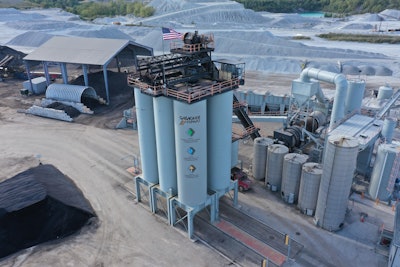
Asphalt plant owners and producers aren't always known for being innovators. The successful companies though, the ones that stand the test of time, know that in order to grow, you have to lead.
Gallagher Asphalt, headquartered in Thornton, Il, is celebrating 94 years in business due to their dedication to their customers and because they have been willing to lead the industry in innovation and change, when and where that change was needed.
"We never want to risk staying the same if there's something we can be doing to be better," Dan Gallagher, president of Gallagher Asphalt says. "We encourage our employees to find ways to do their jobs more efficiently and then act on their suggestions very quickly if it's something we think can create change."
This top down initiative to drive innovation and continuous improvement is what allows Gallagher to thrive in the very competitive Chicago market. The company owns and operates three asphalt plants in the area and offers construction and paving services throughout Chicagoland..
Going Digital Increases Productivity
Maintenance operations are the heart of your business and need to be properly managed to make sure your equipment and crews are able to continue the work that needs to be done without delay. Many companies use paper forms to document when a piece of equipment is in need of repairs, but Gallagher found this method was causing too many delays and sought a more streamlined process to keep their equipment working.
"Manual forms created a long paper trail and it would take us up to three days sometimes to find out if a repair was needed," Brian Ludke, Gallagher shop foreman says. "One of our employees took the initiative to create a QR code in conjunction with an Wufoo online custom form builder which allows all our equipment operators to conduct a comprehensive equipment inspection in the field by simply scanning the code with their phone.”
Employees can enter all the details of the equipment condition including attaching pictures of any problems. As soon as they complete the form any faulty conditions noted, including photos are communicated immediately to the shop.
Not only does this streamline the process of maintenance, but it also improves productivity. Mechanics can easily make one trip to a jobsite prepared with the proper parts to tackle a problem, instead of making several trips.
"This was a game-changer for our mechanics," Ludke says. "The in-app checkpoints for each machine make it simple and efficient for problems to be reported and inspections are completed regularly because the process is much easier for operators to follow. This keeps us up to date on any problems that they might be seeing so we can address them before they become critical issues."
Gallagher also used the barcode feature for their warehouse operations as well for crews ordering needed supplies. Workers in the field can scan a different QR code and order shovels, spray paint, safety vests, etc. and have it waiting for them when they are next in the yard or have it placed in a designated crew truck the next morning. This cuts down time wasted in line waiting for someone to gather the supplies at the storeroom.
"It's all about visibility and transparency," Don Gallagher, IT manager for the company says. "We are working towards transparency across all functions of our operations and this is one way we're accomplishing that. The impressive thing is an employee had this idea at 2 p.m. on a Wednesday and 24-hours later it was operational."
Operational Control Improves Efficiency
This "culture of innovation" can be seen in many other functions of the business, but is perhaps most on display in the company's “Command Center.” If you've ever been inside a dispatch room for an asphalt plant, you know it can be a bit of chaos. Gallagher partnered with XBE three years ago to help better manage their operations.
"We have seen everything from job start times being delayed due to preventable issues, a surplus of trucks on the job and forecasted schedules which asphalt plants couldn’t meet the demand if we had run them with everyone operating in their department silos," Will Gallagher, vice president of construction at Gallagher Asphalt says. "We were looking for ways to streamline our communication and prevent problems before they happen. This makes our operations run much smoother in real time and gives more time back to our staff to think at a more strategic level."
The XBE system gives all stakeholders on the job or at the plant access to real time information they need to properly manage our operations in a cloud-based platform that can be seen 24/7.
"The system visually documents what was once disparate information and puts it all in one place where everyone can see the most current schedule," Will says. "We know what work we have in the coming weeks and what resources are needed across all jobs and aggregate it at a high level for long term planning.. We can see projected vs. actual performance and the system will forecast how the remainder of the day will trend if we continue operating at the current pace. We can automatically forecast cycle times from the plant based on prior performance. We know all the locations of our drivers vs. the location of the paver and can see the time the truck spent at the plant and the time on the job.
“We used to have many opinions of what can or can’t be done. Now there’s hard data to prove those theories and that helps tighten the variance of the daily unknowns. We retrained our team to think differently about planning their jobs and adjusting their plans more frequently when new information is given. This has provided significant pick-up to the bottom line."
