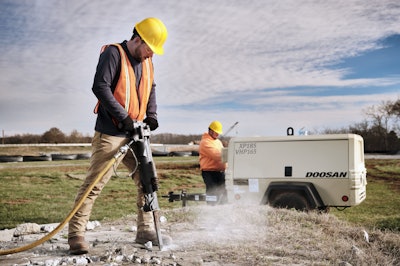
Air compressors are some of the most crucial tools in a construction or rental business. These machines power a vast range of other tools, from nailers to pneumatic wrenches to paint and air sprayers. However, not every type of compressor is ideal for every end-use.
Because compressed air is such a versatile resource, compressors come in a wide array of specifications. As a result, effective air compressor use hinges on choosing the right type of machine for the job. Here’s a look at seven common types of compressors and their ideal applications.
1. Rotary Screw
Air compressors fall into two main categories based on how they operate: positive displacement and dynamic. Positive displacement options, like rotary screw compressors, provide a constant flow regardless of outlet pressure. In a rotary screw machine, this happens by a pair of screws rotating in opposite directions to compress air in a sealed chamber.
One of the biggest advantages of a rotary screw compressor is that it can operate continuously as long as you need it to. They’re also highly durable, often outlasting other types by a couple of years or more. As a result, they’re ideal for prolonged heavy-duty use, like powering jackhammers or sand-blasting operations.
The main downsides to rotary screw compressors are their price and maintenance needs. They’re often more expensive than other positive displacement options and require more care, so smaller operations may want an alternative.
2. Reciprocating
Another positive displacement option is the reciprocating, or piston, compressor. As the name implies, these use pistons to compress and displace air within their chamber. These are among the most powerful compressors for home use, making them a popular choice.
While rotary screw compressors can produce more power overall, reciprocating options can generate a lot with low energy consumption. They’re also more compact than rotary screw machines, making them better for shorter, more flexible jobs. This low energy consumption and portability make piston compressors an appropriate choice for powering hand tools.
However, these compressors produce more heat and noise than other displacement machines, so they’re not ideal for extended continuous use. For many construction jobs, that’s not an issue, but they may not be the right choice for heavier machinery.
3. Scroll
The third main type of positive displacement compressor is the scroll compressor. These machines use two circular scrolls, one that stands still and another that turns inside it to compress air. This design results in fewer moving parts and reduced vibrations, leading to improved longevity.
Scroll compressors produce the cleanest air according to ISO standards. As a result, construction jobs or companies that have to adhere to higher environmental standards may want to use these machines. They're also versatile, operating at various intensity levels.
While quiet and easy to maintain, scroll compressors don’t produce the most power. Heavy-duty tools and machinery may require a different type of compressor, but more passive applications are ideal for these.
4. Centrifugal
Unlike the first three entries on this list, centrifugal compressors are dynamic. That means they draw air in from the outside rather than using a closed reserve of air. In a centrifugal machine, that happens thanks to a rotor called an impeller spinning inside a cylinder to force air inside.
Some centrifugal machines use multiple stages to increase pressure, delivering more power. Multi-stage compressors can deliver remarkable horsepower, making them ideal for powering heavier equipment. Like rotary screw compressors, these machines can also operate continuously, suiting them to longer jobs.
Centrifugal compressors are also highly affordable compared to similar-horsepower alternatives. However, their reliance on fast-moving parts makes them more prone to issues like stalling or choking.
5. Axial
Axial compressors are another type of dynamic machine. Instead of using an impeller, these use rows of fan blades within a shaft. As air passes through each row, its velocity gradually increases, leading to higher pressure.
These compressors are typically smaller and lighter than their centrifugal counterparts and operate at higher speeds. This lets them provide constant flow rates at high volumes, but often with less pressure than alternatives. You’ll often find them in pumping applications, thanks to their consistency and energy efficiency.
Axial compressors are a key part of jet engine designs, but in construction, you’ll find them in pumping or electricity generation. Overall, though, these are rarer on construction sites, thanks to their high costs.
6. Oil-Flooded
Another way to divide compressor types is by their lubrication, which falls into two categories: oil-flooded and oil-free. Oil-flooded compressors, as their name suggests, have lubrication inside their inner workings. More specifically, they have closed, oil-lubricated compression chambers.
Rotary screw and reciprocating compressors often have oil-flooded designs. The constant presence of lubrication means that oil-flooded compressors are often more durable. However, they also run the risk of seeping lubrication, potentially contaminating the compressed air.
The FDA requires oil-free air in some industries, so construction teams adhering to higher cleanliness and safety standards should avoid oil-flooded compressors. For most low-power construction equipment, though, these are a safe and cost-effective choice.
7. Oil-Free
Oil-free air compressors, by contrast, don’t have any oil in the compression chamber. Instead, they have built-in, lasting alternative lubrication on their moving parts. As a result, these can produce air without any traces of potentially hazardous oil.
Centrifugal compressors are typically oil-free, and some oil-free rotary screw and reciprocating compressors exist, too. These can be more expensive, but they’ll produce cleaner air and often work at lower temperatures and noise levels. These advantages make them ideal for construction in busy areas or eco-friendly worksites. Oil-free compressors are also better-suited for continuous operation since they require less upkeep. Over time, though, they may need additional work to last as long.
Get the Right Kind of Air Compressor for the Job
Like any tool in construction, air compressor efficacy depends on matching the right type of machine to the job at hand. The right choice can speed up or cut costs on a project, while a mismatch may incur unnecessary expenses and delays.
Understanding the different types of compressors is key to making the right choice. When you know what your options are, you can make a more informed decision, leading to better outcomes and more successful projects.