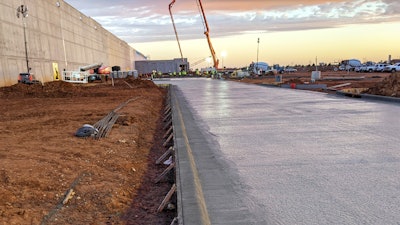
Throughout history, many new processes have come along to improve how people achieve end results. These innovations— even those that eliminate just one step—often lead to dramatic increases in productivity and efficiency. When digital cameras entered the market, they cut out the step of going to the store to develop a roll of film, accelerating the process of viewing family photos. Lawnmowers with bagging functions eliminate the step of raking and bagging grass clippings, leading to considerable time savings.
Now take these concepts and apply them to construction. In an ever-evolving industry, contractors innovate through the equipment they purchase and processes they adopt. When it comes to concrete, monolithic pours are one process that contractors can use to drive efficiency.
Monolithic pours streamline concrete work by pouring curb and gutter simultaneously with flatwork, instead of completing these pours one at a time. If completed with the right equipment and considerations, contractors can reap the benefits without sacrificing quality.
Savings
A traditional pour most often requires curb and gutter work to be poured, finished and cured to outline the pavement area. Then, the crew returns at another time to pour and complete the flatwork. A monolithic pour, or an all-in-one pour, improves efficiency by completing curb and gutter at the same time as flatwork. This process saves a considerable amount of time by completing the entire job with one pour instead of two, boosting productivity and the bottom line.
Driven to continually seek new ways to keep up with ever-growing demand, more contractors are seeing the benefits of monolithic pours, especially for parking lots and streets. Contractors who streamline the most time-consuming aspects, such as hand-shaping curb and gutter, experience the most significant spike in efficiency and often double production. Just as the digital camera created a more productive photo development process, monolithic pours drive up efficiency for contractors.
Walk-behind curbing machines with monolithic kits and battery-operated walk-behind curbing machines are two options that contractors may consider for a more streamlined process of hand-shaping curbs.Curb Roller Manufacturing
Progress
With a good crew, walk-behind curbing machines are capable to maintain the production pace found with a laser screed while eliminating the extreme physical labor and the need for large machinery for curbs. These machines consist of a handle attached to a metal drum that is connected to a hydraulic power source. The single-operator machine reduces the intensive manual labor of shaping curb and gutter while producing a consistent, high-quality result, even for operators with minimal experience. While these machines were originally developed for completing curb and gutter work on traditional pours, most can be modified to adapt them for use during monolithic pours.
Newer entries to this class of equipment incorporate battery power and a design specifically created for monolithic pours. These machines combine the benefits of traditional walk-behind curbing equipment with lightweight portability to quickly move throughout the jobsite. Battery-powered walk-behind curbing machines offer easy maneuverability and transport due to their relatively small size and lack of cords and hoses.
Consider a contractor who was hired to install a large parking lot for a private company. The crew used a laser screed due to the sheer size of the project. They worked during the night to limit traffic interference and were able to pour about 2,000 yards of concrete pavement per night. However, they were only able to shape about 300-400 feet per night by hand. Investment in a battery-powered walk-behind curbing machine doubled that productivity to 700 linear feet per shift.
The equipment options for monolithic pours are often highly versatile and therefore offer an increase in overall return on investment as well as productivity.Curb Roller Manufacturing
Results
Laser screeds and walk-behind curbing machines are ideal for projects such as parking lots with large amounts of flatwork and multiple areas of curb throughout. However, a machine that can shape curb and gutter simultaneously with flatwork can be ideal for certain monolithic pour applications like street construction or replacement. Slipform machines are one of the more efficient solutions if and when the project matches the machine design parameters and there's enough volume of concrete to justify their operation and overhead costs.
Some manufacturers offer custom drum options for hydraulic screeds. These drums can reach up to 16-ft. long and can be designed to match a specific shape, like half of a street, including the curb and gutter. Custom drums replace the pipe on a hydraulic roller screed and use a spinning motion to shape the concrete.
This monolithic pour method is ideal for streets due to the long stretches of pavement that are the same shape. It is especially convenient for replacing existing streets because it allows one lane of traffic to remain open. After the crew completes one side of the street and it’s ready for use, they change the traffic flow to complete the second side. In the past, this was only possible with large, expensive slipform pavers or through manual labor, but a custom drum with a hydraulic screed provides a method to complete the work for a fraction of the cost or time.
One of the key advantages of monolithic pours is that all-around quality of curb and gutter work increases when contractors use the proper equipment for the job.Curb Roller Manufacturing
Quality
A common misconception is that monolithic pours produce low-quality curb work. This may be true if a crew that is primarily focused on flatwork is hand shaping the curb. They may have little experience in curb and gutter work, and they have to apply most of their focus to the flatwork, which is the larger portion of the job.
However, the proper equipment can provide a key advantage and increase-all around quality to a monolithic pour. Replacing manual curb work with one of these mechanized systems makes it easy to achieve consistent, spec matching results, even with an inexperienced crew. The equipment is user friendly and enables contractors to accomplish more with less labor, a key advantage in a difficult employment environment.
Weather
A key consideration when determining whether a monolithic pour is the right solution is the weather. Monolithic pours really shine in tough weather conditions. As seasoned concrete workers know, the weather dictates when and how efficiently they can pour. Dealing with a small pour window becomes less of an issue with a smaller number of pours. With the right equipment, monolithic pours can double or even triple production and help crews maximize the work they can complete before that window closes.
Despite all the advantages, there are some cases where a monolithic pour is not the best solution. These situations will come into play in colder climates. If a job uses asphalt for the pavement, the concrete curb and gutter must be poured separately. Additionally, the monolithic pour method is not ideal if the curb and gutter or flatwork may need to be replaced separately. In colder regions where brine regularly collects in the gutter, the freeze and thaw breaks down the concrete and leads to a shorter life for the curb and gutter than the pavement.
For some monolithic concrete pours, contractors may benefit from using one machine to shape the curb and gutter as well as the flatwork simultaneously. This capability comes in the form of a custom drum with a hydraulic screed.Curb Roller Manufacturing
Demands
Contractors can maximize their investment in concrete equipment by purchasing machines that increase productivity for a variety of applications. Beyond custom drums for monolithic pours, hydraulic screeds also pair with standard pipes to screed flatwork for jobs such as streets and sidewalks. Walk-behind curbing machines have multiple drum options and can also complete curb and gutter for traditional pours. Additionally, battery-powered walk-behind curbing machines effectively complete patch and repair work and complement slipform machines to complete corners and tight radii.
The demands of the construction industry are shifting rapidly. There is a high demand for work, and contractors can capitalize on these opportunities by finding innovative solutions that improve their processes and increase their capacity.
Monolithic pours are not the answer for every concrete project, just as instant cameras and rakes are still used instead of digital cameras and mowers with baggers. But with the right equipment and the right application, a monolithic pour may be what drives an operation to peak efficiency.
This article originally published May 2023, by On-Site magazine.