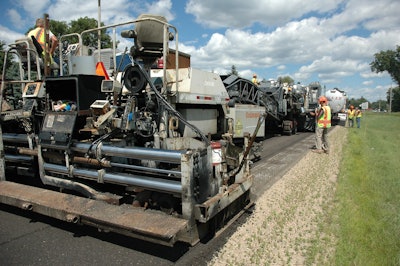
When road agencies are faced with how to upgrade a 20-year-old road structure that has received a hot mix overlay and several chip seal preservation treatments during its life cycle, another mill and fill approach seems like the most logical approach. But Sauk County, WI, Highway Commissioner Stephen Muchow has experienced the benefits of Cold In-place Recycling (CIR) on several previous projects, making it a natural solution to a 13-mile stretch of CTH H running from Reedsburg to the popular vacation playground of Wisconsin Dells.
“It’s a more cost-effective way to improve the road structure because you use less virgin material,” Muchow says. For this project the asphalt overlay was 3 inches thick versus the 4 inches typically used. “We’ve used this approach in the past and have achieved better results compared to milling a road and overlaying it with a new asphalt mat. We were getting quite a bit of reflective cracking coming through and we’re not experiencing that with past CIR projects.”
On 10-year-old CIR projects, Muchow says reflective cracking has been reduced by 50 percent. The other significant advantage to the CIR approach is that the existing material can be rejuvenated and put back down to provide a much improved base course. On a conventional mill-and-fill, four inches of the old surface were removed and replaced with four inches of new asphalt. On the CTH H project the four inches of old asphalt are milled, pulverized, rejuvenated with a PG 52-34 binder and then put back down as new base course. Two different mix designs were used since a portion of the road had received a chipseal treatment, raising the AC content of the material to be rejuvenated. Once the CIR portion of the project is completed, a new three inch surface course will be applied, which will not only provide a smoother ride for motorists, but also a more substantial road structure to accommodate the heavy truck traffic that use CTH H for convenient access to Interstate 90/94.
As far as Muchow is concerned, CIR is a viable option for most road rehabilitation needs. For a road supporting a lower traffic volume, a thinner surface course of virgin HMA would be required.
Project basics
On the day of the project visit, Mathy Construction was using a Wirtgen 2200 CR to mill, crush and mix the old asphalt before conveying the material into a CedarRapids CR561R paver. The Wirtgen 2200 can process up to three lane miles (12-1/2 feet wide) of material a day. Since the actual width of road (travel lane and shoulder) measured 15 feet, a narrow four-foot router milling machine was used ahead of the 2200 to make sure all existing four inches of the road surface was incorporated in the new rejuvenated base material.
The Wirtgen 2200 CR pushes the two tanker trucks that supply the rejuvenating binder and water, which are pumped into the mixing chamber. The average binder temperature in the AC tanker was 320°F (160°C) for optimum asphalt foaming per the CIR mix design.. The foaming process (two percent AC and two percent water per volume total material being mixed) allows the paving and compaction crew more time to achieve density. A Hamm pneumatic roller was used as a break-down roller and a Cat double drum vibratory roller used for finish rolling. t. The CIR process allows for opening the road to traffic during construction. . The CIR mixture generally cures within two weeks and then can be overlayed with an asphalt surface course. On this particular project, D. L. Gasser will place a warm mix asphalt (WMA) surface produced using Evotherm. D. L. Gasser will make the mix with recycled asphalt pavement (RAP) into the mix to further promote the overall sustainability of the CIR project. Further, enhancing the performance and sustainability of the pavement, the WMA asphalt is placed at 220°F (104°C).
“CIR is a cost-effective way to maintain roads because you’re recycling the material right onsite, so you’re not hauling it off and bringing in expensive virgin material,” notes Steven Krebs, P.E., WisDOT materials management chief, who was visiting the project along with other state DOT officials. On the Sauk County CTH H project, as with most CIR projects, the county achieved a 25 percent savings by using the CIR process.
This project was bid/constructed using WisDOT’s new special provision specification for CIR.... It’s the wave of the future in maximizing rehabilitation dollars to improve roads. For the CTH H CIR portion of the project, field engineers could direct repair of surface deviations greater than ½ inch between two surface contact points using a 10-foot straightedge. High points would have to be corrected by reworking, rerolling, trimming, milling or grinding. Depressions would have to be corrected by reworking or having a tack coat applied and filled with HMA immediately prior to placement of the surface course.
Contractor’s perspective
For Mathy Construction, the CIR process provided the best opportunity to deliver a quality pavement in a sustainable and cost-effective way for the customer.
According to Ervin Dukatz, vice president of materials and research for Mathy Construction, Sauk County Highway Department wanted a cost-effective method to restore CTH H. They realized it had some distress issues, particularly with reflective cracking., They were interested in an HMA overlay project that would provide more than a temporary “Band-Aid” and achieve a smoother, better performing road structure.
“By milling four inches deep, we’re able to remove a majority of the defects and by rejuvenating that milled material before putting it back down, we’re able to prevent many of those defects from coming back,” Dukatz notes. “The two primary advantages of CIR are reduced costs and improved pavement structure. Costs are reduced by eliminating the costs of hauling milled materials away from the site and then hauling new base material back to the site. Then, by adding asphalt back into the milled material along with water in the mixing process, you uniformly coat the material that is then compacted for for a more stable pavement base platform. The improved stability results from the CIR train acting as proof rolling, highlighting weak areas which then can be repaired before placing the WMA overlay. The end result is superior ride numbers on the finished road surface and a better performing road structure with an extended life.”
The end result for the Sauk County Highway Department and the taxpayers of Sauk County is a win-win-win. Sauk County Highway Department achieves a better performing road structure at 25 percent savings over a traditional mill and fill process, D.L. Gasser and parent company Mathy Construction was able to construct the right solution for the right job at the right time, and the taxpayers of Sauk County enjoy a smoother ride for a longer time and at a lower cost than what other construction methods would deliver.