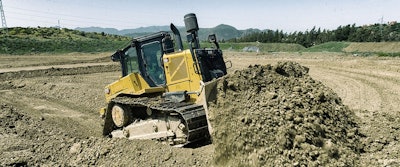
We used to feel confident saying that fuel expenses accounted for 30%-50% of a machine’s operating costs. Given the recent spike in prices, that number may be even higher now. Either way, it’s a lot — and anything you can do to lower that percentage goes straight to your bottom line.
Five factors play a role in fuel efficiency: idle time, operator technique, job-site set-up, equipment selection and configuration, and technology. Let’s take a closer look at that last item. When you’re shopping for equipment, what fuel-saving technologies should be on your priority list?
1. Advanced Engines
Look for equipment engines capable of delivering full power at lower rpms, which reduces both fuel consumption and emissions. Power density is important, too, allowing higher performance in a lighter-weight package. The option to run the engine in economy mode when the job allows is another fuel-saver. It reduces maximum engine speed and can cut fuel usage by as much as 6%. Also keep an eye out for automatic engine idle shutdown, which stops the engine after a predetermined period of idle time.
2. Innovative Features
Consider machines equipped with electric drive, hydrostatic or continuously variable transmissions. They can deliver double-digit reductions in fuel consumption with productivity equal to or greater than standard models of the same size or class. Load-sensing hydraulics also improve fuel efficiency by automatically directing the right amount of flow to the implements based on operating conditions. Even features like electro-hydraulic joystick controls can contribute to fuel savings by helping operators of any experience level work more quickly and efficiently.
3. Onboard Systems
Your choices here are practically endless: 2D and 3D grading, on-the-go payload weighing, productivity measurement, lift and slope assist, even remote-control and semi-autonomous operation. Talk to your equipment dealer about which onboard systems make the most sense for your operation. The good news is that they can all deliver significant fuel efficiency improvements — primarily by helping your operators dig, load and grade with more confidence, speed and accuracy.
4. Telematics
Most every machine today comes with a telematics system. The key is choosing one you’ll actually use. That means a simple interface, the ability to customize the information you want to see and access to reports that make understanding — and acting on — data easy. With the right telematics system, you can track everything from working time versus idle time to fuel consumption by machine, operator or job site. Then you can identify issues affecting fuel efficiency and make changes to improve it.
No single technology is the magic bullet to shrink your fuel bills. But the right mix of solutions above — combined with a focus on idle time reduction, good operator technique, smart equipment selection and proper job-site set-up — will have you filling up the tank less often and getting more work done along the way.