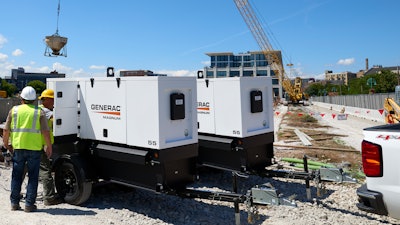
Traditionally in prime power applications, you choose a single generator with enough power output to operate all of the tools and equipment needed on a jobsite. However, operating several smaller generators in parallel might be a more efficient and versatile solution.
Paralleling is when two or more generators are electrically coupled together using special equipment to form a larger capacity power source. If the two generators are the same size, it effectively doubles the power output.
“The basic premise behind paralleling is to take two generators and connect them together in such a way that they combine their output to make a theoretically bigger generator,” says Todd Howe, Manager - Global Generator Products, Doosan Portable Power. “In the air compressor world, that is pretty easily done. You take the hose that is coming out of the air compressor that is producing the flow and pressure and you manifold those together. If you have two 200-cfm air compressors, putting the two together would give you 400 cfm.
“In the generator world, it is a little more complicated,” he continues. The generators need to be synchronized. To do that, the control systems of the generators need to “talk” to each other. “We are trying to get both generators to be producing the same voltage and frequency, and probably of most importance is to get them to produce the same phase angle, which basically means that the sine waves that the generators are producing peak at the same time. If the generators fall out of synchronization, you are more likely going to damage one of them or have one of them stop producing power and start importing power.”
You can also set the percentage of contribution from each unit. “You have controls that are capable of being set so that each genset that is paralleled will have a contribution toward the total power of the application,” says Luis Navarrete, director of engineering for Generac Mobile Products. Load management and power sharing allow you to assign how much power each generator produces.
Digital Control Simplifies Parallel Capability
Paralleling generators isn’t a new concept, but it has been simplified with microprocessor controls. “You need to manage the same electrical parameters whether it is a newer or older machine,” says Navarrete. “The difference is the newer machines will be more user friendly. The controls are going to be easier to use and will do things more automatically with fewer manual settings. It is more plug-and-play.”
Many capabilities are now built in. “Paralleling generators used to require large, cabinet-size switch gear and manual interaction,” says Ben Froland, product manager, Wacker Neuson. “Modern paralleling generators benefit from sophisticated electronic controllers that do most of the work. Other than the controller, the only other features needed are a motorized breaker and a data line to allow the generators to talk to each other.”
These advanced controls simplify what used to be very complex. “That is the big reason why paralleling is becoming more mainstream, particularly for rental companies,” says Howe. “It has always been a great tool that offers a lot more flexibility, and it helps provide better performance in certain applications like events, concerts and T.V. production, where you need power redundancy. Having two generators running together would also give you power if one of those machines goes down if you had a fault, without disrupting the event. That has been a very common application historically, but now we are finding the same benefits flow over into other applications like oil and gas for similar reasons.”
More manufacturers have started offering paralleling controls as part of their catalog offering. Howe notes that Doosan has offered paralleling as an option on certain models dating back as far as 2010.
The offerings continue to expand. Where once offered only at the top of its portfolio, Doosan’s customers are now requesting paralleling capabilities in smaller units. “We are starting to see demand for paralleling increase down into the middle range of our portfolio,” says Howe. “I predict it’s going to be commonplace down to about 150 kW.”
Many different types of generators can be paralleled, as well, even older models. “It is possible to parallel a microprocessor-based controller in a new-generation genset with a very old mechanical genset,” says Navarrete. It just takes a lot more effort to set up.
No matter what type of paralleling setup you choose, it’s best to have it set up by a skilled technician. “As you are putting these gensets together, you are going to [want to] have a knowledgeable person come to the site and make sure the phases and the voltages are aligned and everything is running properly,” says Navarrete.
Once that is done, the new controls allow any operator with experience to run the system. “They have become more fail proof,” Navarrete states. “If you do something wrong, the machine will just not let you do it. All of the functions are now more automatic.”
Pros of Paralleling
Paralleling offers several benefits, according to Froland. For one, it can be used to link small generators together to perform like a larger one. There are a number of reasons to do this, including:
Greater utilization: Several small paralleling generators can be rented out individually for smaller applications and sent out together for larger applications.
