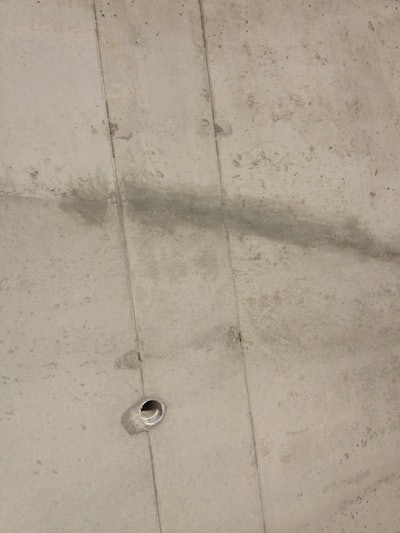
Question: A recent project we were completing was held up when our homeowner ventured to the site to see the concrete work we had just unveiled during stripping of the forms. Across one wall was a visible line we commonly know to be a pour line, but immediately the concern was “my foundation is already cracked,” what can we do to reassure our customer? – Concrete contractor from Indiana
Answer: We will agree that this is a very common inquiry that we receive from the market.
Occasionally the contractor defending their work brings it to our attention and sometimes it is by the customer looking for third party assistance, in either challenging the work or relieving their concern. Regardless of the purpose or direction for the inquiry, the reality is that blemishes and visible record of concrete placement is a natural part of the cast-in-place process, particularly when higher aesthetic standards or specifications are not set for the project.
A Change in Load
The vast majority of the occurrences for these diagonal lines in a cast-in-place are the indication of a change in concrete load during placement. When a contractor is placing concrete in vertical formwork, regardless of the placement mechanism (e.g. concrete pump, conveyor or direct chute), the truck placing the concrete will run dry and a change is made. Concrete trucks traditionally carry between 7 and 10 cubic yards of concrete while an average 3,200 square-foot house foundation requires between 50 and 60 cubic yards of concrete.
Most residential lots have considerable restrictions on the movement of vehicles due to lot lines and other traffic congestion, therefore only one truck at a time is able to deliver its load. When one finishes and moves out, the next moves in and placement resumes.
Depending on the amount of time between starting and stopping, the concrete in the forms has already been vibrated by the crew waiting on the placement to resume. As the new load is placed, the contractor will resume vibrating the fresh concrete but may not extend the vibrators fully between the previous placement and the new concrete. This results in what the industry refers to as a “pour line” or a slight variation of color or texture that may indicate a natural color variation in the concrete, a different rate of compaction or vibration and most likely the difference in hydration stage of the fresh concrete.
Concrete begins hydrating the moment mixing begins of the cementitious particles and water. There are multiple stages or benchmarks for the hydration process that range from mixing to initial set, final set to design strength, etc. The contractor should fully recognize the stages of workability and to make certain that initial set is not reached between placements.
When Cold Joints Appear
If this happens, rather than a “pour line” between concrete placements, a “cold joint” will occur. A cold joint is where the previous placement hardens prior to the receipt of the next placement and the result may be a reduction of the monolithic behavior for the concrete element, in this case a foundation wall.
Professional concrete contractors can easily identify if the concern for a cold joint is present and can plan to remediate the problem should that occur before they start the next placement. However, should a serious concern exist for a cold joint over a pour line, there are non-destructive methods to core and examine the concrete before making the final determination of the best way to proceed.
Wall sections that have cold joints and steel reinforcement are likely to still perform adequately due to the combination of shear transfer across the joint due to the steel reinforcement bars and the coefficient of friction at the rough joint. An engineer may also review the joint if sufficient concern exists.
Check the Guide
ACI 309.2R-98 – Identification and Control of Visible Effects of Consolidation on Formed Concrete Surfaces (American Concrete Institute, www.concrete.org) can be a useful guide to a complete description of the presence of these diagonal lines. From section 2.5 of this document:
“Placing concrete too slowly may allow workability to be lost and can produce layer lines or cold joints due to improper consolidation. Undervibration is far more common than overvibration and may be caused by the following: 4. Failure of the vibrator to penetrate into the preceding layer.”
The question is a good one to start the conversation between contractor and customer on the quality of their wall and the performance issues that the owner will be responsible to maintain. While the diagonal pour line is very infrequently a cause for concern for any issue of performance, especially for walls receiving dampproofing and/or waterproofing treatments, the discussion of the long-term maintenance goals for proper grade and foundation care will lead to decades of proven value and performance.
Want to know more? Contact CFA Managing Director, Jim Baty at 866-232-9255 or by email at [email protected]. The CFA is a national association for professionals with the mission to support the cast-in-place contractor as the voice and recognized authority for the residential concrete industry. ACI 332 is the Residential Concrete committee for the American Concrete Institute and as a code committee is seeking professionals from all aspects of this industry with an interest in participating in the development of expanding and strengthening this concrete code.