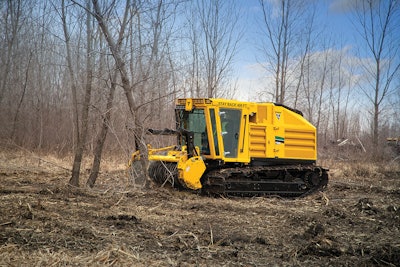
Selecting and maintaining a mobile mulcher can be a little more involved than it first appears. There are many choices that have a direct impact on performance, uptime and ROI.
Technical advances in mobile mulcher tractor hydraulic systems have resulted in higher flows and pressures. “The need to maintain the systems that operate these machines has become ever more important due to the increased hydraulic flows and pressures that the machines create to be efficient,” says Rob Haines, sales representative, Bron.
This has also made it critical to match the proper attachment to the tractor. “Looking beyond necessary safety guarding of the tractor, matching the mulcher attachment and the tractor can play a significant role in the return on investment,” says Mike Slattery, Fecon. “The mulcher industry has evolved significantly over the past 11 years to provide many choices that make it possible to tailor equipment to specific needs. On the mulcher attachment, buyers and renters should look at rotor diameter, type, tools, rpm and bearing size, [and the] type and size of hydraulic motor (unless it will be on a PTO tractor), mulcher width and mulcher weight.”
Hydraulic failures are one of the most common reasons for downtime. “When researching mulchers, keep in mind that higher hydraulic flows in combination with high pressure can result in a shorter life of the main hydraulic components,” says Jeff Bradley, Recycling and Forestry product manager, Vermeer.
Hydraulic systems on mulchers face multiple demands. “The tracks or wheels of the machine are used frequently, while the attachment pumps are steadily working to drive the mulcher rotor,” says Slattery. “This means two significant hydraulic circuits are drawing from the available engine power simultaneously and steadily throughout the day.”
Couple this with the material generated during the mulching process and it places higher demands on hydraulic cooling. Be sure to clean out debris to keep temperatures under control and prevent possible fires.
“Mulchers are dynamic machines that require attention in order to prevent costly downtime,” says J.R. Bowling, vice president, Rayco. “Common issues we find are that operators don’t inspect and/or clean the cooling systems, debris screens and belly pans. As a result, the machines tend to run hot and experience overheat shutdowns, oil leaks and component failure. The operators can easily prevent these issues by making inspection and periodic cleaning part of their maintenance routine.”
Haines agrees, adding, “Ignoring engine, hydraulic and powertrain maintenance will quickly lead to extreme costs with early failures in these high-demand machines.”
Pay Attention to Cutting Edges
Different mulcher tool options can have a dramatic impact on performance and tool life. “Consider jobsite conditions including abrasiveness of vegetation and soils, the amount of rock or foreign debris that is present and the type of vegetation,” advises Slattery.
Most brands will offer tool options such as standard carbides and knife tools (also called planer tools). “Standard carbide tools provide a good all-purpose solution balancing wear life, durability and productivity,” says Slattery. “Knife tools are used for faster cutting and finer sizing in fewer passes. Some brands have other options including more robust carbide tools for extremely rocky or abrasive conditions.”
“Matching the tip style to the material type being processed is a good way to help you get the maximum longevity and productivity from a mobile mulcher,” says Bradley. “Determine what material type will be processed and match the mulcher head features to maximize productivity. If you will be mulching larger diameter materials, then a planer-style mulching head with depth control rings can help decrease your time to process the larger material, and provide a more controlled size of mulch product left on the ground.”
An item as simple, and overlooked, as changing tools (teeth) can have a major impact on uptime and machine life, as well. “Changing teeth will help reduce fuel consumption by keeping teeth with good cutting edges so mulching operations happen easier,” says Haines. “Changing teeth as needed also helps keep the mulcher drum in good balance, thus reducing unnecessary vibration and shake into the machine. Unbalanced drums will virtually shake a machine apart.”
Weigh Dedicated Mulchers vs. Attachments
There are both advantages and disadvantages when it comes to a dedicated mobile mulcher vs. an attachment. “If the head is dedicated to the tractor, that means it has been designed specifically for the tractor,” notes Bradley. “It also means the tractor is more likely to have a more rugged design with required safety features built specifically for the forestry application.”
As J.R. Bowling, vice president, Rayco, points out, dedicated units are built to stay cleaner, run cooler, provide more cutting power, be more durable, have safer cabs and be easier to maintain than, say, a compact track loader. “They also have features like hydraulic winches and heavy-duty guarding built into their design, not added on as an afterthought,” he states. “If you are going to be mulching most of the time and using other implements occasionally, then chances are you will benefit from a dedicated mulcher. There’s simply no compact track loader, tractor or skid steer out there that is designed to hold up to the rigors of mulching on a day-in, day-out basis.”
Where attachments are popular is when you want to maximize utilization of a tractor and do not have enough work to keep a dedicated mulcher tractor busy. “The largest advantage [of] using an attachment on a carrier as opposed to a dedicated unit is the ability to use that carrier for other jobs when the mulcher is not needed,” says Lee Smith, product manager, FAE USA.
