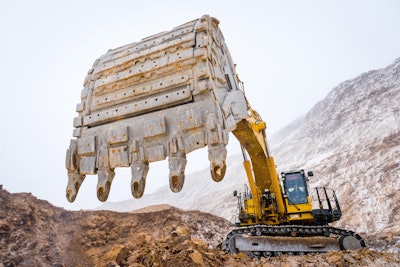
The projections are in and they look solid: Construction equipment rental revenue in the U.S. will grow by 12.5 percent this year and is expected to grow by 7 percent in 2023, according to the American Rental Association’s recent forecast. The bottom line to this new bottom line? You’d better be planning for a bump in demand for your heavy equipment rental solutions, along with customer expectations for high availability and maximum uptime.
With increased time utilization of fleet equipment, rental center GMs and garage and service shop managers will see more wear and tear on their machines. Preventive maintenance can stem unplanned servicing and significant repair work. In such a demanding time with ongoing staffing challenges, it’s more important than ever to keep your equipment up and running and your shop set up for maximum efficiency. Here are some tips that will help:
1. Right Tool, Right Time
Jobsites can be exposed, brutal environments, so when equipment comes off rental, it needs to be thoroughly and efficiently inspected, maintained and repaired, and on deck for the next customer. Searching for disorganized small parts or chasing down a part online or across town is an expensive waste of time. Can you afford to have an excavator that rents for $800 per day out of service because your shop ran out of something? That missed rental opportunity may cost you a long-term customer.
Work more productively with orderly, clearly labeled storage systems that meet your center’s unique needs. A modular system with the products you use most can grow with your shop. Prepackaged equipment maintenance assortments with minimum quantities provide broad parts coverage with minimal expense.
2. Labor Lift: Hands-on Help
The ongoing labor shortage continues to be a top concern across the industry. Look to your vendor partners for on-the-ground assistance. A best practice for service-intensive vendor managed inventory (VMI) programs puts reps on-site in a customer’s facility every 10 days, ordering and stocking product, so your team can focus on service. They have a fundamental understanding of the shop’s business, inventory usage patterns and maintenance and repair challenges. This helps solve for supply chain and labor shortage issues and lowers the total cost of operation.
Regularly inspect hydraulic hoses and assemblies for abrasion, leakage, cracking or blackening, rust buildup, kinks and tube erosion.©ilyaplatonov – stock.adobe.com
3. Turnkey Solutions
That excavator I referenced earlier, along with dozers, backhoes, cranes and a long list of pieces in your inventory, relies on hydraulic systems. Regularly inspect hydraulic hoses and assemblies for abrasion, leakage, cracking or blackening, rust buildup, kinks and tube erosion. Better to head off a problem now than risk a breakdown in the field. Replace hoses proactively to increase productivity and lengthen component life and ensure safety. Safety first, last, and always.
Want to really impact time and cost savings? Crimp in-house. And in the field. Take control of your hydraulic maintenance by making your own OEM-quality custom hose assemblies to reduce downtime and cut your hose costs by up to 50%. An industry expert can help you set up a crimping station, select product and match systems and train your staff to assemble hoses and fittings safely and confidently.
Two of the long list of casualties of recent supply chain disruptions are aerosol cans and plastic nozzles – both increasingly hard to source. A refillable aerosol system that runs off standard shop air systems and works with 5-gallon pails or 55-gallon drums is an economical alternative to aerosol products such as brake and parts cleaners. Charge reusable aerosol containers with product and compressed air in seconds and cut costs up to 30% compared to the standard price of aerosol cans.
4. Ask Questions, Share Ideas
We all learn by trading experiences. Did you know you can loosen worn bolts with rounded heads using a pipe wrench? Or that a soldering iron can heat a stuck screw held fast by a threadlocker? I drive big storage hooks with a wrench to protect the plastic coating and my hands. I didn’t until I saw someone else do it – a minor “aha” moment.
My point is that nobody’s born knowing. There may be a more effective product application, a new use for a tool you’ve long used for something else, or even a tool you didn’t know existed that can make a faster, cleaner repair. You won’t know unless you ask.
Again, look to supply partners. On-site reps are experienced and knowledgeable. Invest a little time so they can demo how a product works, how best to use it and show you tools to make a repair better, safer and less expensive overall. This is also the time to hear recommendations and application advice on high-performance, maintenance engineered products that meet your shop’s standards and application specifications.
Expect the Unexpected
You couldn’t have predicted or prevented the impacts of COVID-19 and supply chain delays on your business. Check in with your vendors on plans that streamline supplies and processes so your operation can address seasonal demand for snow removal, professional turf/golf equipment and lawn and landscape equipment, and the growing heavy equipment needs of your construction, industrial and government customers. You won’t have to worry about where maintenance and repair products are up and down the supply chain – they’ll always be at hand.