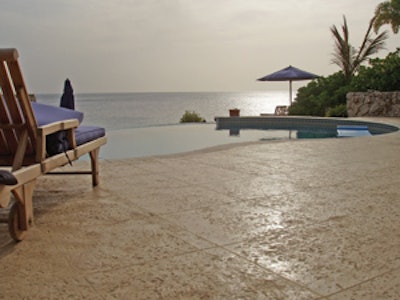
Our first visit to the Caribbean island of Bonaire was back in May 2005. Our friends Scott and Sharon Barlass (full-time residents on Bonaire) invited us down to help stain the floors on their new beachfront home.
I feel compelled to discuss concreting on this 290-sq.-mi. island. What intrigued me was the way the local workers performed their skills with the local materials and tools obtained on the island. I figured I would ask Scott a few questions relative to concreting on Bonaire since he dealt with both the good and bad aspects of concrete construction.
What made you choose decorative concrete virtually throughout your entire home?
There were two factors in our decision to choose decorative concrete. The first was the opportunity to have a unique appearance that was rich and varied. The second was the relative cost difference between decorative concrete and importing tile to the island. We would have had to tile more than 5,000 sq. ft. of surface and the cost would have been more than $50,000. On top of that, there would have been import duties of 30 percent and then shipping costs of $10,000 to $15,000. Also, there is the chance of breaking tile during shipping in the open seas, let alone having to order an additional 20 percent of tile to cover the broken tiles.
How is the labor different from the states?
In the states (Minnesota) we had a lot of concrete at our home. The driveway, pool deck and gazebo area, as well as roughly 2,500 sq. ft. of living space, consisted of concrete. On our project in the states, I recall the concrete supervisor supplied by our concrete contractor not being overly active in orchestrating his team of workers while at the same time doing a poor job of coordinating materials and supplies.
Many of the workers seemed unskilled and had no business being on the construction site in the frame of mind they were in. Some days they showed up and some days they didn't. Not to stereotype, but our experience in dealing with our contractor in the states was not a positive one!
On Bonaire concrete is a way of life. There is very little wood used in construction. Concrete is used on floors, walls and many times (like our home) even the ceilings. The common laborers seem to be inspired in achieving more detailed work such as concrete finishing so they can move up on the pay scales. Any improvement they can make is a great improvement in their lives, which is a major motivator. Skilled concrete finishers on Bonaire make about $11 per hour. A common day laborer earns approximately $3 to $3.50 per hour.
Does the production of concrete installation differ from the states and if so how?
In the states, production seems to be much different because basically the supervisor would call the ready-mix concrete company and it would be delivered in the truck for a quick and easy installation. In Bonaire there is only one ready-mix plant that delivers by truck. Once the truck arrives on the construction site, they won't stand by for long. It is not uncommon for the driver to discharge the load and drive off leaving a reservoir of concrete waiting for its new home.
Most concrete is mixed by hand in a mortar mixer. As far as the raw materials, the cement comes from Venezuela. Much of the aggregate is crushed coral from different parts of the island and has very high salt content. The sand is made by crushing the coral down, and the sand is very coarse and has a high salt content as well. Therefore the workers have to use a large 3- by 4-ft. screen and throw the sand through the screen (their homemade sieve) before mixing. It is doubtful that one mortar mixer load of concrete is the same as the next one. Plastic buckets are used to scoop up material and consistency would not be the same throughout. But they have a good gut instinct for mixing each batch and get very close.
Are you satisfied with the quality of your concrete installations?
Overall I am satisfied with the concrete; however most of the concrete is less than 3 years old and hasn't stood the test of time. I guess like in the states, I still need to keep a close watch on the concreting process. In one instance, I showed up one day and instead of shoveling sand the workers were shoveling dirt into the mix because the contractor was running out of money. The availability of materials has been a big issue with the construction of our home. For example, sand is not plentiful just because we live on an island. Last year for three months there was no sand.
As I mentioned, sand is actually made here by crushing coral rocks. I'm told that as of the first of the year crushing the coral to produce sand will no longer be allowed to protect the environment. This will mean that all sand will have to be imported. The cost of sand is $600 per cubic meter.
We talk about sourcing sands and cements, how about for the workers sourcing finishing tools, edging tools and stamping mats along with general supplies?
There is a local source for purchasing trowels, shovels, wheelbarrows, but anything beyond that — stains, dyes, stamps, etc. — have to be imported from the United States, which takes a minimum of two weeks.
Have high-end decorative concrete finishes hit the island yet?
Here there is very little opportunity for education for advanced concrete science, method or art and very little incentive because there hasn't been a huge market. Most homes are traditional or simplistic, but that will change over times as the opportunity becomes available for education and artistic installation.
What about any language barriers or financial considerations?
These are definitely huge issues, both the language barrier and the financial end of the business. Not many workers speak any language other than Spanish. Needless to say, after three years of construction, my Spanish has improved dramatically.
Financially, U.S companies typically don't accept any non-U.S. credit card. This means that I have to make many of the purchases and then expect reimbursement from the builders or workers.
As you can see, there are many considerations many of us here in the United States simply don't have to even consider when pouring concrete. The more we travel to foreign countries and experience their construction practices and processes, the more I truly realize how fortunate we are to have all of the wonderful resources at our fingertips.
The bottom line is, when we think we have it tough, maybe we should quit our whining and take a moment and realize how good we have it.
Good luck.
Bob Harris is the founder and president of the Decorative Concrete Institute, Douglasville, Ga., which provides hands-on training in architectural concrete. He has personally placed or supervised the placement of more than 3 million sq. ft. of decorative concrete and is the author of a best-selling series of decorative concrete books. For more information, call (877) DCI-8080 or visit www.decorativeconcreteinstitute.com.