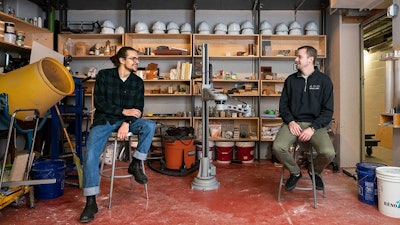
Recycled hemp biomass, water and lime. Cement, sand, fibres, plasticizers and water.
Combine the first group of ingredients in the correct ratio and you can make hemp building blocks that perform exceptionally well as insulation and, with the right compression, could also work as a structural material in walls. Mix the second set and tweak the formula properly and you can use a 3D printer to produce thin slabs of ultra-high-performance concrete.
Both are building materials with the potential to reduce our carbon footprint — and both are being developed by master’s students in the Carleton Sensory Architecture and Liminal Technologies (CSALT) laboratory in the basement of the university’s Architecture Building.
While the majority of Carleton students have spent the last 10 months learning from home on their laptops, Robin Papp (who literally has his hands in the hemp) and Sinan Husic (who is experimenting with concrete) couldn’t complete their master’s research without getting into the lab a couple days each week.
Architecture is an academic discipline that requires interplay with the physical world. Thankfully, Carleton’s Azrieli School of Architecture and Urbanism has the space — and the will — to find ways for students to safely continue in-person work that addresses global challenges such as climate change.
“Hands-on learning provides an entirely different way of knowing something, which is vital for architecture,” says Prof. Sheryl Boyle, who supervises Papp and Husic and secured the MITACS grants that fund their research partnerships with Hurd Solutions and the Canadian Precast/Prestressed Concrete Institute.
“Architectural imagination mediates our ideas or concepts and sensory experience,” continues Boyle.
“Both of these projects address the material makeup of our buildings,” she adds, “and the material makeup of our buildings needs to change.”
Following COVID-19 Safety Procedures
The CSALT lab is divided into three separate workshops. One is being used by Papp, another by Husic and the third by studio teaching fellow Jesse Bird, a recent architecture master’s graduate who is working on a building material made from recovered paper and cardboard.
All three follow Carleton’s COVID-19 screening protocol before coming to campus, wear masks when they’re in a shared space, and sanitize surfaces and door handles before they leave.
Hurd Solutions provides Papp with large amounts of hemp biomass — the byproduct of rope and fabric manufacturing, with virtually no THC content, that would otherwise be considered waste. He mixes it with water and lime and other natural additives and pours the resulting mixture into a 4-in. by 4-in. form, presses the material, and then removes the form to let it dry.
Because the “hempcrete” is breathable, it works well as insulation. Boyle likens it to breathable Gore-Tex, whereas the building envelopes we typically use today are more like plastic bags with supplemental ventilation systems — an important distinction at a time when COVID-19 has drawn our attention to the need for clean healthy air.
But Papp is also using a small hydraulic press to experiment with denser, stronger hemp panels that could be used as a structural material.
“It’s very much a hands-on learning process, getting a feel for it and playing with different ratios and mixtures,” he says.
Papp describes the process that he uses as “messy,” so he’s glad to have a suitable workshop. And though he misses the studio life that architecture students usually experience — bouncing ideas off one another in a large, shared open space — he considers himself fortunate to be able to come to campus at a time when so many others cannot.
“It’s very quiet,” he says, “and for me there’s an advantage to being on my own. The solitary research time helps with my thesis work.”
Experimenting with Low-Carbon Concrete
Husic sees Papp on occasion in the CSALT lab — “it’s nice to have human contact once in a while,” he says — but for the most part is similarly alone.
“I feel guilty sometimes because not all of my colleagues have access to the equipment.”
The lack of distractions allows Husic to focus on his research, which explores both digitally fabricated and handcrafted concrete. The final product of his thesis will be a life-size 3D printed concrete chair.
New methods of making concrete are being developed around the world, he explains, but this work is generally proprietary and secretive. Cement is very carbon-intensive to produce, so people are trying ingredients such as clay powders and recycled blast furnace slag and various fibres, plasticizers and other additives in the mix.
“It’s a fine chemistry,” says Husic, who uses a large 3D printer — a rotating arm with a one-metre radius atop a two-metre pole — to extrude concrete that cures instantly. “I’m experimenting with the formula to come up with the right recipe.
“This gives me an intimate understanding of how the material works on a variety of levels. What’s the thinnest you can cast it? What’s the thinnest you can print it? Concrete was basically the first plastic. You can form it into whatever you want.”
A half-inch-thick slab of the ultra-high-performance concrete he is working on could have the same strength as a six-inch-thick piece of conventional concrete, which on a large construction project can lead to significant carbon savings.
“This kind of research builds a thought process that’s transferable to any material,” says Husic. “People are thinking about the sustainability of materials in every industry. Architects typically work with technologies that other people invent and we try to use them in practical and unconventional ways. It’s great to be at a university and learn how some of these technologies really work.”
The Show Must Go On
Husic and Papp aren’t the only architecture students using their hands these days.
To support students who are working at home but still need materials laser cut, 3D printed or fine-tuned by CNC (computer numerical control) machines, as well as students and faculty who need to borrow cameras and other audio-visual equipment, the Fab Lab on the ground floor of the Architecture Building opened a take-out window for contactless service that’s booked in advance online.
“Students need to validate their designs in a physical way — designs and things like scale don’t come to life on a screen,” says digital craft technician Steve MacLeod, who built the fast food restaurant-like window, complete with a doorbell, microphone, speakers and pay system.
“Students need an opportunity to tinker. They have to do it in order to learn. And we’re taking all the steps we can to support them in a safe way.
“It’s actually good to keep it working.”
In early January, life will also return to the Pit — the open space at the heart of the Architecture Building — as Prof. Yvan Cazabon’s theatre production workshop gets rolling, one of a handful of courses that have been approved as face-to-face pilot projects at Carleton.
The workshop, which will bring together up to a dozen or so students from Architecture and the English Department’s Drama Studies program, incorporates all of the elements of staging a live show, such as set and prop construction, lighting design and video projection. One session each week will be conducted remotely and the other will be in-person on campus.
For the last eight years, the class has culminated in a performance for a live audience, everything from Shakespeare to contemporary theatre, sometimes in partnership with local theatre companies. This spring’s pandemic-era production, according to Cazabon, could revolve around an online broadcast or possibly an outdoor venue.
To satisfy the COVID safety requirements of Carleton’s face-to-face pilot process, Cazabon submitted an 18-page proposal, detailing how the space will be physically used and who will be present, mask and sanitizing protocols, ventilation, washroom access and the learning outcomes that benefit from face-to-face instruction.
“It’s hard to improvise when you’re separate from each other.
“It’s the action, as well as the environment, that give meaning to a concept,” he continues.
“Whether it’s set design or sound and lighting design, I can’t imagine working on these things with students in any other way.”