Redundancy: If the application cannot be interrupted, two generators can be paralleled to operate at 50% load. Should one generator fail, the second generator will pick up the other 50% load without any loss of service. Redundant generators can also be set up to balance engine hours and to take turns shutting down for maintenance while maintaining the load overall.
Motor starting: Motor starting applications require a great deal of current to start and then taper off once the motor is running. This can lead to oversizing of the generator and problems such as wet stacking. If paralleling generators are used, two generators can perform the starting and then one can shut down to allow the other one to run fully loaded.
“It is all about load management,” says Navarrete. “You may need 1 MW of power at peak, but then at some point your base load goes to half of that. There is no real need to have a 1-MW machine running when it is not being used completely and then having to deal with the additional fuel and wear and tear. [Paralleling] let’s your supply flex up and down depending upon the demands and requirements of the load.”
This lets fleet owners standardize on a common size of genset and use paralleling capabilities when more power is required. “You may have a fleet that wants to standardize on a certain size machine because that makes the most cost-effective maintenance cycles and cost of ownership,” says Navarrete. Paralleling allows fleet owners to achieve better utilization.
In addition, sophisticated controls allow functionality such as power management. “This is where you have an array of generators connected together in parallel and the control system is smart enough to determine, based on your load, which generators it should operate to optimize fuel consumption,” says Howe. “Let’s say you had four generators in parallel and you can run that job with two generators. The control system would notice that and elect to shut off two machines. If demand increases, it will bring a third machine back online and ultimately the fourth machine back online. You will not only burn less fuel, but you will run fewer hours on those generators.”
This allows generators to run more efficiently. “You need to be at least 30% loaded to have good, consistent, reliable operation,” says Howe. “There are a lot of generator applications where that is unrealistic 100% of the time.”
“Paralleling is certainly one of those technologies that can help with varying loads,” says Froland. “With multiple paralleling generators on site, the customer can be assured that the number of generators running matches the load appropriately. If reacting to a non-linear load is a concern, the newer Tier 4 Final engines respond faster than any previous generation of engines. Variable geometry turbos and high-pressure common rail injection with electronic control make for very quick response to changing conditions.”
Potential Drawbacks
But paralleling does have its downsides. “It is still a more complicated control system than a basic analog generator,” says Howe. “If you have very simple construction applications — running well pumps or water pumps, job trailers or traditional commercial construction activities — sometimes these types of jobs are best suited for a simple machine with an easy-to-use control system that is more geared toward operators who are looking just to push a button to start and push a button to stop.
“The level of sophistication and control with a paralleling system ratchets up the complexity a good bit, and it is not necessary for every application,” he adds.
The other drawback is that the functionality and capability of these control systems adds to their cost. “Motorized breakers and paralleling controllers are significantly more expensive than their conventional counterparts,” says Froland. “In advanced paralleling applications with the grid, additional switchgear located off the generator may also be required.”
While the size of generators with paralleling capability has been decreasing, there are still size limitations. “The reason we are not seeing paralleling down into smaller units is simply that the cost/benefit isn’t there,” says Howe. “It is easy to take a 20-kW machine and switch it out for a 40-kW machine. They are similar in size. They are similar in rental rate. It is easier to take a simple machine and apply it correctly in an application as opposed to relying on a paralleling solution with the small machines to avoid that cost and complexity. Right now, 150 kW is where the bar is set.”
Generac offers paralleling capability down to 75 kW. The technical limitation to size is driven by engine size. “Smaller engines are typically harder to parallel because they are less stable speed wise,” Navarrete acknowledges. “Controlling power with load management is directly affected by your ability to control the engine speed. For us, the balance between performance and cost is 75 kVA.”
There is an exception to the general sizing rule. Many smaller inverter generators offer paralleling capability. These units typically offer 2,000 to 7,000 watts and can be connected in parallel to double their output up to 14,000 watts. This is because inverter generators rely on DC power, which simplifies paralleling.
“The inverter electronics makes it a plug-and-play affair to daisy chain those units together,” says Howe. “Those units do not have to synchronize. It is more like my air compressor analogy. You just plug those units together to increase capacity.”
Regardless of generator type or size, seek expertise if you think paralleling may be right for your jobsite. Specialized rental companies focused on the generator market more than likely have generators that can be paralleled. They will also have specialists who know how to properly apply these generators for various applications.