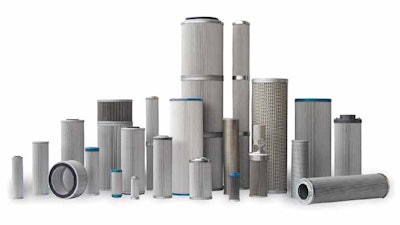
By Sara Jensen, managing editor, OEM Off-Highway
The higher operating pressures of today’s hydraulic systems have greatly increased the importance of filtration within these systems. Pressures of anywhere from 4,000 psi and up make it easier for contaminants within hydraulic fluid to cause damage, while the tighter tolerances of components now being used in mobile equipment make them much more susceptible to damage or failure from contamination.
Just a decade ago, a single filter could keep a hydraulic system clean. Now, most equipment has multiple hydraulic filters, notes Joël Daub, division manager of Hydraulic and Lube Filtration at HYDAC International. He adds that an OEM may even choose to put a high-pressure filter directly in front of a single valve to ensure it stays protected from potential contaminants.
Due to the increased system pressures and component sensitivity, providing finer filtration has become a key goal for hydraulic filter manufacturers. Many are achieving this through developments in new filtration media and improvements to overall filter design.
However, Daub says finer filtration may not be the solution in all situations, such as in colder climates where cold starts can cause dirty oil to get into the system. During a cold start, the hydraulic oil’s viscosity is high, which in turn causes a high pressure drop within the filter element. The high pressure drop opens the hydraulic system’s bypass valve, letting unfiltered oil pass through the system.
To avoid this, Daub says it’s sometimes necessary to use a coarser filter element if the size of the fine filter cannot be increased to reduce the pressure drop. Knowing how a system works and in what application it will be used is vital to selecting the appropriate type of filter.
Marty Barris, director of the Hydraulic Products Group at Donaldson Company Inc., says filter manufacturers have begun to pay more attention to reducing pressure loss because of the potential cold start issues. He says many OEMs have found the premature wear on their equipment can be attributed to unfiltered oil flowing through their systems during bypass events, such as pressure loss during cold starts.
To help combat this, Donaldson developed its Synteq XP hydraulic filter media, which is specifically designed to reduce pressure loss, as well as improve filtration performance. “It’s thermally bonded together rather than with a resin or glue,” he explains. “We can provide the efficiency protection but at a much reduced pressure loss, because we don’t have the glue or resin blocking off many of the pores. We get a much better flow through the media.”
Barris says Synteq XP reduces pressure loss by up to 30%.
Cartridge Filtration
The move toward cartridge filters has been one of the ways manufacturers have started going about meeting the needs for finer filtration and reduced pressure loss. According to Justin Bitner, product specialist with Eaton’s Filtration Division, cartridge filters provide high dirt-holding capacity and low pressure drop characteristics.
Eaton’s Internormen line of cartridge filters, introduced at CONEXPO-CON/AGG 2014, feature six layers of filtration media to help capture harmful particulates. Bitner explains that the two center layers of filter media, made of absolute rated fiberglass, are what provide the filter with its high dirt-holding capacity. “It’s industrial technology,” he says. “But you find the products that were developed primarily for the industrial market are starting to find their way into the mobile markets as system performance and demands increase.”
The increased use of cartridge filters has also been due to the environmental benefits they can offer over spin-on filters. “When you recycle a spin-on element, you throw away a lot of steel,” Daub says. Cartridge filters, however, are typically composed of materials that can be recycled or disposed of in ways that eliminate steel or other metals entering the landfill. HYDAC uses polyamide materials to help reduce the metal content of its filters, and has developed filter elements that can be incinerated.
Donaldson’s FLK medium-pressure filter is a cartridge-style filter featuring a reusable bowl, requiring only the filter cartridge inside the filter to be replaced. The filter cartridge is composed of nylon plastic components that enable it to be incinerated instead of being put in a landfill.
Barris notes that developing more environmentally friendly products is becoming another important design aspect for filter manufacturers. Donaldson continues to look into the use of alternative components, such as using injection molded nylon or plastic construction instead of steel. Customers are also asking the company to use plastic filter media support screens in place of epoxy-coated steel screens.
Donaldson is also looking to use alternative materials in the end caps to which the filter media is bonded. Here again, Barris says the company has switched from steel to injection-molded nylon with many new filter designs.
