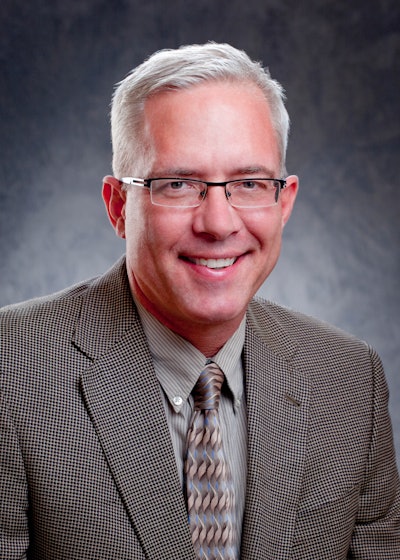
This traditional means of working at height can be dangerous, but getting American workers to adopt safer powered access alternatives comes with challenges
Go anywhere building work is being done and you will likely find a ladder. Dating back at least 10,000 years, ladders are even older than the wheel and definitely some of the oldest man-made technology still in use. But despite their ubiquity and endurance, ladders are often not the best tool for the job, especially in this day and age when there are so many safer alternatives for low level access.
According to the Center of Disease Control and Prevention, a study by PhDs Socias, Menendez, Collins and Simeonov examined ladder falls and discovered that:
- 43% of fatal falls in the last decade have involved a ladder
- Among all workers, 20% of all fatal falls involved ladders
- Among construction workers, 81% of fall injuries treated in U.S. emergency rooms involved a
- ladder
Statistics aside, it’s clear the use of ladders comes with some hazards. But should we stop using them? Should they be banned from US jobsites? We asked a panel of industry experts what they think. Following is an excerpt from that discussion.
Jenny Lescohier, editor, Elevating Safety: Ladders are a low cost and efficient tool – how much are they used on today’s construction jobsites and should they be the first choice to gain temporary access to work at height?
Tony Groat, manager, IPAF North America: I believe ladders should be the last choice for gaining access to work at height on a construction site, and we need to raise awareness to the assumptions and decisions made in their use. A proper site risk assessment is required and must identify hazards, evaluate risk and develop control measures. This includes selection, provision and use of suitable equipment to perform the task.
While often not suitable equipment for the task, ladders are used commonly on many construction sites for the simple reason that they are a low cost option, readily accessible, versatile, practical and effective in the correct work environment, providing temporary access to work at height. In my experience, they are perceived as a “tool of the trade,” require little to no training and as one is in every household – so everyone assumes they know how to use one.
TJ Lyons, Eastern Region EHS director at Total Facility Solutions: There are more ladders than we need on today’s jobsites, that’s for sure, and it’s troubling to me. In 2011, I developed the “Ladders Last” program for Turner Construction Co. in New York, NY, with the aim of educating those in construction that ladders are inefficient and often dangerous. That was a real game-changer and still a successful program there. Ladders should always be considered a last resort.
But the message has less to do with safety and more to do with how fast we can get the job done. The biggest obstacles we face are A) we’ve always done it this way, and B) we already have the ladders.
Trying to get rid of ladders based on a safety message is a nice idea, but people really want to hear about efficiency, getting the job done faster with some profit. In Europe, where the use of ladders is far less than in North America, studies have shown it is three times faster to do work off a work platform than a ladder because you’re unrestricted, you can use both hands. Based on inefficiency alone, ladders are a one of the most archaic, common devices on our sites.
Phil Holwell, senior director of engineering at JLG Industries: Ladders are used everywhere, mainly due to their portability, but they’re also often used because operations are being done out of sequence; somebody comes in and has to use temporary access like a ladder to work around something or work in a space where work should have already been done. Obviously, a ladder is a simple, portable way of getting to height. Some ladders are getting more and more complex – with wider bases and platforms at the top - as they try to address safety concerns, but then they’re not as portable.