Visibility and efficiency are great, but XBE has also taken some of the experience needed for the operations out of the equation.
"Generationally, the seasoned veterans know exactly how many trucks you need and what risks you may run into when the jobs are actually running," Will says. "This program better helps the younger generation catch on to the industry faster. You don't necessarily need 12 years of experience to plan the job any more. You can schedule it in great detail and the system will optimize based on the inputs. At the end of day, a lot of the planning is just math."
The company also uses XBE for their Yard 2.0 operations to control trucks coming in and out.
"Data from XBE flows autonomously to the trucks to not only maximize loading of the truck, but also for e-ticketing," Will says. "We no longer need to have a dedicated person at each plant but instead can use RFID tags to recognize them. We are also working to develop license plate recognition to identify the truck when it comes into the yard."
Know When to Upgrade
The latest change Gallagher has made was a complete plant blending control upgrade at their 600 tph Thornton plant in 2020. Their old blending control was 15 years old and had some components that were no longer supported. Instead of simply replacing components of their existing system, they decided to completely overhaul their controls.
"Our plant is 22 years old and the old WEM controls worked in conjunction with push button control panels and instrument gauges which were suffering nuisance failures after all those years," Jim Trost, executive vice president at Gallagher says, "After a lot of discussions with our plant team and reviewing various supplier quotations, we decided to upgrade to a total control system that eliminated all the buttons and gauges and moved the operator interface for all functions to the PC.
“We chose WEM based on feedback from other asphalt industry total control system users we visited and WEM’s ability to adapt and customize the things that we wanted as part of the new system,” Trost continues. “WEM came out to our site and worked with our team to discuss all the details of what we wanted to accomplish and together we were able to create a system that was right for our plant”.
Initially, the Gallagher plant operators were reluctant to move from a panel system to the integrated controls, but once they saw how the system could work, they understood how it would make their job easier.
"You can see the discomfort in the plant operator's eyes when you tell them what they’ve worked with for years is going to go away for something new," Trost says. "Once we discussed the benefits of the total controls at length and got them involved, they stepped up and took the lead on working with WEM to get the most we could out of the new controls. I’m very proud of the job our team did on this project, these guys go above and beyond and take pride in everything they do."
Trost adds that starts are a lot easier and with all electric ac tanks. The valves open as they need to when you switch the mix over
"It's just one button to get it all switched over,” Trost says. “It’s much easier now."
WEM Analytics also helped sell the new system to Gallagher.
"We are such a data-driven company that the analytics option WEM was offering was a huge incentive," Trost says. "The advanced report package displays various real-time operational dashboards and that helps us know what's happening at the plant so we can make better business decisions."
The Gallagher team pulled the first wire on the old system in December of 2020 and the plant was ready to make mix the following March when the weather allowed. This included a total renovation of the entire control room in addition to the controls upgrade. The plant can produce over 600-tph and uses innovations like camera systems at load-out for safety and a MAXAM Transporter bin top conveying system to ensure the mix is being transferred to silos as efficiently as possible.
When the transporter system was installed in 2015, it was one of only two in the country and eliminated four existing 600-tph transfer conveyors, four diverter gates, and five silo batchers. This change alone added up to a $20,000 annual maintenance savings and about $14,000 per year in electrical savings.
Start Small the go "All In"
Making major upgrades to your facilities to stay up to date with technology and improve operations is one thing, but don't be afraid to start small. Even a small step forward is better than staying still.
"The small things add up," Trost says. "Our QC manager came up with the idea to use iPads and shared OneNote software with test report forms in our QC labs to document all test results. This allows us to keep everyone up to date in real-time and that's a little simple thing that didn't take a lot to get done and it's paid dividends to our operations by dramatically improving communications for our multi-site operation.”
Once you start, don't be afraid to continue trying new things and go "all in" on innovating.
"When we first started out, we dipped our toes into certain technologies instead of making a commitment because we wanted to make sure it was going to work for the company," Will says. "A lot of systems we have purchased didn't work out for us because we didn't lean in to them and leverage them to their fullest potential and we learned from that. We came out better from it and that comes from leadership and trickles all the way down.”
The team at Gallagher knows that listening to their people and changing to help them accomplish their tasks easier, from the bottom up, will continue to help them thrive.
"As a company, we are never satisfied with what currently exists, we are always looking for who’s working on the next great thing and if we can't find someone doing it, we will build it ourselves," Will says. "The Chicago area where we work is probably one of the most competitive markets in the U.S. and we need to do everything possible to stay cutting edge and trim costs as much as possible to remain competitive. We continue to innovate to not only keep what we have today but to build a culture of excellence for the future generations, not just at Gallagher but within the Asphalt industry."