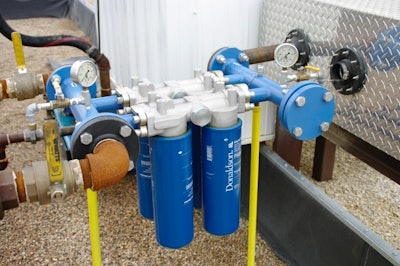
Changes continue to take place in the equipment world, especially when it comes to advancements in injector technology and changes in fuel specifications. While the end results of such changes will be positive with cleaner air being emitted from engines, they can ultimately lead to unnecessary downtime if fuel, oil and lubricants are not filtered properly.
“We see Tier 4 engines being more and more sensitive to dirt and other contaminants that can be picked up by fuel as it makes it way from the refinery to your equipment,” says Scott Grossbauer, Global Director – Donaldson Clean Fuel & Lubricant Solutions. “Just like the saying of garbage in, garbage out, the same holds true with fuel, oil and other materials. If you put dirty fuel or oil in your equipment, ultimately you’ll have breakdowns that cost time and money – far more than the cost of filtering the fluids in the first place.”
Inorganic and Organic Contamination
Fuel contamination can be separated into two broad categories: inorganic and organic. Inorganic contaminant is typically hard particulate (dirt) picked up throughout distribution, Grossbauer explains. From the refinery, fuel is typically very clean, but as it gets transported throughout distribution (which can include pipelines, terminals and delivery trucks), it gets more and more dirty. Once on site, as it’s stored in bulk tanks and moved for distribution and use, it picks up contaminants from the infrastructure as well as ambient conditions.
Organic contaminant represents anything carbon-based, typically hydrocarbons with various chemicals attached. These organic contaminants can also come from a variety of sources at or downstream of the refinery: lubricity improvers, cold flow improvers, biodiesel, corrosion inhibitors, etc.
“It is very important for fuel additives to be dosed at the right levels and under the right conditions to ensure the best overall fuel stability. Otherwise, these additives can become insoluble and therefore 'unfilterable,'” Grossbauer points out.
Generally speaking, hard particulate (inorganic contaminant) will cause permanent damage to the injector system, while softer particulate (organic contaminant) will cause fouling, i.e. deposit build-up on the injectors. In both cases, the engine does not run as designed and can result in a decrease in fuel economy, an increase in emissions and a decrease in power.
Reliability is Key for Businesses
“It’s all about reliability. There are an amazing amount of savings to be realized by keeping fuels and lubricants free of particulates and moisture,” says Scott Dunbar, VP of Filtration, Whitmore Manufacturing Co. “Not only can companies greatly extend the life cycle of critical operating equipment, they can almost eliminate lost productivity due to unplanned downtime. The vast majority of premature equipment failure is related to lubricant contamination. Bringing awareness of the ROI on keeping fuels and lubricants in pristine condition is something we really feel we owe our clientele.”
Today’s Tier 4 engines use high-pressure common rail (HPCR) fuel injection systems that operate upwards of 40,000 psi. These systems require very clean fuel to operate as designed for their entire service interval. Unfortunately, most fuel is dispensed from storage tanks into equipment 500 to 1,000 times dirtier than what is allowed in many injection systems, Grossbauer comments.
Traditionally, only top-quality on-engine filters would be used to remove the contamination in the fuel to meet injection system fuel cleanliness specifications. But the requirements for HPCR fuel are so clean that a two-step approach is needed to maintain service intervals and achieve consistent cleanliness: first, filter the fuel in the bulk storage tank prior to use in the equipment, and then filter again with on-engine filters. Bulk filters should remove contamination in the fuel down to a cleanliness level of ISO 14/13/11, whether the contaminant present is hard or soft. It should be noted, however, that all fuel filters are designed with the goal of removing the hard inorganic particles, so while they will also filter the soft organic materials, filter life may be reduced when excessive amounts of organic material are present.
Besides meeting HPCR fuel cleanliness requirements, the use of bulk filtration also provides necessary protection against any highly contaminated fuel that may be delivered (ongoing or as a one-time occurrence). By filtering prior to use in the equipment, the bulk filtration system will stop excess organic and inorganic particulate from being delivered into equipment’s tanks, ensuring the onboard filters can meet the expected service intervals.
“If excessive fuel contamination does exist, it may plug up the bulk filters, but not the on-engine filters,” says Grossbauer. “This helps eliminate costly unscheduled downtime and makes operation and maintenance much more predictable.”
Clean In, Clean Out
Use of high-efficiency filtration at the inlet of a fuel storage tank infrastructure will help protect against taking delivery of dirty fuel. In addition, adding an effective breather filter on the tank will help combat the entrance of ambient dirt and moisture.
Ensuring fuel is clean prior to storage is a must, but contamination happens within storage tanks, as well. Therefore, filtering fuel as it is being dispensed into the equipment will help safeguard machinery. This will be the last chance to protect against any contamination that may have been introduced in storage – tank scaling, contamination from piping or general fuel/additive stability problems can still exist.
In short, today’s engines – Tier 4 and otherwise – are more sophisticated than ever and require cleaner fuel than ever before. Investing in a bulk fuel filtration system will help protect your equipment against dirty fuel, eliminate unplanned downtime and help you achieve more.