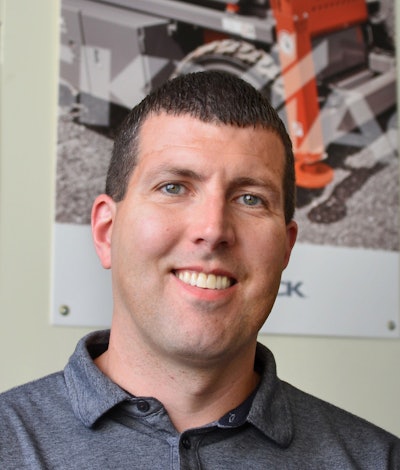
New North American Access Equipment Standards – put forth by the American National Standards Institute (ANSI) and The CSA Group in Canada - will result in many changes to machine design when they're finalized later this year. Following are the main points to be aware of.
Load sensing – Most machines will actively monitor load and NOT operate with normal functionality if overloaded beyond rated capacity.
As with current standards, it is the responsibility of the machine operator to ensure the unit is not loaded beyond the restrictions displayed on the unit by the manufacturer. Moving forward into ANSI A92.20 or CSA B354.6 (A92.20/B354.6), however, MEWPs must be equipped with a means to avoid overturning and exceeding permissible stresses, which is most commonly a load sensing device that will disable the normal elevating functions of the machine and sound/flash an alarm when overloaded.
Rental companies and contractors alike should be aware that jobs which had previously been inappropriately completed by overloading a machine will require different planning and execution with new units that will be designed to inhibit this misuse. While load sensing does add some complexity to units, equipment operators should be aware that identical technology has been in use in other markets (such as Europe and Australia) for over 10 years; the required modules are extensively field tested and validated in those market places. Scissor lifts will generally use a combination of scissor stack angle sensors, pressure transducers on the lift cylinders and/or load sensing pins, while booms will typically use load cells to measure platform load. While there are some differences in implementation for manufacturers, load sensing affects booms and scissors similarly from a fleet/operation perspective.
New wind force requirements – Increased weight and reduced capacities in outdoor/wind conditions.
At a high level, wind load is assessed more aggressively under A92.20/B354.6. Scissors and vertical masts will feel the sharpest impact of more conservative wind load assessments, with a larger change in added weight. Narrower electric slab units are more affected than the wider, heavier rough-terrain units. It should also be anticipated that personnel capacities for outdoors (wind-rated) use will differ under A92.20/B354.6 from current A92.6/B354.2 machines. For example, a typical A92.6/B354.2 scissor might have a two-person capacity with a 28-mph (12.5m/s) wind rating. The same scissor lift under A92.20/B354.6 might have a two-person capacity under a 0-mph wind load (often referred to as “indoors use”) and one-person capacity at up to 28-mph (12.5m/s) winds (often referred to as “outdoors use”).
For booms, while some added weight can be required, standard 40- to 80-foot self-propelled booms are generally much less affected by the wind rating requirements of A92.20/B354.6. Expect slight changes in weight and more stringent restrictions on material size supported by glazier kits, pipe racks, etc. Personnel capacities are unlikely to be affected on larger models, but compact electrical units might vary in a similar way to scissor lifts.
New stability testing requirements - Expect to see foam-filled tires.
Variations exist in the calculation of overturning and stability moments between A92.20/B354.6 and A92.5/A92.6/B354.4/B354.2. These mostly have only subtle effects on machines, but the largest change comes about from how A92.20/B354.6 treats the difference between air-filled and foam-filled tires. With A92.20/B354.6, the demand is made that machines are tested with a deflated air-filled tire in the worst possible position, making air-filled tires unattractive from a feasibility standpoint; you can expect to see foam-filled only (no air-filled tires) on the vast majority of RT scissors and RT booms under A92.20/B354.6.
Entrance gate with toe boards replaces chain entrance on electric scissors and vertical masts - Toe boards at entrances on booms.
Due to its simplicity and cost effectiveness, the most prevalent scissor lift entrance in the North American market today is the chain gate entrance. With the move to A92.20/B354.6, flexible devices are no longer permitted to be used as platform gates and toe boards have to be present on all areas of the platform, including the entrance. This mandates a shift away from chain gates to half height, full height or saloon-style gates for all scissors. Boom lifts will keep broadly the same entrances as today’s machines, with the exception that the toe boards must cover the entrance area.
Railing heights - Compact DC scissors now mostly equipped with folding instead of fixed rails.
Under the current standards, smaller scissor lifts in the North American market have solid, non-folding rails approximately 1m (39.5”) in height. A92.20 mandates a railing height of 1.1m (43.5”) from the platform floor. This additional height results in these smaller units no longer being able to fit through standard door heights with the rails deployed, necessitating a change to folding rails as standard on a number of units. Additional familiarization will be required with end users.