There’s nothing wrong with a ladder for a lot of jobs, but the risk assessments of those jobs is crucial. One of the important elements is how long are you going to be on that ladder? Fatigue is a key issue. Standing and balancing on a step is tiring and leads to fatigue, and if the ladder is being used for too many hours, that’s when people take shortcuts. Coming down and missing the bottom step is one of the most common mistakes that leads to injury and it’s very often related to fatigue.
Elie Nassif (MOL), provincial specialist, construction at the Ontario Ministry of Labour: Ladders are quite commonly used on today’s construction jobsites, mostly for access and egress. Workers do also work off ladders – especially step ladders. They should definitely not be the first choice to gain temporary access to work at height. There are other means, both in terms of immediate safety – providing better protection against falls – and in terms of ergonomics. Scaffolds and powered elevated work platforms are definitely a better choice than ladders, both in terms of access and egress and for doing the work.
Granted, there are situations where ladders are easier to use – such as when the location is too tight to allow other means of access. However, a work plan and hazard assessment are advisable prior to deciding to use ladders on an ongoing basis. Some of the concerns are fall protection, proximity to overhead power lines (especially when moving the ladder from one location to another), plus fatigue and ergonomic considerations.
Lescohier: What are the primary hazards associated with using ladders and how can they be mitigated?
Groat: According to the Bureau of labor statistics, 20% of fatal falls were from ladders in 2009 and another study identified that 50% of all ladder-related accidents were due to individuals carrying items as they climbed. As simple as ladders appear to be to use, ladder violations are always in the top 10 OSHA violations cited, the 6th highest in 2017. OSHA states that training of the personnel using ladders can prevent 100% of the accidents. Falls are the leading hazard and electrocution is another potential hazard.
Falls are mostly caused by the use of faulty ladders, the improper set-up of a ladder, the incorrect use of a ladder, and selecting the wrong type of ladder for the task.
Eric Medley, director of sales and marketing at Bauer Ladder: Overreaching is a problem, and it’s an issue of the operator not being patient. It’s the same with missing the last step. If the user knows the proper way to use the ladder and has the patience, it’s not a dangerous tool to use.
Holwell: Hazards are common with any jobs working at height. With ladders, those hazards often center around floor conditions and whether the ladder is secure on the floor or ground surface. The process of climbing up and climbing down, often with hands full, becomes a fatigue issue. The constant repositioning leads to shortcuts. It’s more common on the small jobs. When you get to larger, professional businesses that are taking an ethical approach to how they look after their people, even the client doesn’t want to have safety incidents on their site or on their project, so they’re doing a proper risk assessment and at least a review of the available alternatives. Risk assessment for a ladder really should take into account whether it’s a temporary job, will the work at height require movement where the operator needs both hands?
Lyons: By about 2:30 in the afternoon, someone working on a ladder all day is just physically exhausted and not paying much attention, so they miss the bottom step. Don’t kid yourself, that’s due to fatigue. People always talk about electrocution as a common hazard, but it’s really fatigue. Ladders are a dangerous device as designed and if you are not paying enough attention a fall will land you in the ER 25% of the time.
Lescohier: Have incidents with ladders increased? If so, why?
Groat: A consumer product safety commission report states that over the last 10 years the amount of ladder-related injuries has increased 50%. Ladders seem to be an easy, fast and economical solution to gain access to work at height. The concept of completing work fast to make money permeates our culture. We think, “Should I reach a little farther or add time to climb down and move the ladder?” or “It’s a little short of what I need, but I’ll make it work…” We’re creating a culture focused on doing more with less, and it has consequences. Are proper risk assessments being completed prior to all tasks being performed? Are the correct tools being selected/provided for the task? Do workers follow the work methods defined in the risk assessment or do operational failures interfere with safe-use planning? Can a worker be expected to work standing on a ladder all day, and maintain balance while climbing up and down?
Lyons: Based on my observations, I’d say we have fewer ladder incidents because we’re using fewer ladders. Around 2011-12, the idea of phasing out ladders came about, and I suspect ladder use has declined since then. The real area to look at for ladder fatalities is in residential construction. Those folks don’t pay the needed attention to safety and are very production driven. Large commercial companies have time to stop, have the revenues to look at alternatives and then pay for them. That’s not something you can easily do in the trades.
