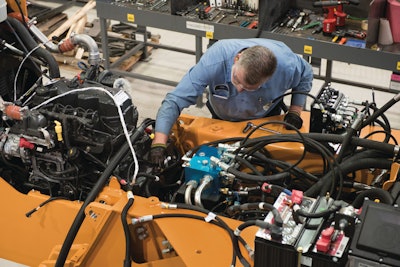
Hydraulic systems operate under high pressure, and hoses and assemblies have a shelf life. When improperly stored, installed and/or serviced, hoses and parts can become damaged and spray hot, highly pressurized fluid that can injure workers and anyone standing nearby.
“Everyone working on or around hydraulic systems should be properly trained in hydraulic system safety,” stresses Stede Granger, OEM technical manager, Shell Lubricants. Working safely with hydraulics largely comes down to common sense, he notes. But everyone, including the experienced operator or service technician, should get back to the basics.
Know What You’re Working With
The basics of hydraulic system safety start with being cognizant of the pressures and temperatures that exist within today’s equipment, says Granger, and the dangers that are associated with them.
“Today’s machines are designed with more bang for your buck,” says Heath Watton, regional manager, Southeastern Equipment. “Over the last 10 to 15 years, manufacturers have been faced with footprint and weight constraints in designing for increased power. To compensate, they have designed hydraulic systems with increased pressure to obtain more power. Everyone wants machinery to be more productive… bigger, faster and stronger. That increased power means increased pressure and heat within hydraulic systems.”
According to Jeff Snyder, industrial brand specialist, Chevron Products Company, fluid in mobile or stationary construction equipment is under pressure ranging anywhere from 2,000 to 10,000 psi at temperatures upwards of 180° F. If the fluid bursts out of a hose, it can burn the skin quickly. Even if it is cooled enough not to burn, additives may exist in the fluid that could irritate the skin.
In addition to the danger of burns or irritation, be aware of the potential for high-pressure leaks. “The velocity with which fluid is forced through a break in a hydraulic hose can be in excess of hundreds of feet per second,” says Snyder.
“Most think of a hydraulic leak as a hose breaking and spewing fluid in a visible spray,” says Ben Briseno, product manager, Citgo. “However, even small leaks can pose a danger.”
While not common, an undetected pinhole leak in a hydraulic hose could act much like a hypodermic needle, injecting hydraulic fluid into any unsuspecting person nearby. Since penetration of the skin can occur at pressures as low as 100 psi, take precautions when working around hydraulic lines by wearing protective equipment (glasses, gloves, etc.). Never use your hands to check for hydraulic leaks.
If an injury has occurred, follow your company’s policies and procedures and seek medical attention immediately. Injections may feel like a pin prick and may not look damaging, but may have life-threatening results if left untreated. When hydraulic fluid enters the body, it begins to kill tissue. Blood poisoning and bacterial infection are also risks if an injury is left untreated.
Visual Inspection is Key to Prevention
Prevention is the best way to avoid a hydraulic system injury. “Every company should have a preventive maintenance program for their hydraulic system. This should be just a part of the whole machine’s preventive maintenance program,” says Snyder.
“Before maintenance can be completed, it’s important to shut off the machine and let it cool down,” he advises. “Retract cylinders, relieve pressure and depressurize all accumulators. Then and only then can a visual inspection begin.”
Snyder prefers to start a visual inspection at the reservoir, which is the “heart” of the hydraulic system. “I inspect the reservoir and areas around it for signs of leaks (pools of fluid). I follow the lines to the pump, valves and conduits and then out to the [working] end of the machine (hydraulic motor, etc.). I look for dirty areas, bad seals, appropriate couplings, etc. Once I reach the working end, I follow the hoses all the way back to the reservoir, making a complete circuit.”
Even out in the field, when time is money and labor is expensive, Snyder emphasizes the importance of taking the time to follow proper precautions. “From a safety perspective, it’s important not to rush into anything,” he states. “Take your time to secure the area and follow the proper lockout/tagout procedures before inspecting the machine.”
Hoses Deserve Special Attention
It’s important to periodically inspect hydraulic hoses. “Pay special attention to hoses known to be in harsh environments or those that are flexed numerous times,” says Granger.
“Check for signs of temperature damage or hot spots on a hose,” Snyder recommends. “Check the general condition of the hose for abrasion, blistering, bursts, nicks or cracks. When you are certain the hose isn’t leaking, check it for hardness and changes in color. Check for dirt accumulation around the fittings or on the hose itself. Hosing should look neat and tidy with no twisting or kinking.” Replace damaged components immediately.
Hydraulic system safety depends on proper hose selection. Hoses are rated, sized and designed for different applications. For example, a spiral hose will be used for a different application than a braided hose. And today’s high-production machines often incorporate hoses made of steel fibers vs. rubberized hoses.
All hydraulic hose is stamped with a manufacture date and maximum working pressure. Replace any hose that has expired with the appropriate replacement hose based on manufacturer recommendations. Also, don’t forget to check fittings. These should be sized appropriately and be free of damage.
“Make sure the pressure ratings of the replacement components are compatible with the system they are being installed on,” Briseno cautions. “Refer to OEM recommendations for the equipment and don’t substitute or improvise with whatever is lying around.”
Pay attention to thread end selection, as well. Manufacturers and distributors offer manuals, tables, thread gauges and seat angle gauges to identify the appropriate coupling.
Avoid mixing and matching hose and couplings from different manufacturers. Each manufacturer designs a coupling to properly fit its own hose manufacturing tolerances. An improperly coupled hose could blow off or leak, causing downtime and possible personal injury.
During installation, be careful not to twist the hose or exceed the recommended bend radius. Use the correct hose length and avoid routes that cause the hose to bend immediately behind the coupling or promote rubbing and abrasion.
Fluid Design and Cleanliness matter
“Having an ideally running hydraulic system is critical to productivity,” says Snyder. It can also have an impact on safe, efficient system performance.
Part of a smooth running system is selecting the appropriate hydraulic fluid for the application. “Hydraulic oils have advanced over the years,” says Briseno. “There are numerous formulations — fire-resistant, water-based and chemical synthetic-type fluids to name a few. There is technology now available from some fluid manufacturers that can improve hydraulic productivity efficiency, which for mobile equipment, equates to more work done per gallon of fuel burned.”
“Hydraulic fluid is a power transfer medium,” comments Mark Betner, product manager heavy-duty lubricants, Citgo. “If the power transfer can be sustained over the work cycle, productivity improves. If the word ‘productivity’ resonates with an operator, and it does in today’s high-production equipment, the design of the fluid matters.”
Selecting the appropriate hydraulic fluid should start with the OEM recommendations for the equipment, Granger indicates. The tendency for machines to run at higher temperatures today means the quality and viscosity of the hydraulic fluid becomes more important than ever.
In addition to the equipment, maintaining the integrity of the hydraulic fluid can help avoid problems. “Hydraulics are the lifeblood of the machine,” says Mark Crews, regional manager, Southeastern Equipment. “Like a person’s blood, hydraulic fluid can’t have contaminants or the success of the machine will be compromised.”
“Contamination of the hydraulic fluid can cause seal leakage and a host of other issues,” adds Betner.
“If a valve contains built-up contaminants, it will no longer perform properly,” says Snyder. “This can cause the temperature to skyrocket because the flow is restricted in the area. It can also cause machine creep after shutdown due to a stuck-open valve.”
“And remember, if it’s leaking out, it can leak in,” he says. “Be mindful when repairing a leak to keep the hydraulic fluid free from contaminants.”