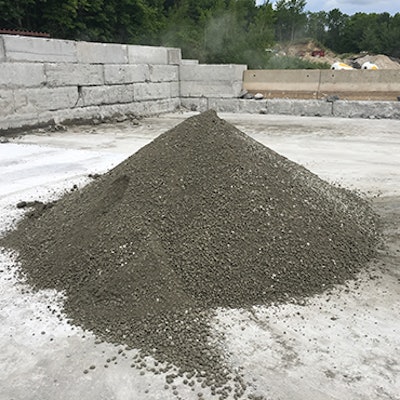
By Angel Abelleira, for GCP Applied Technologies
Concrete is the world’s most used construction material. It is used to construct homes, schools, offices, roads, runways, tunnels and bridges and so much more. However, it has a large carbon footprint, and waste concrete has become a major problem. The National Ready Mix Concrete Association (NRMCA) estimates that in 2017, approximately 350 million cubic yards of concrete was produced in North America, and approximately 12 million yards of that concrete was returned.
The NRMCA estimates that 1 to 5 percent of ready-mix concrete is returned every year. There are two main reasons why such a high percentage of plastic concrete gets returned. First, contractors commonly over order for a project to ensure they have enough concrete and don’t need to order a last-minute partial load. Second, ready-mix concrete can be rejected at the jobsite, typically because it fails to meet the specified slump or plastic air at the point of placement, or is well past its time limit.
What is done with the returned concrete? The decision is complex, as producers must be in compliance with all applicable environmental regulations and specifications. While a logical solution to this problem is to batch new concrete on top of the returned concrete and use it on a new project, until recently, there was no industry standard to guide producers in doing so. The new ASTM C1798/C1798M sets forth the requirements that a producer must comply with to ensure that the final product meets the needs of the prospective buyer. Due to the extensive list of quality and logistic requirements though, only a fraction of returned concrete will be resold. Thus, the majority of returned concrete is made into blocks, crushed to be used as concrete aggregate or road base, discarded in landfills, or discharged into a concrete reclaimer. All of these processes are costly and/or labor intensive.
Today, there is an opportunity to significantly reduce concrete waste and, in some instances, realize additional revenue through a new patent-pending technology. GCP Applied Technologies has developed the CLARENA RC40 admixture, an environmentally-friendly solution to easily recycle and reuse returned concrete. It is a high surface area, non-regulated, non-leachable product that does not require water to recycle the returned concrete. When added to plastic concrete, it turns the concrete into granular material that can be used as a replacement for virgin aggregate in fresh concrete or used as a high-quality road base or compacted fill material.
The technology does not waste any material from the returned concrete, and the process is efficient and green throughout. The end result is recycled aggregate that ready-mix manufacturers can reuse. The technology offers numerous economic and environmental benefits, including:
- Material conservation
- Cost savings
- Reduced concrete in landfills
- Reduced emissions, fuel and energy
Innovative solutions such as the CLARENA RC40 admixture are posed to have significant environmental and economic impacts on the concrete industry.
ACI member Angel Abelleira is a North America product manager for concrete products at GCP Applied Technologies in Cambridge, MA. He has worked for GCP for 32 years, including 12 years in the Cement and Concrete R&D organizations, where he was granted three U.S. patents. He holds a graduate degree in chemistry from Boston College.