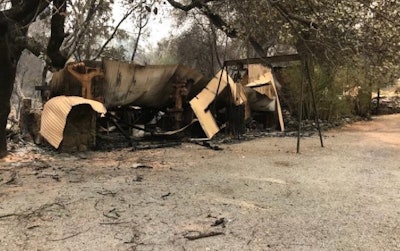
The intense forest fire that jumped the Sacramento River near Redding, CA, in November destroyed Iron Mountain Manufacturing, which produces Geotextile Apparatus Co. (GAC) products, according to Mounque Barazone, owner of GAC.
Products manufactured by GAC include the multi-patented Grizzly Cub 300T, Grizzly 600T and 600TH Oil Truck fabric installation machines, patent-pending models RP3XL and RP4XL roll pullers, and patent-pending High Melt brush/broom.
But Barazone, who developed his first fabric installation machine in 1980 and acquired numerous patents for it through the mid-1980s, said that despite the fire the company was able to produce and ship it's roll pullers within weeks of the fire because parts could be produced and assembled elsewhere. Manufacture of the fabric installation machines will be more problematic because the factory was destroyed and Iron Mountain Manufacturing will not be allowed to rebuild on the same site.
He said Iron Mountain was permitted to manufacture at its forested location because it was grandfathered in by a state law. But since the fire destroyed the entire facility the state will not allow them to rebuild to manufacturer there. So Barazone says GAC is researching other locations for manufacturing.
Carl and Sue Taylor, owners of the Iron Mountain Manufacturing, lived on the property and escaped the fire. Barazone, an experienced sailor who was support staff in the America’s Cup, met Carl Taylor, a blacksmith in the mid-1980s when the two were working on their boats in a nearby lake. They struck up friendship that became a business relationship where GAC would invest in Iron Mountain Manufacturing so it could add the necessary equipment and the company would produce product under contract with GAC.
“Carl’s disabled and they gave them 30 minutes to evacuate,” Barazone said. “He immediately left his house and went to the facility to collect all his notes he’s made over the years about making the GAC products. I have the drawings but there are things he’s learned over the years and he wanted to make sure he had those for when we start up again.
“Every year I use every dime I have to get the shop going and buy steel and inventory, brushes and all. It was our busiest time and we were three days away from completing a machine and had just built roll pullers to replace the year’s sales. I had just borrowed $10,000 to put those in stock and build an extra inventory machine. We had one machine just about ready to ship and orders for three more we were working on – but those will be delayed until we can get the manufacturing up and running."
Barazone said the manufacturing equipment was decades old and used old-school technology and because of that it was virtually uninsurable. “My equipment, all my tooling and fixtures were old and all written off years ago and not insurable. The insurance cost exceeded my inventory cost,” Barazone said. “Insurance companies don’t want to insure equipment like that because it can’t really be replaced. You have to replace it with more modern digital equipment that costs way more than the old equipment.”
But he said GAC is getting tremendous support from both Federal Emergency Management Association (FEMA) and the Small Business Administration (SBA) in its effort to get its manufacturing going.
He says part of the difficulty GAC will have restarting its manufacturing operation is the machines require many fixtures and tooling. There are over 300 parts with angles, holes and slots and assembly cannot be done with the fixtures and tooling.
Barazone said that because Iron Mountain Machinery will need completely new manufacturing to build the fabric installation machines, he will eliminate the Cub 300T and Grizzly 600T and produce and introduce a new, upgraded installation machine, the Grizzly 900, that takes advantage of new technologies. Machines take between two and four weeks to manufacture depending options selected and Barazone says he expects the first Grizzly 900 to be shipped this spring.
Barazone said the fire and manufacturing delays will not alter his plans to speak at National Pavement Expo, Feb. 27-March 2 in Nashville, where he will be discussing “Best Practices” for Installing Paving Synthetics.”