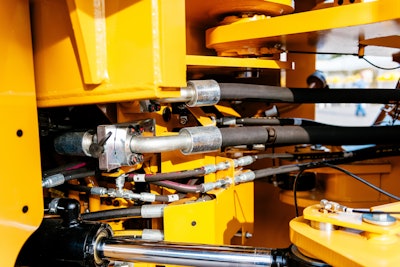
Hydraulic oils are used in many areas of our life, from the telescopic booms of cranes to the control valves in a tractor. These oils are special as they perform a particular function which is unique to them. In addition to the regular functions of an oil, hydraulic oils can transmit power which truly sets them apart. In this article, we will take a deeper dive into the world of hydraulic oils, how they can be used, ways that they should be stored and handled and of course some advancements that we’ve seen over the years.
What Are The Functions of Hydraulic Oils?
Before going any further, we must understand how hydraulic oils function and the impact that they create for our equipment. As per (Pirro, Webster, & Daschner, 2016), the concept of hydraulics revolves around the transmission of force from one point to another where the fluid is the transmitter of this force. Ideally, this is based off Pascal’s Law where, “The pressure applied to a confined fluid is transmitted undiminished in all directions and acts with equal force and at right angles to them.”
As applied to hydraulic oils, once a force is exerted on an oil, the oil can transmit this force to either help an actuator turn or stop an excavator from moving (through braking). This is the transmission of pressure, but hydraulic oils can also provide the functions of reduced wear, prevention of rust and corrosion, reduction in wear and friction and an overall improvement in system efficiency.
For anyone who has worked with hydraulic oils, they will be familiar with the fact that these oils have very tight clearances which requires them to be clean. As they are transmitting power through the fluid, having clean hydraulic oil is essential, so this flow is not disrupted. Since the force will be the same throughout the lubricant, having these tighter clearances allows for more force to be output per square area at the intended target without the contaminants.
Overall, hydraulics will perform the regular functions of an oil but with the added benefit of the transmission of force for these applications. But not all hydraulic oils are created equally and some need to be specifically designed for particular applications within our industry.
Are There Different Types of Hydraulic Oils?
Similar to there being endless types of greases, there are also many types of hydraulic oils specifically designed for certain systems. Hydraulics comprise of lots of different operations as such, they will be called upon to perform in various applications. Some of these can include being fire resistant, biodegradable or even being able to also act as an engine oil. These properties can be influenced by the type of base oil used to produce these oils. For example, fire resistant or rapidly biodegradable fluids or even specialty hydraulic fluids can use PAOs (Polyalphaolefins), PAGs (Polyalkylglycols), POE (ester oils) or other synthetic oils as their base oil.
As per (Mang & Dresel, 2007), hydraulics require special types of additives for their applications. The most important additives for hydraulic oils are:
“Surface active additives” – For hydraulic oils these can be rust inhibitors, metal deactivators, wear inhibitors, friction modifiers, detergents / dispersants, etc.
“Base Oil active additives” – For hydraulic oils, these can be antioxidants, defoamers, VI Improvers, Pourpoint improvers, etc.
Typically, the additives for hydraulic oils can be broadly classed into those which contain zinc and ash and those which do not. Zinc and Ash free oils can represent 20-30% of hydraulic oils on the market and are used for specialty applications where the presence of zinc or ash can hamper the functionality of the equipment.
One such example is the use of these oils in the JCB Fastrac 3000 series for the hydraulic oils. These systems contain yellow metals which can be easily degraded with the presence of zinc or the filterability of the oil can be impacted due to the presence of water. Hence, zinc and ash free oils must be used in these instances.
The following shows a chart of the types of hydraulic fluids as per (Mang & Dresel, 2007) broken down by hydrokinetic applications, hydrostatic applications and mobile systems.
Figure 1: Classifications of hydraulic fluids as per (Mang & Dresel, 2007) Chapter 11, figure 11.9.Strategic Reliability Solutions Ltd.
As seen above, there are many different classifications of hydraulic oils. To provide some clarification on the symbols used in DIN 51 502 and ISO 6743/4, (Mang & Dresel, 2007) produced this table.
Figure 2: Classification of mineral oil-based hydraulic fluids as per (Mang & Dresel, 2007), Chapter 11, Table 11.3.Strategic Reliability Solutions Ltd.
When looking at hydraulic oil classifications, these categories will come up and it is important to be able to understand what each of these mean as well as how it translates to your system. Typically, the most common are the ISO HM and ISO HV.
The ISO HM refers to oils with improved anti-wear properties used in general hydraulic systems with highly loaded components and where there is a need for good water separation operating in the range of -20 to 90°C.
The ISO HV oils are HM oils with additives that improve viscosity-temperature behavior. Ideally, these are used in environments that experience significant changes in temperatures, such as construction or marine, between the ranges of -35 to 120°C.
Are Consolidation and Cheaper Hydraulic Oils Worthwhile Considerations?
