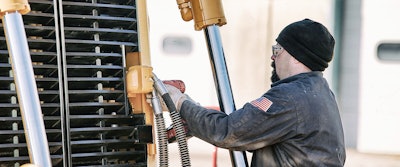
Let’s say you just learned one of your older pieces of equipment needs a costly fix. What’s the smart move: go ahead with the repair, rebuild the machine or pull the plug?
Conventional wisdom says to follow the “50-50” rule: If the cost of parts and labor exceeds 50% of the cost of a replacement machine, it makes more sense to rebuild or replace. But there are other factors to consider. Make sure you consider all of these costs as you run your numbers:
1. Taxes: You pay more in taxes on a new piece of equipment than on a repaired or rebuilt machine.
2. Depreciation: You incur high depreciation expenses the first few years after you purchase new equipment. In some situations, you may be better off repairing or rebuilding older equipment that’s already been depreciated.
3. Warranty: A new machine warranty can help you reduce or avoid future repair costs. Keep in mind, though, that some rebuilt units — like Cat® Certified Rebuilds — come with a same-as-new warranty. That’s a way to keep repair costs under control without replacing a machine.
4. Fuel: Newer models consume fuel more efficiently than older machines. Will the savings you see in fuel offset the cost difference between buying a replacement machine or repairing/rebuilding? It’s worth making the calculation.
5. Disposal fees: There are expenses associated with the safe disposal of an older machine or with choosing to sell it yourself. Make sure you add those fees into your cost estimate.
6. Training: Will you need to spend extra time and money on operator training if you replace older equipment with a new model? One of the often overlooked benefits of rebuilding is that it lets you keep using machines your operators and technicians already know.
7. Technology: Many new machines come with built-in or optional technologies — like grade control, payload weighing, compaction control and more — that increase productivity, efficiency, safety and profitability. The value you gain from these technologies may offset the additional upfront cost of a replacement machine.
8. Production losses: Does this particular machine play a key role in production? If so, lost time is lost money. A repair is generally the fastest way to get equipment back to work. A rebuild takes longer — although typically just eight to 12 weeks — and a new purchase may require additional lead time.
9. Opportunity costs: Do you have the cash flow to replace this machine and fund your other business priorities? If not, it may make sense to repair or rebuild the equipment instead.
10. Competitiveness: Consider how each option affects your competitive position. Will a repair or rebuild keep you at the top of your game? Or would new equipment allow you to bid more jobs, serve more customers and grow your profits?
Here’s one more thing to keep in mind as you weigh your options: financing. Whatever you decide is the smartest move for your business — repair, rebuild or replace — options like these can help you fit the expense into your budget.