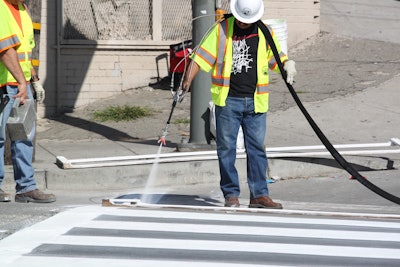
As public agencies look to maintain safety and reduce traffic disruption they look to longer-lasting pavement markings, bringing new materials into bid specifications. And as materials become more commonly specified by states and cities, they inevitably come to the attention of property managers who want, much like municipalities, less disruption on their property and longer-lasting markings.
The result has been increased attention to plural component materials and the need for contractors to include these materials in the services they offer.
Bill Howseman , president, Dispensing Technology Corp., says that unlike thermoplastic material, which is a single-component material that is melted to be applied, plural component materials are just what the name implies: thermosetting, two components are joined together to create a finished product. That product, according to Kurt Gruenberg, vice president, sales and new product development for RAE Products, is typically more durable than paint, maintains its reflectivity longer – and is more expensive.
Epoxy
The plural component material with which most contractors are familiar is epoxy. Epoxy is durable and very thin, making it less susceptible to plow damage. For that reason it’s more common in northern United States. Epoxy is effective on both asphalt and on concrete and is often used instead of thermoplastic on concrete.
There are two kinds of epoxy: Fast cure and slow cure. Fast cure is less expensive and it’s what most people use because it meets specifications and because it cures fast and can be opened up to traffic sooner. Slow cure adheres better to the pavement and is more durable but it takes a while to set up. In many cases either type will meet job specifications. The gel time for epoxy is slow to medium (see chart), meaning the material has a long enough pot life that it won’t set up in the gun. That enables contractors to use a static gun rather than an impingement gun to apply it.
Epoxy is applied in a 2:1 ratio, meaning two parts of epoxy resin to one part curing agent. Multiple pumps on the equipment are set to deliver the correct amount of material to the machine’s gun.
“You have to have the correct ratio as formulated by the manufacturer of the material or you’ll end up with properties that don’t meet the expectations of the formulation,” Howseman says. “But meeting the ratios is pretty foolproof with the equipment on the market and the positive displacement pumps.”
Howseman says that almost all epoxies require heating of the material so the viscosity of each component matches so they can properly mix. Material manufacturers recommend heating material to between 110° F and 140° F. Sometimes the container is heated and sometimes the material is heated as it recirculates in a loop through a glycol heater. The hoses to the spray gun are usually heated also.
Methyl Methacrylate (MMA) and MMA-B
Used widely throughout the world but only starting to gain traction in the United States is Methyl Methacrylate (MMA). Unlike epoxy, which relies on a curing agent, MMA requirs a catalyst to make the marking material cure. (A curing agent takes part in the reaction where a catalyst only initiates the curing.)
MMA is often referred to by its ratio (98:2) but unlike epoxy which refers to its ratio in PBV (parts by volume) MMA 98:2 refers to its ratio in PBW(parts by weight. So in this case the material is 98% resin and 2% catalyst by weight. Where MMA 1:1 and MMA 4:1 is stated in parts by volume. The MMA 1:1 is prepared for spraying by mixing in 4% BPO powder PBW .
The catalyst used in both MMA is benzoil peroxide oxidizer (BPO) and Gruenberg says the 98:2 is safer to use?? because BPO is a liquid. He says the 1:1 MMA is a three-component kit that includes part A, part B and powder BPO. Part B and the BPO are mixed to “promote” part B, and once that’s done it essentially becomes a 1:1 material PBV.
The amount of catalyst added determines how fast the material cures. A small amount of catalyst means the material can be worked for a while, a lot of catalyst means it only can be worked with briefly before it sets up. Contractors can vary the amount of catalyst (liquid or powder) to vary the cure time (to slow it down in hot weather or speed it up in cold weather, for example).
Once the MMA 1:1 is mixed it must be used within 72 hours(depending on how much catalyst is used) or thrown away because it begins to set up. Gruenberg says one of the advantages of MMA 98:2 is that there’s little-to-no waste because the 98% and 2% is mixed at in the tip at the gun. “With 1:1 you’re mixing and promoting Part B and once it’s mixed whatever you have left at the end of the job you’ve got to throw it away,” Gruenberg says. “That’s not the case with 98:2.”
