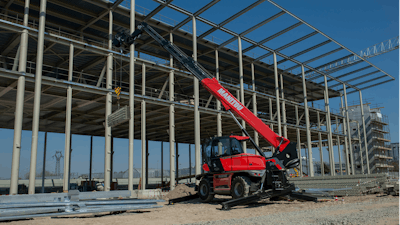
Understanding how to use load capacity charts is crucial for proper selection and safe application of a number of machine types, but perhaps none more so than telescopic handlers. These versatile units are used to transport, lift and place materials and tools of varying weights, shapes and sizes using a selection of different attachments, often while operating on or over uneven or rough terrain.
“Since telehandlers also have the unique potential to extend those materials away from the vehicle with the telescoping boom, it is up to the operator of the machine to assure the material it’s lifting, placing or carrying is within the rated capacity of the unit,” says John Boehme, senior product manager, JLG Industries.
Each telehandler comes equipped with a load chart that outlines the different attachments it can support, as well as the machine’s operating range and operating envelope. But what goes into developing the charts and why is adhering to the recommended parameters so critical to proper, and safe, operation?
What Load Charts are Based On and How They’re Applied
“Load charts for all rough-terrain telescopic forklifts used in North America are created per the ANSI/ITSDT B56.6 Standard. This design standard provides a consistent load chart development process for the industry,” notes Steve Kiskunas, product manager - telescopic handlers, Manitou Group. “Specific engineering tests are conducted with each machine to determine the correct capacity for the machines in various positions. Load charts indicate the maximum capacity of the machine at various lifting ranges.”
The three main aspects of operation taken into account within load charts are the overall weight of the load, the height and distance at which the load needs to be placed or picked up and the load capabilities of the machine.
Shown is a sample load chart from JLG with an explanation of how to read it.JLG Industries
Attachments are also taken into account, with the operating envelope located relative to the load center position of the attachment being used, says Boehme.
“The most common load chart will be for the standard factory-supplied forks with the load positioned no more than 24 in. from the carriage backplate,” says Brian Hatch, AMS-Merlo territory manager and tech trainer. “However, attachments other than forks can possibly have a load center greater than 24 in. from the backplate.” He adds that load charts for forks, grapples, jibs, buckets, etc., are permanently mounted on all Merlo models.
Other manufacturers have also chosen to provide separate charts to match approved attachments. “Each Skyjack telehandler has its own capacity charts for the various carriages, forks and attachments that can be used with each machine to ensure safe operation,” says Rafael Bazzarella, product manager. “These options allow operators to use the machines in various types of applications, making the telehandler a very versatile and productive machine.”
Specific engineering tests are conducted with each telehandler to determine the correct capacity for the machines in various operating positions.AMS-Merlo
“The loading zones we subsequently supply to our customers on these load charts can be easily translated into what capabilities a particular project will need in terms of height, reach and load,” he adds.
Load charts provide the guidance required to select the right telehandler for the task. “For general use, customers often first determine the maximum weight of the materials they will be using on a project,” says Kiskunas. “Then, they check that weight vs. the approved working ranges for that weight range on the machine load chart. If the customers’ maximum material weight is equal or below the load chart weight for the areas they need to reach with the materials, that machine should do the required work.
Follow the Charts to Minimize Mishaps
Load charts are also used to maximize the chances of safe, successful load placement. “That is essentially the function of the load chart — to provide the operator with the information regarding a machine’s operating range and envelope for the various carriages and attachments available for the specific unit they are using,” says Bazzarella. “By working within the load chart, the operator ensures the safe operation of the telehandler and protects the equipment from damage due to overloading.”
Watch: How to Read a Load Chart
“Understanding load charts and especially load centers of a particular lift project is one of the most important aspects of operating a telehandler safely,” Eckhardt emphasizes. “Operation of a telehandler beyond the scope of the load chart can and will directly affect safety of the operator and nearby personnel or property, safety of the load — which could have considerable value itself — as well as can shorten the life of a machine by causing early structural failures, component and hydraulic overloads and even dropped loads.”
To ensure safe operation, each Skyjack telehandler has its own capacity charts for the various carriages, forks and attachments that can be used with each machine.Skyjack
Merlo offers an anti-overturn protection system that provides a safety factor to keep the machine from overturning even if the operator makes a mistake in applying an attachment load chart reference. “The length sensor, angle sensor and weight sensor provide the machine’s computer with a constant equation that calculates the safety factor and capability of the machine,” Hatch explains.
Lack of or incorrect calculation of the load center of the material to be lifted can also hinder machine efficiency. “The load center can greatly affect the capacity of a machine,” says Eckhardt, “and often complaints of lack of ability to properly lift a load are actually a result of grossly underestimated load centers or complete lack of attention and understanding of the load center at all.”
Misjudging the center of gravity, particularly for larger loads, and mispositioning the load on the forks is a common mistake, Bazzarella agrees. “Another mistake would be using the higher of two capacity values when there are intersections in the capacity regions,” he adds.
Training on how to properly read and apply load charts is essential to avoid these and other common misapplications. “It’s extremely important to train telehandler operators on the proper use of load charts,” says Bazzarella. “Understanding the importance and working within the load chart limits for the various approved carriages and attachments helps prevent accidents and abuse of equipment.”
Set Yourself Up for Proper Lifting
Before using a telehandler for a particular lift, it’s important to identify:
- the weight of the load and its center of gravity to ensure that it is correctly positioned on the forks;
- the height it will need to reach;
- the forward reach required;
- and the model’s load capabilities.
Once equipped with this information, the load chart offers guidance that will allow the operator to confidently utilize the machine. “For example, once you have successfully paired the weight and telehandler model, you can use the load chart to assess the load placement or retrieval position,” says Boehme. “Because boom angles and extensions are an integral part of every load capacity chart, you will use boom angle and extension information to place or retrieve the intended load at the required height and reach.”
“With this information, the operator can reference the load chart to determine the maximum boom angle and extension allowed and then determine if it’s safe to continue with the lift or if the machine will require repositioning for safe operation,” Bazzarella adds.
The operator should always have load charts present on the machine for the attachment he or she is using.Xtreme Mfg.
To make this easier, Manitou’s MRT 2260 has a preloaded attachment load chart database that helps ensure the correct load chart is applied when an attachment connects to the machine.
Merlo offers a built-in/onboard weighing screen on its telehandlers that “eliminates all the calculations and guesswork of the load charts for the operator,” says Hatch. “This screen will give you three readouts that help the operator stay informed of what the machine is capable of and what is currently being lifted,” he notes. Readouts include the current weight on the forks/attachments; the maximum capacity of the machine at that particular moment in time; and the maximum capacity of the machine.
Yet, even when such technology is available, it’s still important that telehandler operators know the basics. “Training helps operators understand the basic assumptions used to develop the load charts. The load is centered in a 4’ x 4’ x 4’ homogenous cube — a 24-in. load center or the center of 48-in.-long forks,” says Kiskunas. “Loads which do not have this load center, or loads that are unbalanced, can result in load and/or machine instability.”
It’s also good to have a plan in place. “A proper plan for a lift is essential as one needs to understand the load weight, size of load and the specific worksite dimension,” says Eckhardt, “including any obstacles that may be encountered when performing the lift.”