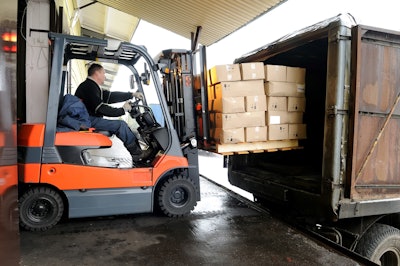
It's been predicted that renewables may produce more than half the world’s electricity by 2035. And while it may seem futuristic, the electrification of everything is happening now, and, at a breakneck pace. Whether it’s transportation, building, industrial conversions or other innovations, everything seems to be going electric.
The shift is due to more regulations on greenhouse gas or carbon emissions, which also happen to be increasingly stringent. It’s the hope that reduced electricity costs will provide incentives to avoid the headaches of dealing with evolving laws that tend to creep up on business as usual.
We’re aware that our industry—construction—is responsible for 39 percent of carbon emissions globally. And a recent U.S. Green Building Council study showed that construction also accounted for roughly 40 percent of our annual energy usage. It’s no wonder that the Environmental Protection Agency (EPA) has been enacting stricter emissions standards for nonroad diesel engines, like so many of those used on American construction sites.
This means the electrification of construction sites, and the equipment used on them, is right on the horizon. Take Oslo, Norway, as an example, where all new public buildings must use “fossil-free-fueled” construction machinery. Oslo boasts of the first zero-emission, all-electric jobsite. By using electric construction machines, it was estimated that the Olav Vs Gate Pilot Project saved 35 thousand liters of diesel and avoided the offset of 92,500 kilograms of CO2. According to their estimates, that’s equal to taking 20 cars off the road for a year.
Norway may be a pioneer with its new laws that ban polluters, like diesel construction machines, but cities like Barcelona, London and Beijing have already passed laws of the same vein. At the Gammon Construction site in Hong Kong, a battery-powered crane has begun erecting the Advanced Manufacturing Center, which will be one of the company’s first all-electric projects. It’s plain to see this isn’t a trend, but instead, is a new way of doing business.
The construction industry is dutifully responding with all-electric equipment. Volvo has a host of machines almost to market, such as compact wheel loaders and excavators that boast of zero emissions, lower noise levels and reduced energy costs. In January of this year, Bobcat Co. launched its new, all-electric Bobcat T7X compact track loader. It completely eliminates all hydraulic systems, meaning there are no petroleum products being used.) Heavy equipment companies also are spending on R&D to electrify their offerings.
These strides are excellent for large equipment companies to make but, for construction site operators, there is reason to pause. Whether to leap now, to what could be considered early-adapter status, requires a lot of understanding about the pros and cons for an electric conversion.
Energy efficiency and fewer emissions may be the most obvious benefit of going electric. Since electric motors don’t rely on burning fuels the way internal combustion engines do, there’s much less pollution caused. An added bonus is that cleaner electric construction equipment could save construction companies money by entitling them to emission-reducing tax incentives.
Less noise equals happier neighbors. It’s no secret that construction sites produce a lot of noise. It’s the No. 1 complaint of neighbors, over dust and traffic. With quieter, electric machines, construction sites can have longer workdays, and, in some places, they can possibly run at night. It’s also considered safer to run a quieter site because verbal communication is less subdued. What’s more, quieter engines avoid potential hearing damage to workers caused by prolonged exposure to loud machinery.
Lower maintenance costs help. Internal combustion engines have many more moving parts than electric motors, which means there are fewer ways that things can go wrong. Indeed, electric construction equipment breaks down less frequently and requires fewer checkups. Construction companies who rent, lease or buy electric will end up spending less on maintenance and will face reduced equipment downtime.
On the other hand, there are drawbacks to converting right away to all-electric equipment. One con is insufficient infrastructure. Currently about 60 percent of electric power in the United States is provided by coal and natural gas plants. Since these are fossil fuels, their use negates the decreased pollution benefit that goes along with adopting electric construction equipment, and any tax credits could be null. Furthermore, in some cases, it might require a large initial investment to provide a site with enough power for it to run a full array of all-electric equipment, especially if it is in a rural area. Transportable diesel fuel help avoids this problem.
Long recharge times are also a red flag. While there’s much R&D surrounding better batteries, the ones used in heavy equipment today take a long time to recharge. Backups and comprehending the different requirements of each machine cause work delays and too much down time, not to mention the costs of replacement batteries.
Higher costs are the reality for now. Electric construction equipment is still within the new product category and is therefore more expensive to purchase than standard equipment counterparts. Additionally, repair costs are higher and mechanics scarcer and newer.
As we progress, we’ll see more commitment in funds from the likes of the U.S. Department of Energy, which recently announced $45 million in funding to support the domestic development of advanced batteries. Electrifying the transportation sector in America is a priority for the Biden administration, whose goal is to have electric vehicles constitute half of American car sales by 2030.
Alas, we’re not in the 2030s yet, and we’re still waiting for all that renewably powered electric infrastructure to plug into. Balancing future mandates and doing the cost-benefit analysis make it a company’s individual choice on how to fuel a construction site. A mix of traditional and electric may be a solution for now, and there are certainly many hybrid models on the market to try out. Renting or leasing a machine is a great option for slowly sliding into the electric future.