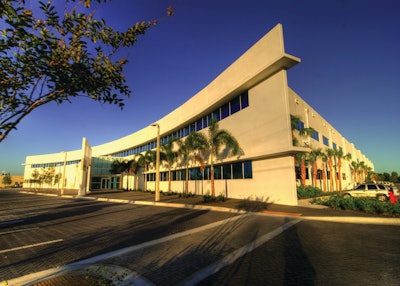
The challenge:
Constructing a tilt-up concrete manufacturing building with an accelerated schedule and jobsite restrictions
The players:
Woodland Construction Company
Permit Engineering Services Inc.
Meadow Burke
White Cap
SpecChem, LLC
The process:
Oxygen Development’s headquarters facility in West Palm Beach, Fla., combines manufacturing with its corporate offices. Because the project had an accelerated schedule and the jobsite was situated directly on a major thoroughfare, requiring that deliveries and equipment not impact traffic, tilt-up was the best choice for construction.
The building has a curved feature on the entire frontage with pavers and landscaping that provide an upscale appearance. A curved cast-in-place concrete stairway in the main entry lobby, along with polished concrete floors, gives the office area an industrial but aesthetically pleasing look. The east side of the building consists of two rows of tilt-up panels. The inside row comprises the main building's bearing wall and is curved inward, originating at the ends of both the north and south walls. The outside curved feature row curves outward, originating from the southeast corner of the main wall and continuing on an outward plain, on a segmented radius. This causes some of the east wall panels to be double thickness with openings and architectural recesses on both sides of the wall.
On this segmented curved wall, there are large recesses on the exterior that have a hammered finish in the tilt-up panels as well as recessed columns to accommodate a continuous ribbon glass window wall. The curved frontage wall of the building also features a cast-in-place eyebrow above the ribbon windows on both the first and the second floors for the full length of the building's elevation, extending through to the tilt-up panel cantilevers on each end.
Oxygen was also required to provide a new covered bus stop shelter along the main road in front of the facility, so one was efficiently designed and erected utilizing tilt-up, including the roof. Despite a very tight schedule, tilt-up enabled the owner to occupy the building on time, and manufacturing began on schedule.
Project Specifics
- Project wall area: 91, 513 sq. ft.
- Project floor area: 221,732 sq. ft.
- Project footprint: 166,869 sq. ft.
- Tallest panel: 45 ft. 1 in.
- Widest panel: 49 ft. 1 in.
- Largest panel: 1,233 sq. ft.
- Heaviest panel: 176,000 lbs.
- Tallest cantilever panel: 12 ft. 6 in.
- Longest spandrel panel: 34 ft. 9 in.