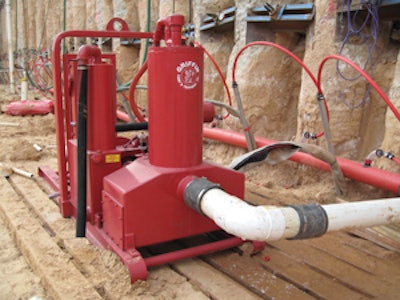
Selecting the best dewatering solution requires experience and an understanding of the physics involved. For optimum performance and equipment life, it's important to choose the correct type and size of pump, as well as set it up for the application.
Sizing pumps should be a science, not guesswork. "Trial and error is not suggested, but it is not an uncommon method in contracting pump rentals," says Mark Trumble, business development manager for RSC in LaPorte, TX.
Many parameters influence an effective pumping system. According to Dale Conway, vice president of engineering, Thompson Pump & Mfg., you need to understand the required flow, pressure, solids size, suction lift, altitude, specific gravity, viscosity, temperature and fluid type.
"If the product is water, then use suction lift and discharge elevations as a bare minimum estimate," advises Trumble. Then account for any losses in the system. "The TDH (Total Dynamic Head) is then created by adding friction losses from the distance pumped, as well as all valves, fittings and equipment downstream which have resistance to the suction and discharge."
"The longer the discharge run of the hose, the more the friction loss. The more friction loss you have, the less flow," explains Jim Widrick, construction equipment sales manager, Gorman Rupp. "So you really want to minimize how much friction loss you have through the hose." Keep in mind that all pumps are limited to a maximum suction lift of about 28 ft.
Solids content can actually dictate pump type. "Centrifugal pumps have limitations of the size and make-up (hardness) of solids," says Trumble. "Diaphragm, vane, gear, lobe, progressive cavity and submersible [pumps] all have applications that are best suited to their design and the work to be performed."
Widrick adds, "Centrifugal pumps are effective up to a maximum of 4% to 5% solids at best. If you go much higher than that, you usually have to go to a positive-displacement pump, such as a diaphragm pump."
As such, it's important to consult the manufacturer's specifications for solids-handling diameter.
Dwight Evans, engineer, Godwin Pumps, recommends using a suction screen that is slightly smaller than the solids-handling diameter to protect the pump from large debris. "Also consider the materials used in the wear parts," he says. "The higher the concentration and diameter of a solid, and the greater its hardness, the greater the potential for failure of the wear parts (impeller, wear plates, seals, volute, etc.)."
Value of wet prime
Trash pumps come in several variations with different inlet sizes, solids-handling capability and efficiencies.
"Wet prime trash pumps are one of the easiest to use and maintain as they have fewer components than other pumps - basically a pump and a motor/engine," says Jerry Soto, Griffin Dewatering Corp. "Wet prime pumps require the pump cavity to be filled for the first time, then will 'self prime' as long as there is water above the eye of the impeller. To prevent the pump casing water from siphoning the water out when the pump is shut down, there is a check valve on the suction side."
Fewer moving parts can be a big advantage. "Depending upon how it is designed, that wet prime pump can last 20 or 30 years with regular maintenance," says Widrick. "The difference in the pump end is the wet prime pump has a large volute to hold a large volume of water."
Evans notes, "The benefits of a wet priming trash pump are portability, independence from a designated power source, ability to be placed right at the water's edge and relatively inexpensive purchase price and operating cost. Disadvantages include the need to manually prime, inability to control speed and limited fuel capacity that demands more frequent monitoring and refueling."
Wet prime pumps are a little more bulky, and priming is affected by internal pump wear, adds Conway. Dry prime pumps, on the other hand, are smaller in physical size, and priming is unaffected by internal wear. However, there are more moving parts to maintain.
Wet prime models have operational limitations, as well. "Wet priming trash pumps are best suited for applications with a relatively low sump," says Evans. "Specifically, applications with less than 200 ft. of discharge - not pumping more than 350 gpm - are the most common."
Yet, their impeller design makes them a good solution for jobs where solids are present. "They are successful in applications including trash-laden water found in construction applications, stream and pond dewatering and septic tanks and manholes," says Evans.
They work best where there is an abundance of liquid. "It would be preferred to have the pump running constantly in an application where there is plenty of water or liquid that is being pumped," Evans states, "or if the unit has an automatic float control for automatic on/off operation."
Soto adds, "The best conditions for wet priming pumps are open pit and sumping applications, where the suction lift is less than 25 ft. and where priming time is not as critical. Wet self-priming pumps normally take longer to prime, depending upon suction lift and length of suction hose/pipe.
"They also can be used for bypass pumping when there is sufficient retention time to allow for the pump to prime," he continues. "While the wet prime pump can handle some air intrusion on the suction side, if there is a significant intrusion of air, it will lose its prime and will need to re-prime itself. So for a good period of time, the pump is not pumping."
In addition, while wet prime pumps may range up to 12 in., this says little of their capacity. "For the most part, wet self-priming pumps are of a lesser capacity due to their design limitation than their cousins, the dry prime pump," says Soto.
