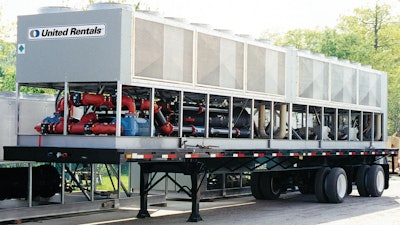
Planned outages are an important maintenance tactic in a utility power management strategy. They involve considerable planning, resources, and budget and help keep a power plant operating at maximum capacity. United Rentals has shared tips on how tapping temporary equipment solutions during a plant outage can save a utility time and money, and keep the plant outage on track so operations can resume on schedule.
Temporary equipment requirements, such as power generation, dehumidification and more, can often extend beyond owned inventory. Utilities need to consider every element of an outage plan to ensure the right equipment is ready and in-place at the right time. Rental equipment can fill gaps and ensure expensive machinery used to support outages does not sit idle during other parts of the year.
“Outage planning and execution is a large and costly undertaking. Temporary solutions can offset some of those costs and help utility operations resume in fast order,” said Jody Van Huisen, director of national accounts at United Rentals. “An equipment rental provider with deep experience in planned outages can leverage the knowledge they’ve gained to benefit a utility’s project. During the entire outage cycle, from planning to wrap-up, the provider should function as a collaborative partner who helps drive operational efficiency and productivity while keeping safety top of mind.”
Here are some temporary equipment solutions that can help utilities offset costs and potential lost productivity.
Power generation. Outages are planned to minimize disruptions, but there are still critical power infrastructure and support requirements for onsite contractors and the outage team. Temporary power generation is a must and is likely already included in pre-outage planning. But there are other important considerations. For instance, temporary transformers might be a good alternative option in place of generators. Also, if there is a need for validation of the primary electrical equipment, load bank, and circuit tests become essential.
Supplemental plant air. Often, when only a portion of the plant is down, there is still a need for plant and instrument air. Temporary air compressors provide critical redundancy for these air requirements when the plant’s air compressors are shut down.
Dehumidification solutions. Moisture buildup on turbine motor windings and blades during an outage can cause issues, such as corrosion and reduction of the turbine performance. Temporary dehumidification can dry up some of moisture-related issues and keep equipment running smoothly long after the outage is complete.
Fluid solutions. Build up from seasonal sediment and the inlet water source can cause serious issues and minimize megawatt output. Solid removal and elimination solutions can help maintain reliability during and after the outage. If boiler flushes or cooling tower cleanouts are part of the outage plan, pump, fluid transfer, storage and treatment applications may be needed.
Confined space work. Open excavations may require specialized safety equipment such as modular aluminum shoring boxes with guard rails, mounted ladders, and ramps. Pipe testing and bypass work often need even more specialized equipment. Plus, the confined space training requirements for the team should always be addressed with an expert.
Comfort cooling. In addition to the specialized trench safety equipment for confined space work, portable cooling may be needed. Confined space areas are prone to elevated temperatures, which can be a safety hazard. Portable cooling like air conditioners and blowers can help curb heat and create a safe, comfortable environment for the team.
Equipment tracking. Even with extensive planning and preparation, last-minute line items can make their way into a project and its budget. Tracking equipment utilization is one way to keep costs down and optimize craft worker hours. Also, the plant may need a certain piece of rented equipment only briefly during an outage, but a busy manager may not have time to notice that it is no longer being used and take it off rent. Using a web-based equipment management platform can provide transparency into owned and rented assets and help utilities order or offload any piece of rented equipment at any time.
Information provided by United Rentals and edited by Alexis Sheprak