Holwell: If anything, the use of ladders is probably as prevalent as it has always been, relative to smaller companies, due to their functionality, ease of use and low cost. What has changed is the use of ladders is becoming less acceptable on construction jobsites around the world, to the client, and to the company employing the workers. The cost of incidents and the damages are escalating, so it’s less acceptable and more costly to use a ladder in a professional scenario.
Lescohier: What are the employer’s requirements and responsibilities when placing workers at height?
Groat: In addition to compliance with hazard-specific standards, all employers have the duty to provide a work environment "free from recognized hazards that are causing or are likely to cause death or serious physical harm."
Nassif: In Ontario, the employer must be adequately protected by the highest ranked method that is practicable; guardrails would be the first priority, followed by a travel restraint system (which would not allow the worker to reach any edge or opening from which s/he may fall, followed by a fall restricting system (which is a type of fall arrest system which would limit the fall distance to 0.6 m (2 feet), a fall arrest system, then a safety net. Should the worker be exposed to a fall and be using a personal fall protection system or be protected by a safety net, there are two sets of training that the worker must have: 1) chief prevention officer (CPO) approved training delivered by a CPO approved training provider, and 2) training provided by the employer on the specific system the worker is using. In addition to the above, should a fall arrest system be in use, the employer must develop written procedures for the rescue of a worker whose fall would have been arrested by the system in use.
Lyons: In the US, we’ve typically blamed the worker for a fall, for making a mistake, but in most cases, we provide workers with a poor tool and expect them to make the most of it. In the last 15 to 20 years, however, we’ve started focusing on the tools and equipment that make it safer for the workers vs. workers having to make a decision to be safe. The job of a general contractor is to find ways to work faster and easier, which by default, will often be safer.
Holwell: In the UK, the “Shattered Lives” program has been a real drive toward awareness of the impact of severe injuries in the work place. That initiative, Health and Safety (Offences) Act 2008, introduced in 2009, increased the fines available to the courts and also introduced the ability to imprison individuals for H&S offences (not just for fatalities). Ultimately, it really elevated the knowledge about the hazard of falls from height. Previously, the company could be sued for negligence, now individual managers can be sued and taken to prison. It helped push proper risk assessments and got employers to pay close attention to any work at height, and to any traffic on the jobsite. That documentation is now required by law. I can foresee a time when the legislation will change in the US too. There are already locations in the states where more stringent laws are being applied… like New York where unionized work forces are pushing for safer ways of working. New ANSI standards for MEWPs are now mirroring the most stringent requirements in the world, as opposed to being less stringent in the US. That being said, I think there are signs that people being injured in the workplace is becoming less acceptable, and as global companies are more and more careful about ethical business practices, and also pushing and driving for safer work practices, the culture will find a way of improving standards that have to be met without going to punitive legislation.
Lyons: Fatalities in the UK have dropped due to their Shattered Lives program – focus on falls. It’s produced remarkable results. Here in US, when someone falls off a ladder, no one goes to jail for it, but in the UK, the employer is held liable. And it’s not just ladders but falls from height. If everyone knew they were going to be held liable, I think we would all look a lot closer at falls in the US. And we learn from tradition. Today’s young apprentices are on jobs with people who learned the trade in the 70s and 80s. It’s going to take some time to get rid of tribal learning, our passing of old ways down from generation to generation. We’re trying to get it in the minds of our youngsters starting in the trades that maybe you shouldn’t be using a ladder.
Lescohier: What are a user’s/employer’s responsibilities when selecting the right equipment for a task?
Holwell: There is legislation around the standards that some of the equipment has to meet but typically, there should be a risk assessment of the job being done. OSHA would say, ladders last. There are best practices, different ways of mitigating risks, and if you can’t eliminate the risk, mitigate it by lowering its severity. Near miss reporting is also important. Employers should be recording times things nearly happened, recognizing what the hazards were and eliminating the risk before something happens.