When dry is best
Dry prime pumps prime without the need to add fluid. Prime is maintained via a priming device, which is normally either a vacuum unit, diaphragm or compressor.
Trumble explains, "The priming process is achieved by the use of an integral compressor, which creates a full vacuum through a venturi educator. This is suited for nearly all dewatering and transfer applications that require high and rapid static suction lift."
Rapid priming coupled with higher volumes results in greater efficiency over wet priming units. "A dry prime pump with vacuum assist can increase performance by 20% over a wet prime pump," Widrick estimates, "but the initial cost is probably 40% more."
According to Soto, a dry prime pump will nearly always outperform a wet prime pump due to its design. "Generally, dry prime pumps will incorporate non-clog impellers, which are often more efficient than the open trash impeller used in the wet prime," he notes. "The non-clog design allows for larger sizing, allowing the pumping capacity so you can get a much bigger dry prime."
Yet, Soto cautions that the term "non-clog" can be misleading. "The impeller will clog if a large enough solid is pulled into the pump, i.e., plastic bottles, towels, bricks, etc.," he points out.
Due to their ability to handle large volumes of air in the suction, dry prime models are often used in applications where they may experience dry running or see intermittent flow, such as sewer bypass or construction sites where the unit must constantly work to keep the area completely dry. "[Large air volumes] can occur from suction vortexing, turbulence or low fluid levels," says Trumble. "The prime-assist dry prime will pick up suction prime without any need of an operator filling the pump with fluid."
"Dry prime trash pumps can use automatic controls to start and stop pumping based on flow levels," adds Evans. "The obvious advantages include extended hours of service, increased capacity (volume), decreased dewatering time, higher lifts, independent operation, a broader range of liquids pumped, more durable wear parts and larger solids-handling capabilities."
A solution for thick fluids
Certain situations require positive-displacement pumps, such as a diaphragm pump. Diaphragm pumps are available in a wide variety of materials and elastomers. Advantages include few moving parts and simple operation.
"[Diaphragm pumps] will handle very viscous (thick) materials and create full discharge pressures without regard for any certain position on the performance operating curve," says Trumble. "Traditionally air driven, but also engine and electric fitted, they are generally of low volumes."
Diaphragm pumps are particularly suited for low-flow applications with muddy water. "But they can only handle low flow and low head (pressure)," says Conway.
"We sell quite a few diaphragm pumps, primarily for thick, muddy jobsite dewatering," Widrick notes. A common use is pumping out footings. "That is really when they do a good job. The advantages are they can run dry, they are relatively inexpensive, they are pretty portable and they are relatively small."
Trumble adds, "They are quite suitable for stripping of low point water collection in ditch and tank bottoms."
Because they can handle both equally, it generally doesn't make a difference to the pumps if they are moving air or water. "The major disadvantage is that diaphragm pumps require a lot of maintenance," says Soto. "The back and forth action on the diaphragm tends to wear it and other components out quickly.
"It is difficult to put a time of use on the diaphragms before needing to change them, as pumps will vary," he continues. "However, it would not be uncommon to change them monthly on continual use."
Diaphragm pumps are also not ideal for liquids containing abrasive solids. "Diaphragm pumps are susceptible to a relatively short diaphragm life, depending on the product being pumped," says Evans.
Go with the flow
To ensure proper pump selection, it's important to know the answer to some simple questions. "This includes the lowest and the highest level of the water to be pumped, the quantity of flow required, the distance you are going to pump the water and where you are going to discharge the water," says Widrick.
The flow rate can be calculated based on the time frame you have to pump out a given area. "Then you need to consider any obstructions to the pump layout. From there, we should be able to ballpark and pick out a correct application for the customer," says Widrick. "It is really a pretty simple step-by-step process that, with the correct information, [ensures] the right pump can be chosen nine times out of ten."
Evans recommends picking a minimum of two pumps to handle the peak flow. "This avoids putting the entire bypass on one machine, and will avoid short cycling of a large pump. This is before adding a standby or backup pump to the selection," he states. In addition, all pumps on the job should be the same size to ensure redundancy.
"All pump manufacturers show curves that indicate the hydraulic potential of a pump," Evans continues. "Keep in mind that hydraulic performance can be greatly affected (up to 50%) by the suction and discharge length associated with the application. As a general rule, the elevation needed for the application should be half or below half of the pump shutoff elevation. This rule accounts for hose/pipe friction loss."
Height also affects the pressure required by the pump. "Mostly, the pressure required is found by adding the vertical heights needed and the friction losses through the pipes," says Conway.
Given the complexities involved, don't hesitate to seek experienced assistance. Pump suppliers can be a vital resource to help you quickly assess project requirements. For example, Conway notes, "We offer a pump application checklist that the customer fills out, and the pump supplier assists with the best selection for the job."
For more complex dewatering tasks, you may want an expert on site to size up the situation. "Within a couple of minutes, they can typically come up with a pump selection size, whether it is a high-head or low-head application," says Widrick.
It's important to seek out qualified advice. "Pump distributors/dealers have general knowledge of pump applications. But the best place to get advice is from firms that routinely use pumps in everyday operations and have the background in pump systems and applications," Soto emphasizes. "There is no better tool than experience."