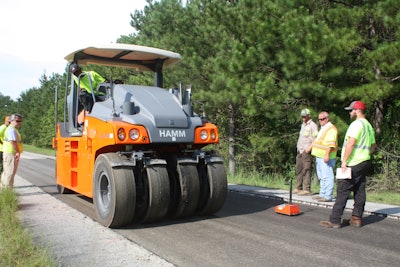
Finding the best intersection between pavement performance and cost is a challenge transportation officials face each and every day. Traditional hot-mix asphalt offers proven performance but at an increasing cost. Cold-recycled asphalt is less expensive, but is lower in strength and typically only used for base material or patching. A new research study at the National Center for Asphalt Technology (NCAT) explores how rejuvenator agents may improve the performance of cold-recycled asphalt, making it suitable for use on low-volume roads when topped with a thin hot-mix overlay. (NCAT has also conducted extensive research with cold-recycled mixes on high-traffic volume roads, but those high-performing experiments required thicker hot-mix asphalt overlays.)
Dr. Benjamin F. Bowers, P.E., assistant professor at Auburn University’s Department of Civil and Environmental Engineering, received cores of cold-recycled asphalt with a rejuvenator from a colleague and found the materials set up between a traditional hot-mix asphalt and a typical cold-recycled asphalt. Bowers and Dr. R. Buzz Powell, P.E., serve as lead investigators for the research.
“We thought there could be a real opportunity here,” Bowers says, noting that the mix uses sustainable materials and is produced at ambient temperatures, which lowers greenhouse gas emissions. It also costs significantly less than traditional hot-mix asphalt, making it a budget-friendly alternative for local transportation officials when paired with a thin hot-mix asphalt overlay.
A Design for Proper Usage
Keeping in mind the most likely uses for such a pavement/thin overlay combination - county roads, neighborhood streets, and subdivisions - the NCAT team decided to test cold-mixes with asphalt rejuvenator products on the test track’s off-ramp, which they felt would offer a good simulation of low-volume roads.
One of the early challenges was to develop a design method. Manufacturers recommended a dosage rate for their products. The team closely followed current cold-recycling design methods, but modified them to account for the rejuvenator. Their design was then held to the same minimum requirements to pass as a typical emulsion recycling mix. “That was groundbreaking,” Bowers says.
Three control sections, one hot-mix base, one foamed cold-recycle base, and one emulsified cold-recycle base, were put in place, followed by three different products, a straight rejuvenator, an emulsion-like rejuvenator, and an emulsion with rejuvenator - Delta S, which is a plant-based additive developed by the team at the Lowell, Mass.-based Warner Babcock Institute for Green Chemistry.
Pavement Restorations, Inc., from Milan, Tenn., is hosting the off-ramp test section dosed the Delta S asphalt rejuvenator. With its portable pugmill plant on site to manufacture that pavement, it volunteered to mix several of the rejuvenators. A paver then laid down each of the six 100-foot sections. All sections were then topped with a one-inch hot-mix thin lift. The off-ramp appears to be one continuous pavement, which was a strategic decision to eliminate stops and starts in the joints; but each section is marked using GPS coordinates and other measurements.
“We like to say that we operate a little bit inverted from the real world. We will prep for four hours and pave for 40 minutes, whereas the real world might prep for 40 minutes and pave for 12 hours,” says Jason Nelson, NCAT’s test track manager. “When we build things on the test track, we try to build them as perfectly as humanly possible unless the sponsor asks us to do it differently.”
He explains that the pugmill requires minimal startup time and is easier to transport than many mobile asphalt plants, making it the likely system of choice for local transportation officials who might eventually use the cold-recycle pavements being tested.
Put to the Test
On the main test track, NCAT typically runs trucks 16 hours a day in two shifts. It puts the equivalent of 10 million single axle loads on the pavement during a three-year test cycle, with most of those going down in about two years. Based on the operation’s schedule, Nelson estimates that the ramp traffic experiences 1.9 percent of that traffic.
With the test sections now complete, Bowers says NCAT will perform a series of evaluations. In addition to weekly visual monitoring, an automated distress detection vehicle drives the track and ramp once a week. Three times a month, a falling weight deflectometer is used to detect physical properties of the pavements. “We’ll be able to monitor stiffness changes, cracking, rutting, roughness, and any of those changes that occur over time,” he explains. “We get lots of data points over a two-year period to watch the changes.”
Nelson sends out weekly performance reports, and cracking data is collected once per month. He explains that while weekly testing may seem quite frequent, it’s necessary because the center puts a hundred thousand ESALs (equivalent single-axle loadings) on the main track every week - a degree of acceleration that is five to 10 times faster than what happens to roads in the real world.
“With that tight data density, you can actually start to see changes before they happen, so we can see things like smoothness or texture that may be indicators of something about to happen weeks or months before anything actually shows up visually on the pavement,” he says.
In addition to testing taking place on the track ramp itself, Bowers is running parallel testing in the laboratory. He collected materials and remixed them to create samples identical to the field study and is running tests in the lab. These tests will be used to help with the design process and quality control as well as to predict performance. “We are really building the laboratory side of this as well in real time as we are getting field performance data,” he says. “Hopefully, those things line up in a way that makes sense.”
At the end of the day, the goal is to create recommendations that can be implemented in the field. “It’s great to do research and learn things,” Nelson says, “but if it’s not something our sponsors can put into use in a relatively short time frame and save them money, it’s not as valuable as it needs to be.”
Bowers hopes to be able to show counties, municipalities, and state DOTs how the rejuvenators can be used in the appropriate settings to achieve better pavement performance at a lower cost. “I think there’s an urgent need to provide these folks with the tools they need to make their community better,” he notes. “We want them to have more tools in their toolbox.”
Therese Dunphy is an award-winning journalist who has covered the construction materials industry for more than 30 years.