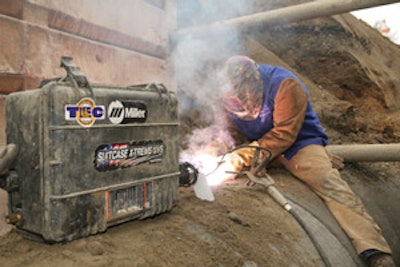
Don Knight
Seven years ago, Lyle Proctor started DDJ Welding, Enumclaw, WA, a firm specializing in welded steel pipelines for the water industry, including hydroelectric dams, local water lines for utilities, pen stocks and power houses. In addition to himself, Proctor regularly employs four or five other welders, equipping them with completely outfitted work trucks. Some years, however, demand increases to the point where as many as 15 welders are needed.
DDJ Welding has Miller Electric Trailblazer 275 DC gas engine-driven welders on two of its trucks. With a peak generator output of 10,500 watts and a welding output of up to 325 amps (300 amps at 100% duty cycle), the units can weld with larger diameter electrodes and gouge with larger carbons (up to 1/4 in.).
"We run a lot of 5/64-in.-diameter E71T8-K6 self-shielded flux cored wire," says Proctor. "On larger diameter pipe, from 48 to 96 in., we will have an arc-on time of 15 to 20 minutes as we weld from the top down to the bottom of the pipe. Our Trailblazer 275, with its 100% duty cycle output, handles those long welds without a problem."
The gas engine drives have proven cost effective. In addition to their lower purchase price, they are significantly lighter than diesel engine drives. This enables Proctor to run 1-ton trucks instead of 1 1/2-ton units. His new Dodge 3500 chassis with 9.5-ft. flatbed cost him about $15,000 less than his older, heavier vehicle.
The lower gross vehicle weight enables Proctor to spec the trucks with a quad cab option. "Since we're on the road all the time, the large cab comes in handy for carrying extra gear," he says. "The 1-ton trucks ride a little smoother, too, which is nice for our guys."
Less weight also makes it easier to meet weight restrictions. "Sometimes we'll run 200 to 300 lbs. of wire in a week," he says. "For one guy to pack that much wire, plus all our other tools, we would really push weight limits by adding a 1,500-lb. diesel welder to the truck. Fortunately, a 600-lb. gas engine drive gives us a huge weight advantage."
Flux cored vs. stick
DDJ Welding wins most of the bids it submits because it completes jobs faster - without sacrificing quality - by using equipment designed for flux cored arc welding in construction applications.
Historically, pipe welders and contractors welding in the field have preferred the stick welding process. But stick welding literally sends profits up in smoke.
"With an E6010 electrode, only about 60% of the electrode mass transforms into the actual weld metal," says John Powers, outside sales, Pacific Welding Supplies/TEC Welding Sales. "The rest of the electrode mass is lost through stubs, evaporates into the atmosphere as smoke or chips off as slag. If you purchase a 50-lb. canister of stick electrodes, you only lay down about 30 lbs. of actual filler metal. Conversely, an E71T8-K6 flux cored wire yields a deposition efficiency of nearly 80%. This means you purchase less filler metal per joint, which increases your bottom line."
Stick welding is also an inherently slow process. A 3/16-in. E6010 electrode deposits about 2.6 lbs. of filler metal per hour. However, a 5/64-in. E71T8-K6 wire, with a wire feed speed of 110 in. per minute and an arc voltage of 20.5, yields a deposition rate of 5.5 lbs. per hour - more than a 100% improvement. Greater deposition efficiency can mean big dollars, since DDJ Welding often gets paid by the joint.
A recent water pipe job for the city of Tacoma involved 48-in.-diameter, 3/16-in. wall pipe welded to AWS D1.1 standards. The bell-and-socket joint required a 1/4-in. fillet weld on the outside of the joint.
Proctor put in a quicker stringer bead (root) pass to heat the pipe and take out any impurities, then put in a structural pass over the top, consuming the first pass and any pinholes that might have occurred. "The pipe required 12.57 ft. of weld, which I completed in about an hour," he states. Completing the same joint with the stick process would have taken at least twice as long.
