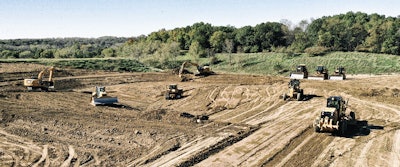
What’s your guess as to how much the building and construction industry contributes to global carbon emissions? 5%? 10%? 20%? According to the 2019 Global Status Report for Buildings and Construction, it’s 39%. That’s a huge number. Granted, most of these CO2 emissions (28%) come from keeping buildings operational once they’re constructed. But that leaves 11% attributed directly to the construction process itself.
The key to reducing machine emissions is burning less fossil fuel. You can do that in multiple ways: Choosing equipment that operates on renewable fuels, electric power or technologies like electric drive. Leveraging onboard technology that helps reduce fuel consumption. Training operators to work more efficiently.
Reducing Idle Time
But one of the simplest ways to burn less is to idle less. Idle time increases emissions because you’re consuming fuel even when you’re not working. It also racks up unproductive hours on equipment, which means you could be changing your fluids and filters less if you reduce idle time.
Follow these five simple steps to reduce idle time, and you can shrink your carbon emissions, generate less waste and cut your operating costs all at the same time.
1. Limit warm-up and cool-down time. According to the U.S Environmental Protection Agency, three to five minutes is all that’s needed at the start of a shift. And two minutes is plenty for most machines to reach optimum shutdown temperatures at shift’s end. Newer equipment, with automatic shutdown features can help operators control this process.
2. Shut off equipment during lunch and breaks. Some operators like to keep machines running to maintain an ideal cab temperature, but that can be a big fuel waster. If keeping the cab warm or cool is essential in your location, consider investing in systems like engine-off cab heaters and coolers instead.
3. Follow the five-minute rule. If your machine is going to idle for more than five minutes, it’s best to shut it down. At that point, restarting equipment actually uses less fuel than idling. This rule applies to trucks waiting to load or unload, too.
4. Take advantage of idle management systems. Newer construction equipment often feature auto-idle or engine idle management systems. This technology monitors equipment parameters and automatically reduces engine rpm to idle rpm or below.
5. Turn to telematics to monitor idle time. You can use the data to compare working time versus idle time by location, shift, machine, even operator. Then, you’ll have the knowledge to make changes or implement training. Remember to share this data with your team so they can understand the effects of idling on equipment and the correlation with overall operation, environmental stewardship and company profits.
Reducing idle time is one of the easiest steps you can take on your journey toward more sustainable operation—and it’s one that can have a significant effect on both your bottom line and your carbon footprint. Check out some other ways you can improve fuel efficiency.