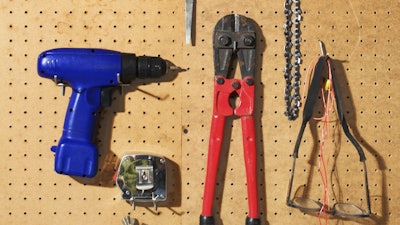
In a previous article concerning the financial impact to contractors when their workers average 90 minutes per day of “looking for stuff,” we identified several techniques that can help reduce if not eliminate wasted time spent searching for all kinds of…well, stuff!
The first technique was focusing on the need to organize your yard, tool room, shop, jobsite gangbox, and even your trucks. I presented a tool called the “5-S Map” that was part of the Japanese system for organizing and cleanliness.
The second technique was called the Job Information Meeting (JIM), a critical pre-job meeting involving at least your job leaders but could include your entire crew. By following a suggested agenda the JIM increases the communication and understanding as to what is expected on the job, where items will be kept, what the flow of work will be, etc.
Now, let’s move ahead to a few more techniques that can have a financial impact on your company’s production and profitability.
Develop Job Set-up Processes
To develop Job Set-up Processes (J-SUPs) is to pave the way to greater clarity and faster starts out of your construction “blocks.” While the JIM is a communication meeting about the project, the J-SUP is the more formal standard operating processes, often called SOPs, that indicate how the work will be organized and the jobsite managed.
There is a right and wrong way, a better way, to drive greater efficiency, productivity and a lot less “looking for stuff.” The J-SUP records the actual steps that will be followed to set up equipment and tools at the jobsite. This is based on location and space requirements at play. Consider a brief example below that might better illustrate the J-SUP.
Jobsite set-up
- Upon arrival the actual parking of vehicles will be done in a safe manner and order.
- A designated area will be designated to allow for lining out needed tools and components.
- Safety barricades and/or tape will be applied clearly designating the area where such equipment, tools and components will be stored during the work day.
- Needed tools for the day will be lined out and placed for easy and safe handling.
- Any item removed from jobsite storage area will be properly returned to exact initial placement.
It is critical that employees know exactly where their tools, components, etc., will be located. Such knowledge reduces the amount of time spent looking for the items, thus increasing the amount of work that is actually completed.
Does this technique appear to be “overkill”? Consider how much time your workers might spend looking for that hand saw, trowel, spray tip, kerosene can, etc. Heck, I’ve witnessed workers searching for the scissor lift on the jobsite, and it was still strapped down on the trailer. Don’t overlook turning each significant work process into a usable and documented process. It can save your crew time as well as serve as a great training tool for new workers.
Develop check sheets for inventory management
A contributing factor to workers “looking for stuff” is often not knowing exactly what is in stock and what is not. It is extremely critical that before every truck leaves your yard that everything that is to be used on the job is accounted for and placed on the vehicles. One tool to ensure that this is completed consistently is to create a check sheet for your daily work needs.
This is much easier to create than you might think. First, record every possible tool, equipment, component that could be used on your jobsites on a form. This becomes your template. Then, as part of the job file the estimator, project manager or foreman customizes this inventory checklist by highlighting or bolding each item on the list that is to be used for the specific job. Quantities can be added at this point if there is to be more than one of any item that is to be taken to the job.
Then, just to the left of each listed item, it is important to allow space to check off the item. This checking off of items is to be done by the crew responsible for the specific job. The crew foreman, or a crew member, then receives a copy of the inventory checklist — identified by the job number and customer name — and then makes sure that each item highlighted or in bold print is placed on the truck. If there is any item missing from the tool room or yard then crew member or foreman communicates this to the senior leader. Some contractors have even provided a document to complete to display what is missing or broken so that replacement or maintenance can be exercised.
The crew that leaves confident that every piece of needed equipment, tool or component is on their vehicle will spend less time looking for those items and more time being productive. Not incorporating some form of inventory control simply sets up our workers to question whether they have all of the needed resources. In other words, “Let’s just see if we can find it once we get to the jobsite.” Not a good solution!
Develop the Next Week Look Ahead (NWLA)
The Next Week Look Ahead is a great planning tool that every crew should never be without. Intended to be completed on a Friday for the “next week,” the NWLA identifies what work will be done for the “next” Monday through Friday. But it also should capture what the needed resources will be, what labor needs will be used each day, and what material needs there will be. Additionally, it is always good to identify any contacts that might need to be made as it relates to the job including other contractors, suppliers, city inspectors, owners, etc.
Some model of the NWLA exists in many progressive and larger construction organizations. In fact, contractors completing large projects might use a two-, three-, even four-week look ahead. No matter the time involved, the same components of identification should be incorporated.
Now, the significance to integrating a NWLA into your construction company is that workers begin to see what the daily requirements are. They become more aware of what is needed and then begin to see what resources will be needed. Such an effort can then be stretched to recognize the need to have such resources available and easily accessible. This again can save time looking for the items.
View a cut away version of a simple one-week look ahead is provided for you below.
Require daily crew huddles (AM and PM)
The final technique that we’ll address is a verbal technique that can not only get your crew started on the right track each morning but can also ensure that each day is brought to a clear end, serving as a set-up for the following day.
The crew huddle is designed to be conducted at the jobsite. Led by the crew foreman, the morning (AM) huddle is designed to discuss the needs of the day, reminders of safety, and basically lining out each worker so that she starts clear and with direction.
The AM huddle allows the crew foreman to point to areas on the site that the crew needs to be aware of or reminded as to what needs to be done, by whom and with what resources. It is also a great chance for the crew members to raise questions or concerns about the day. Likewise, this AM huddle affords the crew foreman the chance to remind his individual members about any “stuff” that needs to be used, where it is to be found or kept, and how it is to be returned.
The PM huddle, also led by the crew foreman, allows the crew to come together at the end of the work day to discuss how the day went, did they meet their goals, why or why not, and what might be done now that will make the next day’s efforts get off on a great start.
The PM huddle also allows the crew foreman to ask about resources, check to make sure the crew returned all tools and equipment to the correct location either at the site or on the truck. The PM huddle also enables crew members to alert the crew foreman if any tool needs replacing or a piece of equipment is in need of maintenance.
Consider an example of the agenda that might be addressed for both the AM and PM Huddle.
The crew huddle is the crew’s opportunity to discuss important items but also a time to make sure they are working on the appropriate tasks and performing them to a level that is productive. Such consistency of meetings requires no more than one to three minutes of clarification for each worker so that there is no doubt as to purpose, strategy and clarity about what to do and where resources are to be kept.
In the battle to reduce the amount of time your workers spend “looking for stuff” it is critical that you, as a leader, buy into a few final thoughts:
- Admit that your workers do spend some time “looking for stuff.”
- Recognize that such waste can be reduced, perhaps even eliminated on occasion.
- Be willing to utilize some of the techniques presented in this two-part article and enforce their consistent use.
- Recognize and reward your workers when they increase their performance and your profitability — proof that they are spending less time “looking for stuff!”
Take the battle to reduce the cost associated with having your workers less organized and scripted out. You can do this, and when you do you will see an incredible jump in productivity, not to mention even better morale from those who have grown weary….”Looking for stuff”!
May you and your workers find what they need…the first time!