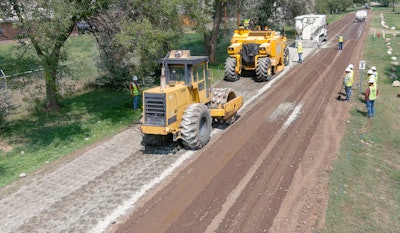
We all know that our roads will only be as strong as the bases they are built on; "Roads may wear from the top, but they fail from the bottom."
While we invest plenty of time and resources creating more resilient asphalt mixtures to help prevent wear from the top, we haven't focused too much on creating a stronger foundation for our roadways.
If left untreated, cracks in asphalt lead to deterioration of the base structure beneath our roadways.
Lithified Technologies developed a soil technology known as LithTec™ that mimics lithification, a natural process that transforms soil into stone over thousands of years. The technology developed uses the same naturally occurring minerals and chemicals, along with accelerators, to make lithification occur in 24-48 hours. This "accelerated lithification" provides optimal strength for road infrastructure, enabling thoroughfares and highways to last much longer.
"LithTec is all about building from the bottom up," Bob Sherwin, CEO at Lithified Technologies says. "LithTec turns the road base or subgrade into a rock-hard and water resistant road foundation that remains bound and non-dispersive while under water. You would witness this with the two soil samples (one treated with LithTec and one untreated) submerged under water at the same time. The untreated proctor immediately will start disintegrating turning the water muddy and the cylinder will lose approximately half of its original size in a very short time. The LithTec treated sample will remain rock-hard and non-dispersive as no material will fall off and the water will remain clear."
Keeping water out of the road base is a key objective and this technology aims to help with that.
Full Depth Lithification
We have all heard of Full-Depth Reclamation (FDR), which is the process of pulverizing all layers of existing asphalt pavements in place to depths of up to 20 inches. FDR has grown in popularity as equipment has evolved and recycling efforts have heightened. While the process is efficient in creating a structurally sound roadway at a fraction of the cost of remove and replace, it does not strengthen the existing road bed.
Added stability can be achieved if the reclaimed base layer is chemically or mechanically stabilized. Chemical stabilization introduces cement, lime, kiln dust, or emulsified asphalt to improve binding of the materials.
As states and municipalities are continually trying to make their road investments last longer, Lithified Technologies has taken this process one step further using science to actually strengthen the roadbed for good.
LithTec produces both high strength and high ductility simultaneously. These qualities are all achieved through the “Accelerated Lithification” process, which decreases the porosity, increases the binding potential, is resistant to abrasion and ultimately turns soil into stone through a process they call Full Depth Lithification (FDL). This process can save 30-50% over traditional FDR projects.
"Accelerated Lithification Technology is not considered to be a “soil stabilizer” at all, as the word itself implies that the product is trying to 'stabilize the soil.'” Sherwin says. "LithTec technology is not gluing the dirt together like a polymer or making it sticky like a lignin, molasses or tree sap which is simply a compaction aid, that washes out under rain and snow conditions. Instead, the LithTec process transforms the soil or road base material at the molecular level, turning it into a rock-hard water resistant base with unprecedented load bearing capacity. This is the first product to achieve double the strength of cement and 3-4 times the ductility. The company spent over $15M and nine years in development to be able to prove this."
Sherwin's company developed the dry blend of naturally occurring minerals that they now call LithTec. These materials firm up within a day after being mixed with and compacted into traditional road base materials at optimum moisture content. The company refers to its LithTec product as 'Nature's Concrete."
"LithTec transforms traditional untreated base course that averages 25,000 PSI Modulus into a "high-performance" road base that has 500,000 PSI Modulus," Sherwin says. "By increasing the road’s load bearing capacity by over 2,000%, road designers and engineers can transfer the “structural credits” (the strength and load bearing capacity) normally found in the asphalt surface, into the LithTec treated base."
As a result, the asphalt thickness may be reduced by as much as 67%.
"Counties across the country have discovered that a LithTec treated road base with a chip seal surface will provide an asphalt performance road for approximately 25 cents on the dollar, compared to a traditional asphalt road," Sherwin says. "When you put the chip seal over the top of LithTec, it's the equivalent of putting it on top of asphalt, but in a much stronger and more economical way."
Custom Formula Provides Lasting Results
Due to the high volume of materials in road construction, Lithified Technologies knows that optimization is the key to the success of each project.
To maximize the high performance potential of your roads, Lithified Technologies provides a "Value Engineer" package that includes customization of the LithTec product to meet the specific project needs. A trained "GeoTechnical" field operator is sent to each project to sample the project and determine variations so that the product can be customized based on the specific variables present in the road base. Testing in the lab and again in the field is performed to ensure optimal results will be achieved.
"From the very beginning of the process, our engineers will go out and pull soil samples from the project," Sherwin says. "They will do GPS mapping of where the samples came from and bring them back to the lab where our technicians will perform a battery of 10 different tests on those samples. This is all a part of the customization process to determine which formula we need to get the optimal performance out of that material."
When it's time for installation of the product, each custom formula is blended on-demand for each specific project. The blend the materials at one of their 19 locations across the country and ship it out the day before or the day of the project. The GeoTechs will again be on-site to perform quality control as well.
"The field testing will make sure the material is hitting the same numbers in the field as we achieved in the lab," Sherwin says. "They make sure you're hitting your optimum moisture content, ensuring the proper depth is being met, the proper dosage is going down and compaction is being met. This is all included with the purchase of the LithTec product."
The LithTec product is applied on-site after a reclaimer/stabilizer comes in to grind up the failing roadway. The LithTec powder is laid down per the custom formula. The reclaimer then goes back through the material ensuring the material is at the pre-determined optimum moisture content. Compaction then occurs with a sheepsfoot roller, a grader then shapes the road and a flat wheel roller finishes out the compaction before the surface is put down.
Perpetual Roadways & Infrastructure Preservation
When you look at the challenges of the road building industry today, we are facing much higher amounts of traffic in much heavier loads as the shipping of goods has never been higher. These increased loads are taking their toll on our roads and highways and the industry must figure out how to build roadways that sustain these volumes.
"We have 15 million 40-ton trucks on our highways and that number is growing by the day," Sherwin says. "DOT studies have said that each 40-ton truck has as much wear and tear on an asphalt highway as 10,000 automobiles."
Building stronger foundations can be a key to longer-lasting roadways.