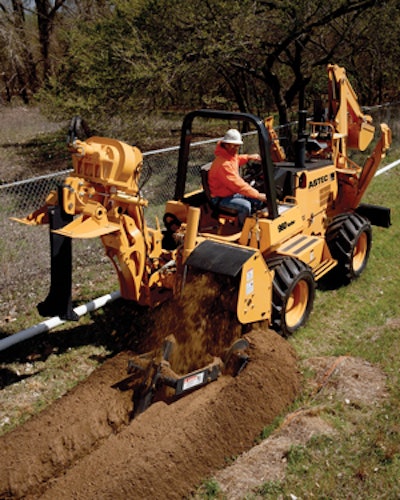
Many variables dictate what trencher configuration is best suited for the task, including depth of cut, length of run, size of the product being installed, local ground conditions and space on the jobsite. You must start with the correct size machine - whether it's a walk-behind or ride-on unit with wheels or tracks - then choose the correct chain, cutting teeth and boom configuration. Next, select attachments that maximize your productivity.
Ground conditions and trench dimensions dictate the correct trencher size. "The more difficult the soil conditions, the more powerful the trencher should be," says Tim Phelps, product manager, Barreto Mfg. The depth and width of cut also affect trencher size. "For example, the deeper and wider the trench, the more earth you are taking out of the ground and the more power and size you want in your trencher to make the job easier."
Length of runs and frequency also affect choice, he adds.
When it comes to trenchers, bigger isn't always better. "You can rent a larger machine and get the work done faster, but it will cost you more. So you have to consider the budget as well as the application," Phelps states. "You also have to consider the size of the area. A smaller trencher is easier to maneuver than a larger one, and easier to transport to the jobsite."
Sizing it up
The smallest of the horsepower range is filled with walk-behind trenchers. "Walk-behind trenchers are limited in dig depth and width," says Bob Wren, training manager, Astec Underground. "However, they play a large role in the total unit sales of rubber-tired trenchers. Walk-behinds may be as much as 50% of the overall market in the 10- to 115-hp range."
According to Jon Kuyers, rubber tire and compact segment manager, Vermeer Mfg., "Most walk-behind trenchers effectively trench 24 to 48 in. deep and 4 to 6 in. wide. They are somewhat limited, as they do not have backfilling capabilities, and are smaller in size and horsepower for tough conditions.
"The advantages they have are maneuverability and overall size to get into confined areas," he adds.
Stepping up in capability are the ride-on trenchers. "Rubber-tired trenchers are mostly used for utility installations such as water, power, telephone and gas," says Wren. "Most utility companies, depending on their given area, use between 50- to 100-hp machines."
The largest trenchers are especially beneficial on longer runs in tough soil conditions. "If the utility runs are significant in length or in difficult soil conditions, such as frozen ground or caliche, more horsepower - which increases the overall size of the machine - will be required for greater productivity," Kuyers notes. "However, job limitations, such as a narrow right of way or confined areas, may require a machine with lesser horsepower that will complete the job, but not as productively."
But wide trenches require more than power to drive the cutting chain. "The larger trench widths or increased depths require greater horsepower to dig productively, but also require greater spoils-handling capabilities," says Kuyers. "The deeper or wider cuts will also require greater auger lengths or conveyors to remove the material farther away from the trench line. Along with increased depths or widths, harder soils will require more horsepower, especially when incorrect cutting tools are used."
Proper sizing really boils down to a few basic questions, according to Wren. "How deep do you always dig? How wide do you dig most of the time? How long are the longest runs going to be?" he asks.
Consult with your dealer when answering these questions, because local soil conditions also impact power requirements. "They should be familiar with some of the local conditions that you might be getting into," says Brent Bolay, the Ditch Witch organization.
Set up for conditions
Make sure the trencher is set up appropriately for local ground conditions. "If you walk into a dealership in Central Texas vs. one in Iowa, they are going to have the trenchers set up to compliment their local area," Bolay points out.