“Both solutions work, so it is a matter of defining the needs of the operation first,” says Slattery. “The attachment solution often means a mulcher will be mounted on a carrier that is capable of running different attachments, which provides versatility. They are not necessarily equipped as standard with appropriate forestry guarding or, in some cases, cooling capacity.
“In many cases, these carriers are less likely to deliver as much available engine power to the mulching attachment when compared to a purpose-built... mulching carrier,” he continues. “But going the attachment route often comes at a lower cost of entry and greater versatility for the buyer.”
Match Attachments to the Task
A proper match between the mulcher attachment and carrier is critical. “If you have a heavy-duty attachment that needs high flow and high pressure attached to a low-horsepower, low-pressure unit, you will cause issues with the carrier,” Smith explains. “On the other hand, if you have a weaker built head on a high-horsepower, high-flow unit, it will quickly cause structural issues to the attachment.”
Choosing the best mulcher attachment for your operation is an important decision. “First, you need to identify what the requirements are for your work,” says Bradley. “For example, what size material is acceptable to be left on the ground? Next, you need to identify all the possible ground conditions that you may be working in and ensure the mulching head has the ability to perform in these conditions. This may be as simple as changing between a planer-style tip and an IR hammer tip.”
It’s necessary to determine the correct head style for your application. “Generally, there are two mower head styles: rotary-style mower decks, often called ‘brush hogs,’ and drum-style mulcher heads. There are varieties of each style,” says Bowling. “No matter which style you choose, select a mulcher attachment that fits the carrier both in terms of size and weight, as well as the drive type (hydraulic, PTO, etc.). The next consideration is the tooth/knife setup. This is often a matter of considering the types of vegetation that will be cleared, as well as the ground and soil conditions.”
“Matching the tractor to the mulcher is a critical step in the process to help reduce the possible hydraulic component failures due to higher flow or pressure than what is recommended for the mulching head,” says Bradley. “The tractor will have a similar cost of operation regardless of what head is installed. Therefore, it is important to match the hydraulic capacity of the head closely with the hydraulic capacity of the tractor to get the best possible performance.”
The work to be performed drives the proper match of attachments to power units. “For example, the requirements of the machine to work in softwoods, hardwoods or scrub brush are all very different,” Haines points out. “Proper matching of horsepower to mulching head will have a direct effect on productivity and longevity of machines. Purchasing a small machine to do large-scale work will take a very long time and the life of the machine could be shortened due to the high demands on that machine and working it over capacity. The opposite is true for large machines, as buying a large machine for small work will have a high initial cost and much more work will be required to keep it busy.”
Physical dimensions also come into play. “Overall machine dimensions may dictate the unit used to accomplish the required work,” says Haines. “Width of the area to be cleared will determine the size of the machine required.”
“When it comes to overall width of the mulcher, most operators prefer the mulcher at least cover the width of the tracks or wheels,” says Slattery. “Of course a wider head means more weight, so also consider the lifting capacity of the tractor and how balance may change as the mulcher is raised through the entire range of motion. If the balance is not reasonably maintained... an increase in ground pressure could result in one area of the machine. That could lead to greater ground disturbance or sinking to the point of getting stuck.”
Double check the tractor and attachment specs to ensure compatibility. “Rotor diameter, type, tools and rpm should be compared with tractor horsepower and hydraulic flow and pressure, balancing available power with rotor inertia, material intake and cutting efficiency,” says Slattery. “Where the mulcher is hydraulically powered, the motor size and type should be compared with available power, as well.”
There are different hydraulic motor options available. “The industry has for the most part standardized on variable-speed motors that present a balance of torque and speed to the rotor, automatically adjusting under different load conditions for maximum production,” says Slattery. “But it is important to have enough displacement and to have the proper shift point in the variable motor to get the best performance.
“For example, there is greater torque potential in a skid-steer application with a 107cc variable-speed motor vs. a 70cc variable-speed motor,” he elaborates. “Both can achieve high-end rotor rpm under lighter loads. But as hydraulic pressure rises and the motor shifts to maximum displacement, the available torque of the 107cc motor will be measurably higher.
“Going further, the motors typically shift based on a specific pressure setting by the manufacturer,” he continues. “Shifting too early or too late can have a big impact on performance. Getting that right depends on tractor variables, including the available flow, maximum system pressure and available horsepower. This can be different based on the type of rotor technology in the mulcher, as well. For example, a depth-controlled rotor is often run at higher rpm than a smooth drum rotor.”
Understand the Trade-offs
Make sure you really understand all of the variables that impact performance and enlist the help of industry experts.
“People are sometimes told one type of rotor is better than another, that motor size does not really matter, or that knife tools are the best and only option,” Slattery comments. “Such claims are simply not true and cause first-time buyers great confusion. It is best to start working with sales representatives that ask what your needs are.
“Any mulcher will mulch, but things like rotor and tool type can make a big difference in performance and price,” he adds. “Carbide tools vs. knife tools are one of the big discussion points. Smooth drum rotors vs. depth control or bite limiting rotors are another important discussion. Motor size and type significantly impact performance and price.”