Proctor also prides himself in producing quality results. "My company's slogan is: 'Quality will never be compromised.' I tell my employees we do things right the first time," he asserts.
In 2006, the company won a subcontract in Anchorage to weld 80 joints of 42-in.-diameter pipe (3/4-in. wall thickness, V-groove, full penetration butt welds). Each joint on the high-tensile-strength pipe took 14 man-hours to complete.
"On the first day we arrived, we met with the engineering and project managers. Welding was at the top of their priority list," Proctor recalls. "A few months later, welding was no concern. We completed all 80 joints - and every weld was X-ray inspected - with just one slag inclusion at the surface of the weld. We ground that out, repaired the weld and it passed X-ray. Other construction workers on the job couldn't believe we could flux core weld so quickly and with such quality."
Benefits of portable feeders
The newest "voltage sensing" wire feeders can run gas-shielded and self-shielded solid and cored wires from .023- to 5/64-in. diameter. Because they have a much broader arc voltage range (14 to 48 VDC), they can run small and larger wires without arc outages or the "contactor chatter" common with older feeders.
Proctor first began using the Miller SuitCase X-TREME 12 VS feeder last year. "I ran those feeders on the Anchorage job paired with Miller XMT 350 inverters, and the welders just loved them," he states.
"On another 72-in. pipe job, where we wouldn't break arc for 20 minutes, the X-TREME's trigger lock function was great," he adds. "It stopped some of the hand fatigue related to keeping the trigger pulled. We could move around and change hand positions without stopping."
The digital display on the feeders increases accuracy. "Before digital readouts, we set voltage and wire feed speed by feel," Proctor says. "We would find a 'sweet spot' and put a scratch mark on the face plate. The digital readouts add more precision, and each machine runs the same. There's no more guesswork when setting welding parameters."
To withstand jobsite environments, portable feeders like the SuitCase X-TREME feature a case made from polypropylene, which shields internal components against sudden impacts and rough handling.
This has come in handy on DDJ Welding's projects. The contractor does much of its welding in trenches and inside pipe.
"We're always around water, mud and sand," Proctor says. "We try to tie the feeders off to make sure they don't fall, but dirty environments are just a fact of life. So far, the SuitCase feeder has been very durable. We even had them submerged when we left them in a pipe overnight and someone opened a valve. As long as you open the feeder up and let it dry for a couple of days, it will be all right."
Proctor admits that some older operators don't want to deal with a wire feeder on the jobsite or carry a feeder in their truck. "But the production of a wire feeder is so much better than stick welding, we feel its worth the effort," he states. "In fact, once you get used to carrying the SuitCase, it's not a big deal."
For added mobility in tight spaces, such as the inside of 36-in.-diameter pipe, DDJ Welding created small wagons that hold the feeder, a 350-amp inverter, work lights and more. "For working in trenches, we just lower the feeder in with a rope, so we don't have to worry about carrying it up and down a ladder," Proctor adds.
Enhanced ROI
With an overhead of $70 per hour per employee, Proctor needs his welders to be as productive as possible. That's why he opted to purchase the gas engine drives and wire feeders.
"You can rarely go wrong looking at new technology," says Proctor. "You have to keep your eyes open to new developments, and that's one of the advantages I get by working with Pacific Welding Supply/TEC Welding Sales. They have a diverse customer base and test a lot of different products. If a welder or feeder can pass the test of working in their rental fleet, then I know it's a good product."
"Our job is to stay on top of industry developments, understand contractors' needs and keep them competitive in the marketplace," says Bob Hankel, director of outside sales, Pacific Welding Supplies/Tec Welding Sales. "One such development is the newest generation of gasoline engine-driven welding generators. By introducing DDJ Welding to these products, we helped lower welder acquisition costs by more than $8,000 per welder."
Proctor sees the investment in the new technology as well worth it. "Better equipment results in better quality," he states, "and that's how I justify my return on investment."
Contributed by Don Knight, district manager, Miller Electric Mfg. Co..