You will need to determine the most appropriate boom configuration. For example, Ditch Witch machines come with a choice of booms. "Typically, a standard boom would have a sprocket on the bottom side of the boom where the chain comes around," says Bolay. "If you are in particularly rocky conditions, that sprocket sometimes has a tendency to get a rock in it."
A specialty boom featuring a large tail sprocket on the end with enclosed sides eliminates this problem. "You have a wear bar strip down the bottom of the boom that the chain actually runs against," Bolay notes. "You don't have any sprocket to interact with the rock."
When it comes to digging chain, make sure you know what you are getting. Not all digging chain is created equal. Consider basic measurements such as tensile strength. "We rate on the weakest link of the chain," says Bolay. "There are some other people that rate on the strongest link. You just need to understand what the rating is tied to."
Some manufacturers offer unique features in the digging chain design. "We hold a couple of our own patents," says Bolay. "We provide extra material along the bottom side, as well as the heat treat process that we use on the pins."
In terms of teeth, there are many options. Tooth styles include rock, dirt, shark and bullet. Each style is designed for a specific soil type, ranging from gummy and sticky soils to hard and rocky soils. You may find you need to change teeth periodically to match conditions. "It is not terribly hard," says Bolay.
Obviously, no single trencher configuration will meet every ground condition and application you are likely to encounter. "We always want to choose a machine that will do the customer's work most of the time," says Wren. "This only means that, during some applications, a customer may have to use a longer or shorter boom and maybe a different chain line setup."
Attachments add function
Certain types of attachments are more prevalent than others when it comes to trenchers. For example, the backfill blade has practically become standard on ride-on models. "We have moved almost into 100% application," says Bolay. "We don't consider it an option on a machine anymore. We build them with a backfill blade. It is a nice support tool to have."
Backhoes have also proven very popular. "They will be selected about 50% of the time with the equipment," says Bolay.
Vibratory plows are another common option. But keep in mind there are limitations on the size of material they can install. "The vibratory plow is real popular when the installation is small diameter pipe or cable that is fairly flexible," says Bolay. "[Once] you get into the larger pipes, you just can't physically get them down into the ground."
Availability of other types of attachments really depends on the tractor. "The attachments are designed and balanced to match the horsepower, hydraulic and structural capabilities of the tractor," says Kuyers. "The larger the attachment and its capability, the larger the tractor [needs to be]."
"At about 40 hp, we start offering different attachments," says Bolay. Attachments such as rock saws just aren't practical below this range. "[It won't cut] as deep and you can't tackle quite as rough of rock conditions as you can with the larger machines."
When selecting attachments for your trencher, take into account soil conditions and other jobsite factors that can influence which attachment will be most productive for your particular situation.
"Attachments will vary in popularity by region, as soil conditions are different," Kuyers comments. "Rock wheels may be more prevalent where solid rock is present, or plows may be popular where there is limited utility congestion and loose soil types. Backhoes are a popular option where there is utility congestion or when existing utilities need to be located."
Time of year can also be a consideration. "We have customers that use a backhoe/trencher in the winter and switch to a backhoe/plow combination in the summer," says Wren.
Wheels vs. tracks
Tires and tracks offer trade-offs that need to be carefully considered.
"Tracks will provide greater flotation (lower psi), stability and tractive effort than most conventional wheeled units," says Kuyers. "Tracks are most advantageous when the ground is muddy or when traction is poor for wheels. They will extend the amount of days that can be worked and without question increase productivity in most applications, which we have validated with our RTX quad track tractors. While tracks may cost more, they offset the increased price with this increased productivity. However, if the unit is going to be working in areas where traction is not an issue, then the wheeled units would be the most economical choice."
Tires are sufficient for most applications. "Today, by far, the most popular units are on rubber tires," says Bolay. "As a general rule, the rubber-tired units are cheaper to operate. They really do provide fairly good traction across a varying set of ground conditions."
Repair and replacement costs can also be a consideration. "A lot of times when you have a tire problem, it is one tire. Where on a track, it is a bigger dollar expenditure at the time to make a change," says Bolay.