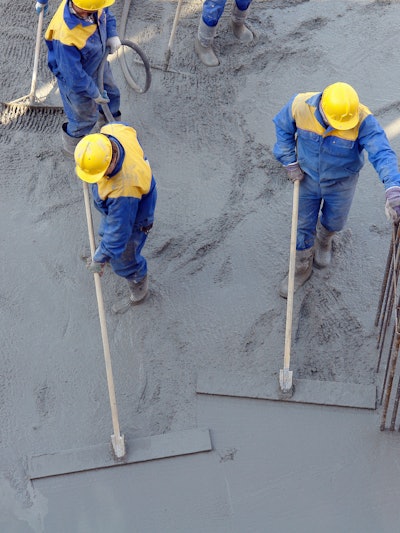
Over-processing is applying more resources than are required, needed or requested. Examples include using copper instead of PVC, getting additional signatures on requisitions, duplicating data on forms, having more than one individual working on a process or task, having more people than necessary handling time sheets, etc.
Over-processing can be seen in several ways. Consider a few of the following examples:
- Crews reworking performed work that already meets needed specification but not the perfectionist attitude of the foreman
- Contractor, estimator and crew foreman all make their “minor changes” on a job drawing
- Substituting a different and more expensive material, process or component to construction…but not getting paid for the additional value
- Putting too many workers on project without an effective plan to keep all workers clearly productive
Over-processing can be difficult to identify at times, but if you have ever observed a crew of five or six labors watching one guy do all the work, you’re getting close to an over-processing situation. Cutting to the chase…over-processing is just putting on more resources than are needed — and most often that leaves the contractor “taking it in the shorts.”
OK, then how can a contractor prevent the casualties of over-processing? Let’s look at a few techniques that can help you prevent over-processing casualties.
1. Have a clear schedule & work plan
Sorry, it’s just not “rocket science.” Throwing more workers at a project just to feel good about having it staffed “adequately” might be the most expensive idea you have. This way of thinking is also a leading waste creator — especially if there is no clear schedule that lines out each of the workers and what each will be doing.
2. Establish clear quality standards & stick by them
I’ll grant you that most construction foremen probably fall in the category of “let’s just get ‘er done so we can move on.” However, it is critical that the contractor obtain the needed specifications for the project or that the contractor establish the standards if none are available. Then the contractor must hold the crews — including the foremen — accountable to produce work to the level of quality spelled out.
3. Establish the “Final Critic” and move on
The “Final Critic” is the final decision maker on prints, estimates, process, etc. In the smaller construction company this person is most likely the owner. However, in larger construction firms, where there might be project managers, division managers, even vice presidents there needs to be a chain of command that clearly lines out authority in who makes the final decisions when there is confusion or uncertainty.
4. Remember to get signed change orders for any changes
In the contractor’s desire to satisfy his customer, agreeing to do an extra “here or there” becomes giving away profitable labor and creativity. While any change and deviation from the agreed-to contract, estimate or drawing should be paid for, the reality of the situation is that this doesn’t always happen.
Obtaining a document spelling out the needed or desired change, including the signature of the client or her representative, is both good business and legally wise. Many contractors get “stuck with the check” after performing changed work the client has requested. Remember, customers can have “selective memory” as to what was and wasn’t discussed when it comes time to pay the bill. Be careful.
So take to heart the potential pitfalls of over-processing within your operation, then begin to apply these four practices. You’ll see an impact in productivity, job clarity and bottom-line performance.
And remember: Lean Construction is about reducing the costs of wastes such as over-processing and empowering the contractor to perform better, faster, and with more profit!
Stay Lean Contractors!