Gruenberg says that while both materials are effective, MMA 1:1 is a little easier to use and is more forgiving. “You can be slightly off on the ratio and it’s still going to perform as intended,” he says. “The 98:2 is less forgiving. If you’re off by 4% or more it won’t provide the properties expected and it also will cure very slowly.”
Gruenberg says MMA 98:2 and MMA 1:1 are both good entry materials into the world of plural component materials for paint striping contractors because contractors can vary the amount of catalyst they need based on the temperature and hand mix it on smaller jobs and then put the material in a cart – for small crosswalks or similar projects. It’s also a reasonable alternative for contractors who want to be able to apply durable coatings but who can’t afford a truck. Howseman says that the equipment cost for 1:1 is less expensive than 98:2 so a contractor can be in the plural coatings pavement marking business for less than $20,000 for an entry level machine.
Gruenberg says that among the plural component options 1:1 MMA is the easiest for contractors to start with because the machine is the easiest to use and is the closest to a typical striping machine. “Basically it’s a spray machine on steroids. There are two pumps and you clean the gun out with acetone,” he says.
Gruenberg says one of the advantages of MMA is recoatability. “Of all marking products MMA has the ability to fuse to itself, so regardless of how many coats you put on top of it, it won’t delaminate and it won’t chip.” He says MMA also doesn’t break down as a result of UV rays.
Another advantage is MMA extends the marking season because can put it down at freezing temperatures. “As long as you don’t have ice or water crystals on the pavement you will have superior adhesion,” Gruenberg says. “It will take longer to cure but it will cure at 32 F because MMA generates its own heat through a chemical reaction.”
Modified Urethane
Not only is polyurethane – a modified urethane -- a member of the epoxy family, it is often used interchangeably with epoxy assuming the specs have been accepted by an agency.
Gruenberg says contractors are likely to see is more in future specifications because it stays white and offers a compromise between the slow and fast cure epoxy options.
Howseman says polyurethane’s 2:1 ratio is similar to that of epoxy, so contractors can put it down with the same equipment, and can use either a static or impingement gun. Both epoxy and polyurethane require a curing agent, both need to be heated, and they offer similar properties.
Polyurea
Polyurea marking materials have the same 2:1 mix ratio so can be put down using the same equipment as epoxy after it has been rigorously cleaned. Polyurea cures quickly, in minutes or even seconds, so a static mixer can’t be used and impingement mixing must be used. Because it cures so quickly it’s an ideal material for long line striping with a moving lane closure.
“That way you don’t have to close lanes,” Howseman says. “The speed at which it cures is a big advantage for highway work, so it’s a great choice for long-line marking.”
Some cities also specify polyurea for intersections and even legends, but in both cases because contractors generally block intersections when working on them the speed curing factor is not as important.
Contractors are encountering more requests for plural components but it’s important to realize that at least for government work the material must be approved for use before it can be included in a bid spec. So contractors interested in adding plural component markings to their services should first monitor bid specs to determine which materials are being specified.
But producers of plural component materials and manufacturers of plural component application equipment do expect the market to grow on the public agency side and on the private side. “We see it growing, absolutely, especially with warranty work,” Howseman says. “As property owners and public agencies expect contractors to guarantee a minimum conspicuity for five years plural component materials will become more used because they maintain reflectivity and effectiveness longer than paint. The contractor can warranty the work without having to go back and keep restriping.”
Rob Buerer, executive vice president of Marking Specialists, South Elgin, IL also provided information for this article.
[possible captions]
When comparing materials plural components should be compared with thermoplastic, not paint. Paint is not as durable as plural components and the cost of plural components is similar to thermoplastic.
Epoxy materials must be heated to between 110° F and 140° F so the viscosity of each component matches so they mix better and mix more easily.
[chart caption]
There are three basic groupings of plural component materials, each designed for a specific use. Marking lines (stripes, legends, or wide-area markings such as bus stops or even bike paths), Adhesives (typically applies to epoxy where the components are mixed to essentially produce a glue,) High-friction surfacing (Used increasingly on roads to improve skid resistance on places where accidents are frequent such as curves, hills and off-ramps. Generally used to coat an entire lane or as a broad surface coating rather than as a pavement marking).