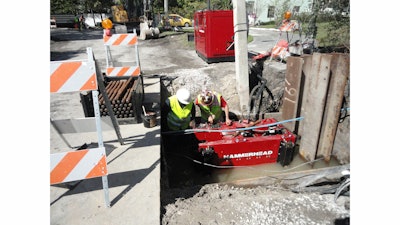
When periodic maintenance could no longer keep the storm sewer system of Biscayne Island at full functionality, the Miami Office of Capital Improvements & Transportation Program scheduled its vitrified clay and concrete pipes for replacement. Though the system could still handle most small storm events satisfactorily, Miami officials wanted to ensure the pipes would continue to manage severe storm events, as well.
Due to the proximity of the existing buildings to the outfall pipes, the resulting drainage improvement plan specified pipe bursting replacement technique. The office considered the possibility of using pipelining to extend the life of the existing pipes, but it was not feasible in this case. So the project was spec’d out for pipe bursting only.
Maggolc Inc. was contracted to upgrade three 100-ft. storm sewer runs to 12-in. HDPE as part of a larger upgrade project, which included replacing all storm sewers for the island residential community in Biscayne Bay, rebuilding affected streets and upgrading street lighting. One of the existing storm sewers was vitrified clay pipe and two were concrete. Maggolc brought in US Sewers and Drain, specialists in trenchless techniques, which then contacted Trenchless Equipment of Oconomowoc, WI.
John Hrabosky, a representative for HammerHead, visited the site personally. “I needed to see what we were going to come across, the landscaping, the homes and such. Access was tight,” he says.
The storm sewers passed from the community’s street beneath the ornate lawns, through protective property walls and under the seabed. The project needed to be completed with minimal impact to the posh residential properties.
By IPBA standards, this was a Class A project: three 12-on-12 runs less than 350 ft. long at less than 12 ft. deep. The varying tidal cycles of a salt-water environment categorized it as experimental technique under Class D conditions. The most significant factor was that the pulling machine pit, or “working pit,” would be under water. Hrabosky recommended the static pipe bursting method with a HammerHead Hydroburst HB100 100-ton pulling machine and a 15-in. OD expanding head for the 12 in. IPS HDPE replacement pipe.
Pipe Bursting 101
The pipe bursting method gets its name from the fracturing that takes place as the expander head, which is larger in diameter than the existing pipe, ruptures the pipe as it is being pulled or driven through it. In this Biscayne Bay project, the head was pulled through the pipe using pull rods that were joined together and payed out from a stationary pulling machine in a pit dug at the storm sewer in the street.
The pipe is drawn in place behind the expander head. As the pipe ruptures, its pieces are compressed into the ground surrounding it. Using a larger diameter expander head reduces the force necessary to overcome friction against the replacement HDPE pipe during the pull.
In a dynamic pipe bursting, the head is driven through the ground with a percussive pneumatic hammer. Hrabosky says the pneumatic technique would have worked as long as positive air pressure was available to keep water out of the hammer, but going with hydraulic over pneumatic “was a sure-fire choice for this job.” The location for the working pit was only 4 ft. above sea level. To minimize the possibility of airflow being interrupted, they would normally pump the pit, but trying to pump a pit dry this close to the ocean would be futile.
However, immersion isn’t a problem for HB100. “HammerHead’s pulling machine doesn’t have any electronics or electric controls on it to worry about,” Hrabosky notes. “There was never a doubt that it would work in the wet conditions at Biscayne Bay.”
A Burst of Activity
The ocean end of the storm sewers was 3 ft. below the sea’s surface, so no entrance pit was required in this application. Restricted to working at low tide, however, the crew had relatively short work windows for completing the three pulls. At most, they would have six hours for a pull, only one pull to a shift.
Since compression along the moving expander head causes a temporary swelling of the surrounding ground, the crew also needed to chip away clearances in the seawall large enough to prevent impact to the wall.
HammerHead called pipe bursting specialist, Mark Maxwell, to be on hand for the pull. For jobs with multiple runs, Maxwell will usually instruct the crews and then serve as a standby consultant. In this instance, since the crews were unfamiliar with the equipment and because the precision required for these pulls left no room for error, group consensus was that Maxwell would serve as primary operator throughout.
Maxwell says he had the easy part, since most of the work for a pipe burst is in the preparation. Once the HB100 was set in the pit, it took Maxwell just 20 to 30 minutes to pay out 3-ft. lengths of pull rod from the machine to the end of the existing VCP.
After the 100-ft. lengths of HDPE had been fused onshore, their ends were plugged to make them buoyant, allowing them to be floated into place at a preparation barge. An excavator aboard the barge lifted and held the HDPE in place as crews made the connections.
The burst required at most 15 tons of the HB100 pulling machine’s full 100-ton capability. Pulling the expander head and replacement pipe through the sewer took a half hour or less. Restoration required the repair of the seawall where it had been chipped away to accommodate expansion and backfilling of the working pit. Maxwell calculates total time of the project dedicated to the pipe bursting operation at “just under a half hour to pay out, another 20 minutes to pull back, per run.”