A Matter of Space
As with many components and systems, hydraulic filters have been affected by the space constraints of today’s machines, partially due to the implementation of Tier 4 engines and aftertreatment systems. Bitner says OEMs want higher performing filters in smaller packages, which has led many filter manufacturers to develop tank-top filters that integrate the filter right onto the hydraulic reservoir.
“We’re even starting to see manufacturers build the filter elements into the reservoirs themselves, which makes an even more compact [package],” Bitner says. “You can’t get any more compact than that.”
Many OEMs are looking to reduce hydraulic reservoir size to save on space needed for Tier 4 engines and aftertreatment systems. This leaves less room within the reservoir for the hydraulic filter. Working closely with OEMs to develop a filter that will fit into their space-constrained designs is key to ensuring a filter will not only fit, but will also be able to provide the necessary amount of filtration, says Daub.
In addition to hydraulic filters, HYDAC manufactures manifolds and valves, which have enabled the company to provide fully integrated systems to help OEMs save on space. “We can integrate the filter element directly into the manifold [and provide] a compact design,” says Daub. He adds that integrating the filter element with the manifold reduces any potential leakage that might otherwise occur because there is less piping between parts. Cost is also reduced because there are fewer components and less assembly time is needed to attach the filter to a system.
Static Standards
One of the many challenges filter manufacturers face is the lack of hydraulic filtration standards that are aligned with real-world conditions. Most of the standards are based on ideal, steady state-controlled environmental conditions.
“The reality is our filters are used in very dynamic environments where there’s engine equipment vibration, surging flow and stopping and starting,” explains Barris. “Being able to understand how our filters perform under that dynamic environment is a real challenge.”
There is a push from both the standards committees and filter manufacturers to change the existing standards and move to a cyclic flow multi-pass test to better reflect real-world conditions. The multi-pass test is one of the key measures of filter performance because it estimates filter capacity and particle separation efficiency as a function of size. “We get a very detailed look at filter performance over its life,” says Barris.
Adopting a cyclic flow standard that incorporates dynamic environments into the test standard, and more closely resembles real-world conditions, is a step in the right direction, he adds.
In the meantime, many filter manufacturers have taken it upon themselves to invest in test equipment that enables them to validate their designs under real-world conditions. Barris says Donaldson has invested in a cyclic flow multi-pass test bench that allows the company to test its filters in dynamic applications.
HYDAC has developed test benches that test filter elements under differing flow conditions. OEM customers send HYDAC the exact flow cycles they are experiencing on their machines so the company can enter that information into its test benches and determine how its filters will perform in that application.
Daub says varying flow can have a major impact on filter elements, and it’s important for the company to be able to develop and test its filters for real-world conditions to minimize degradation. “A lot of applications in mobile industries have varying flow, so we need to be prepared for that,” he states.
In addition, the company has invested in simulation tools to help it see how oil is flowing through a reservoir, as well as how air is flowing through the oil, all of which can have an impact on how filter elements need to be designed. HYDAC will first run various flow simulations on the customer’s existing system to see how things move through the system at different rates. “We look at when the machine is tilted, for example…and try to find where the worst condition is,” Daub explains. “From there, we look at sizing a filter inside the reservoir so we not only filter the particulates, but also make it easier for the oil to get rid of air bubbles.”
After simulations and prototyping, the company works together with the OEM to place a physical prototype of the filter into the machine and test it at HYDAC’s facility or in the field.
Working closely with OEMs is vital to ensuring the correct filtration products are chosen for a given application. Bitner says educating them about the importance of filtration to ensure the longevity of a piece of equipment is key, as well. “Many OEM customers don’t necessarily understand the benefits of using high-performance or finer filtration,” he says. “That’s why Eaton focuses on education through training seminars, webinars, publications — anything we can do to get the message out about the benefits of finer filtration.”
Cost is frequently a determining factor when it comes to filtration. But Bitner says customers often question how much it costs to improve the cleanliness of oil; instead, they should be asking, “What is the cost to me by not adding fine filtration or additional filtration to my machine?”
Keeping oil clean reduces warranty costs, extends the life of equipment and also extends the life of the oil, providing longer service intervals for end users. Working together with OEMs and their customers to educate them about filtration and determine the best filter for their application will ensure they are getting filtration products that meet both their cost and filtration needs.
Article originally published on OEMoffhighway.com