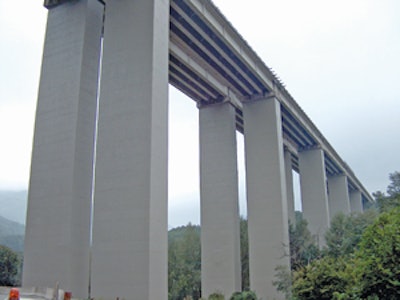
Every year, incomplete concrete repairs and insufficient corrosion protection cost building owners throughout the United States considerable money and time. A simple, yet often overlooked, "fifth step" of concrete repair has proven successful worldwide in ensuring the integrity and durability of concrete repairs — while significantly lowering overall lifecycle costs.
It is estimated there is more than 9 billion cu. yds. of "in-place" concrete in the United States, most of which is more than 20 years old. The use of concrete in construction has continued to grow rapidly, from approximately 220 million cu. yds. in 1990 to 400 million cu. yds. in 2004. This significant quantity of concrete and strong growth rate of concrete use in construction translates into a U.S. repair market of more than $18 billion (USD) per year.
Consult an engineer
These statistics indicate that the typical repair involving deteriorated concrete and corrosion of reinforcing rebar will become more frequent. Before defining a specific repair method, it is necessary to consult an engineer with the appropriate expertise for an assessment of the key dynamics behind the deteriorating concrete. The engineer examines the extent of structural damage, along with a determination of the cause, in order to design a material repair system that will ensure integrity and durability of the structure.
There remains, however, a lack of a solid understanding within the concrete industry as to the best method to address concrete deterioration. Some currently used repair methods — whether topically applied or introduced into repair materials — have yielded inconsistent results and compromised repair performance. This ultimately results in loss of time, money and credibility for both contractor and engineer, while the building owner ends up with disappointment, frustration and no return on dollars spent.
Factors affecting deterioration of concrete
The dynamics behind concrete deterioration are important to understand as effective repair solutions are considered. Virtually all concrete has at least small micro-cracks. These minute cracks, combined with the natural porosity of concrete, open an avenue for chloride (carried by moisture) to penetrate into the concrete, eventually reaching the rebar. As the rebar corrodes, it expands, "blowing" off the cover of concrete, and accelerating the cycle of deterioration.
The other key factor in concrete deterioration is carbonation. When concrete is first poured, its high alkalinity serves as a passivating barrier, protecting the rebar from corrosion. However, as time goes on and the concrete is exposed to the environment, carbonation takes place, reducing the alkalinity and breaking down the passivating barrier. In time, carbonation will reach the depth of the rebar and corrosion cells will develop.
While chloride penetration and carbonation work closely together to deteriorate concrete, other aspects — such as the quality of the concrete and design of the structure — play a pivotal role. The bottom line: Even if the best available concrete repair mortar is used (i.e., high-density and dimensionally stable), carbonation and chloride penetration are working virtually 24/7 to undermine any repair effort.
A 5-step method to repair and prevent corrosion
What then is the best method known today to address corroding concrete? Short of an "engineered" approach that provides for sacrificial anodic or active cathodic corrosion protection, the basic approach involves the following repair methods as defined by the American Concrete Institute (ACI). As stated earlier, any repair necessitates the involvement of an engineer who examines the structure and supervises material selection, repair methods and repair application.
ACI prescribes the following procedures:
- Remove deteriorated concrete and profile the surface according to specifications of the repair material's manufacturer. This includes the removal of any carbonated or chloride-impregnated concrete.
Note: There are methods available today that will remove chlorides from existing in-place concrete. These methods should be evaluated and considered by building owners and engineers. Such methods may be appropriate depending on the extent of the damage and of the desired repair.
- Clean rebar with an appropriate method to remove all corrosion, and repair appropriately to ensure the integrity of the completed repair.
- Coat the exposed rebar with a high-performance anti-corrosion and bonding agent. To improve bonding of the repair mortar to existing concrete, coat all areas of the repair with the same bonding agent.
- Select an appropriate repair mortar with the required performance and application characteristics.
- While this completes the defined ACI repair method, MAPEI recommends going one critical step further to solidify the repair's longevity by an exponential factor — ultimately decreasing lifecycle costs to the owner. For this fifth step, coat the entire structure — both the original concrete as well as the repaired area — with a cementitious, flexible waterproofing and protective coating.
5th step proves successful
The benefit of cementitious coating for repairs was validated by Chris Atkins, senior materials engineer within the Materials and Corrosion Engineering Section of Mott MacDonald Consulting Engineers, in Altrincham, UK. In a recently published interview in the Journal of Protective Coatings and Linings, Atkins concluded that the application of a polymer-modified cementitious coating at thicknesses over 2 mm (80 mils) is the best method to protect concrete structures in wastewater treatment systems.
An independent study of MAPEI's Mapelastic™, designed to provide a crack-bridging barrier that impedes carbonation and chloride penetration of the concrete, showed effectiveness in halting chloride penetration. The test evaluated two specimens — uncoated concrete, and concrete coated with Mapelastic. In the test environment, both specimens were immersed in a 10 percent solution of sodium chloride (NaCl) for 60 days. According to National Italian UNI 7928 standard test method, analysis of the specimens showed that the uncoated sample exhibited chloride penetration of 35 mm, while the Mapelastic-coated sample had chloride penetration depth of 1 mm.
Todd Miller is the Product Line Manager for MAPEI's Concrete Restoration Systems division. Experienced in product line management, marketing, systems development and customer service, Todd is committed to innovative products and positive customer solutions.
For information on MAPEI products and systems, visit www.mapei.com.