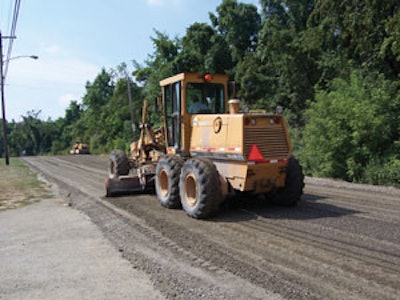
Full-Depth Reclamation (FDR) is offering small municipalities, like South Fayette Township, PA, a cost-effective way to reconstruct roads quickly with minimal disruption to traffic. Cutting Edge Reclamation, Murrysville, PA, recently completed a two-mile stretch of a two lane road in South Fayette, and the FDR process should provide this community with a well-constructed, long-lasting roadway.
South Fayette is a progressive suburban community located 10 miles south of Pittsburgh. Within the community’s 21-square-mile area, approximately 65 miles of township streets and highways must be maintained. As is the case in many communities, many of these roads were not designed to carry the weight and volume of traffic they now bear, but have evolved over time to their present composition.
One such road, Old Oakdale Road, is a heavily-traveled corridor knifing through the center of the township and also the location of the community’s junior/senior high school complex. When the triumvirate of Township Manager Michael Hoy, Engineer Dave Gardner and Director of Public Works Bob Barish looked at upgrading the traffic capacity on Old Oakdale, they worked with township municipal engineering firm The Gateway Engineers Inc. to explore the merits of FDR.
With a bid proposal featuring an FDR approach, Amity Asphalt Paving Inc. of Houston, PA was selected as the general contractor and Cutting Edge Reclamation was selected as the subcontractor to handle the FDR work. In addition to the FDR process, the original specifications called for the road to be widened two feet on each side prior to stabilization, with PENNDOT 2A limestone to be placed into slots cut along each side of the road.
Cutting Edge Reclamation used a CMI RS-500B Road Reclaimer to uniformly pulverize the existing pavement, subbase material and 2A limestone to a depth of 8 inches. The reclaimer/stabilizer was used to grind and pulverize the existing 20-foot-wide, 8-inch-thick road, as well as to blend the new limestone used to widen the road. This untreated material was then spread, graded and compacted to the new lines and grades of the redesigned roadway as directed by the engineer. Project specifications called for a new road cross-section crown of 3 inches, to be maintained by the contractor throughout the two-step stabilization process.
Stabilization
While the original specifications called for the use of an emulsified asphalt (E-5 or CMS-2) at an application rate of 1.5 percent (1.04 gallons per square yard) to take full advantage of the 7.2 percent residual asphalt content in the average 5.4-inch existing roadway material, Cutting Edge proposed conducting a parallel mix design utilizing 2-percent Type I Portland cement in addition to the 1.5-percent emulsion. This was explored to address a number of concerns facing the project, including heavy bus traffic from the school, heavy construction traffic working on the school renovation, the presence of slag in the subbase, the curing time of the stabilizer and the potential for excessive raveling as a result of heavy traffic during a prolonged cure time.
“We submit core samples of the road to a lab facility in order to develop the stabilizing mix design required for the project,” says David Cannon, president and owner of Cutting Edge Reclamation.
Coming up with the right design, based on the material to be blended and the gradation of the material blended, is critical to achieving the compaction and stability of the new base, which generally receives a hot mix asphalt overlay. The comparative mix designs indicated that the FDR process would yield successful results with either the emulsion-only or the emulsion/cement additives. The emulsion/cement additive, however, reduced the curing time from seven to three days, reducing the potential for raveling and increasing the stability of the compacted base by as much as 25 percent. Application of the Type I Portland cement was performed by pneumatic spreader trucks.
Controlling the process
Material gradation is controlled by the forward speed of the machine and the opening in the rear of the cutting system. The longer the material is confined to the cutting system, the finer the material will be when it’s spread out on the roadbed. When an additive like Portland cement is added, the base is re-cut to blend the cement with the other pulverized materials. The reclaimer/stabilizer Cutting Edge uses has an 8-foot-wide cutting system that pumps the stabilizer emulsion additive from a distributor truck. While the type of emulsion is determined from core samples taken prior to the start of the project, the reclaimer/stabilizer operator monitors the application rate of the additive, as well as the compaction density of the final pulverized and blended material after it has been compacted.
“With a formal mix design in hand, we’ll do a 100-foot control strip at the beginning of project and take six density readings. We’ll average the readings and use that as our target density to mirror the formal mix design for the project,” Cannon says.
Once the full depth of the existing pavement, along with a predetermined portion of the underlying subbase, has been pulverized and blended with an appropriate stabilization additive, the road is re-shaped and compacted to produce a strong, durable base suitable for a subsequent overlay. Cutting Edge uses a 10-ton steel drum vibratory roller for the initial knockdown compaction, followed by a 10-ton pneumatic-tire roller and then a steel drum static roller to smooth out the surface in preparation for the new overlay. The compaction process called for continuous monitoring by a trained and certified technician utilizing a nuclear density gauge, with the reclaimed base course ultimately being tested for compaction, smoothness and grade accuracy. It generally takes a week for the full-depth treatment to cure, allowing water from the emulsion stabilizer to evaporate. The end result is a new base that is stronger, more uniform and more moisture-resistant than the original base, resulting in a long, low-maintenance life.
Following the required cure time for the reclaimed base course, Old Oakdale Road received a 4-inch ID-2 binder course of hot mix asphalt and a 1 1/2-inch ID-2 wearing course.
When asphalt pavements fail due to fatigue cracking, rutting, shoving or deterioration of foundation support, Cannon says the FDR process allows him to add virgin aggregates or reclaimed asphalt pavement if it’s determined that the pulverized material does not meet the aggregate requirements for a sound stabilized base.
For customers like South Fayette Township, FDR with stabilization additives provides the following benefits:
- Stabilization increases the stiffness and strength of the base material. A stiffer base reduces reflections due to traffic loads, which results in lower strains in the surface. This delays the onset of surface distress, such as fatigue cracking, and extends the life of the road.
- Strong uniform support provided by stabilization results in reduced stress applied to the subgrade. A thinner stabilized section can reduce subgrade stresses more than a thicker layer of untreated aggregate base. Subgrade failures, potholes and road roughness are reduced.
- Stabilized pavements form a moisture-resistant base that keeps water out and maintains higher levels of strength, even when saturated.
- A stabilized base also reduces the potential for pumping of subgrade fines.
The FDR stabilization process also eliminates the cost of trucking away and disposing of the old asphalt pavement, as well as the cost of a new aggregate subbase, which is generally required in a full-depth pavement rehabilitation project.
“Since the existing asphalt pavement structure can be used to create a new subbase, it saves a lot of money, time and disruption for the community,” Cannon says. “The reclamation process provides significant savings, generally in the neighborhood of 40 percent compared to the conventional HMA mill and fill approach.”
The reclamation approach also provides customers with a lot of flexibility in how they can deal with a variety of road and soil conditions.
“The chemical additives allow a much wider application in addressing various road and soil challenges,” Cannon says. “Customers don’t have to haul away unstable subgrades and replace them with virgin aggregates. The reclamation/soil stabilization process allows them to add materials that will dry out wet soil and firm up soft soil conditions. We’re not a producer or distributor of one type of emulsion stabilizer. We find the right solution to the customer’s problem. We let the road and soil conditions determine the best solution we need to apply.”