Nassif: The employer’s responsibilities reside in the adequate choice of the most suitable system to use, making sure that the workers are adequately trained and supervised and that written rescue procedures are in place. The worker’s responsibilities are to follow the instructions provided by the employer and the training with respect to inspection, maintenance and use of the system.
Lescohier: How is that accomplished? What are the tools available to assist a contractor in making the right decisions?
Nassif: The employer needs to do a hazard assessment and a job planning to this effect. Health and Safety Associations provide related services. There are also private consultants offering their services. Unions also provide education to their members in this regard. Information on the Ministry of Labour’s website may be used for guidance.
Lescohier: Do regulations support or prohibit use of certain equipment to gain access?
Groat: According to the Ministry of Labour, Ontario - Ladder Safety in Construction, July 2011, “Ladders should only be used to work at heights as a last resort, when location restrictions prevent the use of a work platform.” BC Worksafe says, “… They should only be used if safer alternatives such as scaffolding and elevated work platforms have been assessed first and are not reasonably practical for the task.”
Nassif: Yes, the Ontario Regulation for Construction Projects allows the use of ladders, scaffolds, elevating work platforms, ramps and stairs to gain access. They put stringent conditions for the use of cranes (for instance) to gain access. More restrictions are placed on working off ladders: work is encouraged to be conducted off a work platform or scaffold as these provide more room for the worker, are more stable and sound from an ergonomics perspective. Working off ladders should be the last resort. In all instances, the user of the equipment or tool must comply with the manufacturer’s operating manual in terms of use, maintenance and inspection of the equipment.
Lescohier: What other options do contractors have to place their workers at temporary work at height?
Lyons: We need to start a conversation about other options and the whole idea of hand-powered lifts, which can be thrown in the back of a pickup truck, cranked by hand, etc. There are many opportunities for these low level access methods.
Holwell: The vast majority of ladder applications are in 4- to 20-ft. working heights. Most jobs typically require getting a device that will go through a standard doorway, won’t damage flooring, and can go in and out of personnel elevators. There are a variety of powered and non-powered platforms that all have these things in common. They eliminate the risk of not being able to hold on while moving materials up and down the ladder, the risk of missing that bottom step or working at the top of a set of steps. There are a wide range of options in the market including our own Eco Lift, which features an energy storage system that enables a very light hand crank action to elevate the platform to 5 and 7 feet, and the LiftPod, which uses a hand drill to power it. That machine, available in 7- and 14-ft. lift heights with respective weights of 200 and 320 lbs., can be broken down to 50-lb. parts for easy transport. Both options allow workers to elevate his/her tools as well as some materials.
Medley: We’re seeing ladder manufacturers place a greater emphasis on platform ladders than ever before, where the user has a place to stand while he works. All of us are also working toward taking some of the weight out of extension ladders wherever we can, in order to minimize injuries associated with ladder handling, which is more prevalent than falls from ladders. As a manufacturer, we have a responsibility to create a product that addresses the needs of our customers in the safest way possible.
Holwell: To be a viable ladder replacement, machines have to be light and maneuverable enough to get to the site, be able to be transferred in smaller and lighter vehicles, and easily moved around the inside of the workplace. From the operator’s perspective, they require little effort, greatly reducing the fatigue of moving and positioning the machines. There’s room for tools, workers can go up and down hands free, there are no steps to miss, and there’s a rail around the platform, keeping the workers in a safe position, not standing on a step. Far from reducing productivity, replacing ladders with personnel lifts significantly increases productivity due to reduced fatigue, correct height and positioning, the ability to freely use both hands and to move around the platform, the use the tool trays, and the rated platform capacities of 330 lbs.
Lyons: Going back to tribal knowledge… we’ve done a poor job of educating people about alternatives to ladders. We need to be encouraging contractors to look at their inefficiency. We know you can work faster and easier from a lift vs. a ladder but we formed our discussions incorrectly. All people want to hear is what’s in it for them. Will it make the job safer? Honestly, that’s not a big instigator of change for most firms. If the ladders last conversation is based on increasing profit and schedule, they’ll listen very closely.