Given the various types of hydraulic oils that exist, can they all be consolidated into one hydraulic oil that can serve the purpose for all the applications? The short answer is no, the longer answer is that if there is overlap among OEM recommendations within the same viscosity, then there is a possibility of consolidation. Typically, OEMs will provide guidelines on the oils recommended for use and they should be sought out for these consolidations as they will be more familiar with compatibility issues, as well.
On the other hand, it may mean that the hydraulic storage area of the warehouse has numerous hydraulic oils. In this case, a proper labelling system should be in place to ensure that the correct oil gets to the right location. Since these are specialized, using an incorrect oil (or an oil that does not meet the right specification) can result in disastrous outcomes for the equipment especially for compatibility challenges.
One of the most common issues with hydraulic equipment is the existence of leaks. Depending on the application, some owners prefer not to fix the leaks and use cheap hydraulic oil to keep the equipment working. However, this is not the best practice.
When hydraulic oil leaks out into the environment, this can be hazardous to the people on the site (spills or trips), equipment (skids or contamination) and the environment since it was not disposed of properly. By using cheap oil, this can also damage the equipment even more as that oil may not meet the OEM requirements. In these cases, more harm is being done to the environment and the equipment and there can be significant losses financially and operationally.
This is where the quality of the oil and operations (no leaks) can trump quantity (excess volumes of cheaper oil). Unless the leaks are fixed, then the volume of cheaper oil will continue to increase and there will be additional labour costs to constantly maintain the sump levels as well as delays to the project.
Therefore, the overall impact on the efficiency of the hydraulic equipment will be reduced. However, if the leaks are fixed and a quality hydraulic oil is used, then the machine can operate more efficiently, complete the assigned projects and possibly even reduce extra labour costs related to maintenance.
Ideally, consolidation can be achieved as long as the OEM requirements are being fulfilled. However, cheaper oil that does not meet the required OEM standard for a particular piece of equipment is not an ideal option as it can cause more harm than good in the long run.
Storage and Handling
Hydraulic systems have smaller clearances than many. As such, it is imperative that these oils be kept clean and free from any debris. Most hydraulic components have a required ISO 4406 rating that should be met to ensure that the oils do not allow foreign particles to enter as these can easily clog the clearances and cause the system to stop working.
Chevron Lubricants produced a document that compiles some ISO 4406 codes for various types of industrial off highway equipment, which also includes the hydraulic standards. It noted the recommended ISO Cleanliness for John Deere hydraulic Excavators can be ≤23/21/16, this can be found here (Chevron Lubricants, 2015).
Hydraulic oils should be pre-filtered before being placed in your equipment even though there are filters on the inside of the equipment by reducing the amount of contamination entering the system from the onset, you can ensure a longer life for your hydraulic oil. Hydraulic oils should also be stored in closed containers not those that are left open to the atmosphere!
Advancements in Hydraulic Oils
According to CITATION Fit21 \l 1033 (Fitzpatrick & Thom, 2021), the hydraulic oil market was approximately worth USD 77.5 billion by the end of 2021. Mobile hydraulics account for 65% of the market while industrial equipment represents 35% of the market. Clearly, the larger market share exists for mobile hydraulics. However, OEMs are also moving towards smaller oil sumps with longer oil drain intervals that can impact on the volume of hydraulics needed periodically.
Changes by OEMs also impact the formulation of hydraulic oils. For instance, if a smaller sump is used then, the hydraulic oil must now be able to cool faster, transport the same (or larger) force and maintain the intended viscosity of operation while being under greater stress. In these cases, the additive packages involving the antiwear, thermal stability, viscosity index improvers, defoamants and dispersants must be formulated to work in unison without compromising the other.
There have been changes in additive technology that allow for larger tolerances for various characteristics but while additives are evolving, the refining of base oils is also trying to keep up. With all of these evolutions, the chemical composition of hydraulic oil today vastly differs from one created in the 1950s. The requirements of hydraulic oil have also greatly evolved, forcing these changes in formulation.
Hydraulic oils today need to provide longer oil drain intervals, better stick/slip characteristics, increased efficiency, improved conductivity and wear performance and an added level of sustainability. Formulators need to create hydraulic oils that can adhere to these characteristics while also not infringing on regulatory requirements. This makes hydraulic oils one of the most powerful types of oils because they must conform to these requirements while also transferring force from one place to another.
References
Chevron Lubricants. (2015, January 24). Chevron Lubricants Latin America. Retrieved from Chevron Lubricants: https://latinamerica.chevronlubricants.com
Fitzpatrick, A., & Thom, M. (2021, November 08). How the Global Hydraulic Fluid Market Is Changing—And What It Means for the Future. Retrieved from Power Transmission Engineering: https://www.powertransmission.com/blogs/1-revolutions/post/189
Mang, T., & Dresel, W. (2007). Lubricants and Lubrication Second Edition. Weinheim: WILEY-VCH.
Pirro, D. M., Webster, M., & Daschner, E. (2016). Lubrication Fundamentals, Third Edition Revised and Expanded, ExxonMobil. Boca Raton: CRC Press, Taylor & Francis Group.