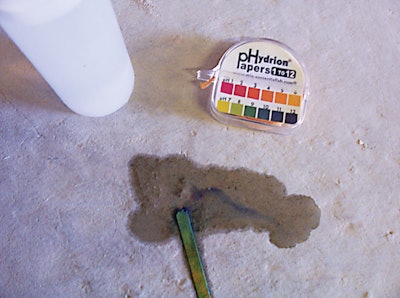
In the summer of 1981 a friend called me to ask if I would be interested in moonlighting to help him install floor sealer for a company in California. Even though I worked 18 hours that day, I decided to take my friend up on his offer. The job started my career in the concrete floor specialties industry.
Back then, our industry was not very scientific: "Coat It! Coat it! Coat It!" was the answer to almost everything. Not much attention was paid to testing or careful engineering of a concrete flooring system to avoid what today are knee-deep liabilities. Shot blasting was not yet prevalent. We used silicon carbide cup stones on shroudless grinders and everything was prepped with a muriatic acid and water mix with no diamond tooling.
The main testing performed on a concrete slab before our work was a visual inspection. If the coatings peeled, we surmised it was from not rinsing the acid properly. White residue meant efflorescence and a possible moisture problem, but was that really it? Or could it be topical deposits caused by hard water or etching?
At the time, water vapor emission tests were done by simply duct taping a square of 6 mil plastic to the slab and checking if it was wet after 24 hours. There was no way of knowing exactly how much water vapor was transferring through the slab. I didn't know what water vapor transmission really was. These tests only concerned concrete coatings and hard surface flooring since concrete polishing was more than a decade from becoming a viable hard surface flooring choice.
Moisture testing and polished concrete
To a company that only engages in concrete polishing, why is moisture testing important? After all, why would you care about moisture? You are not selling products that can peel and delaminate. On the other hand, how many times have you met with a potential customer that is choosing between polished concrete and resinous or vinyl tile? Advanced moisture testing can also be done with ASTM 1869 calcium chloride and humidity probes. Conversely, with a simple PH test kit you can demonstrate that the floor is emitting water vapor and the value engineered choice is polished concrete. If the floor is producing more than 3 pounds of water vapor, which past the parameters that flooring manufactures allow, the litmus paper will turn dark blue at the surface.
If the floor is showing a high moisture problem that also visually indicates an underlying contaminating substance such as sodium sulfate being transmitted from under the slab and deposited on the surface, it is best to do further testing as efflorescence will form on the finished polished concrete. The customer may associate this with the polishing contractor and the reactive chemicals. A slab with more than a 7-pound water vapor emission problem can form visible efflorescence at the surface overnight or over a weekend. Unfortunately treatments and cleaners that dissolve the alkali deposits can also harm the polished concrete surface.
A PH what?
During my 30 years of work in the industry, I can count on one hand the number of specialty floor contractors I encountered with a PH test kit. The test kit contains $12 in litmus paper and a small container of distilled water. I didn't witness someone using a PH test on a concrete floor until acid stains were prevalent. This was the only way to know if the acid in the stain was properly neutralized for the installation of the sealer.
Quite simply, a PH test is a highly revealing check and can be completed in five minutes. If PH at the surface is high, (10 or higher) it can indicate a water vapor emission problem. Concrete dyes, which are powders that are homogenized into a dissipating liquid for delivery and penetration, are pushed to the surface by high water vapor emissions. This causes the dye to loosen and lift from the surface. When it comes to acid stains the opposite may be true. These chemicals depend on a high PH because the colors are produced by the reaction of the metallic salts in the acid stain and the hydrated lime, or calcium hydroxide, which is a by-product of cement hydration in the concrete. In either case, the key is to know what the conditions are before work starts.
If the test is low (6 or less), it can indicate early carbonization of the slab, another potential problem. Carbonization occurs when carbon dioxide from finishing equipment or heater exhaust or other sources mixes with bleed water at the time of concrete placement. The carbonic acid will also push dye to the surface and cause a densifier to react improperly or not react at all. Unfortunately, carbonization of a slab can only be confirmed with core testing.
"Normal" PH for a typical slab surface should be 8 or 9. "Normal" is slight carbonization at the surface caused atmospheric carbon dioxide reacting with alkalis in the concrete surface. Typically this only encompasses the thin layer at the slab surface. If 1/16 of inch is removed from the surface, readings should be a higher 10-12 PH.
Be proactive
As good contractors take the opportunity to perform slab testing before polishing or staining concrete, they will gain the experience and understanding necessary to protect both the contractor's and the customer's best interest. Although these simple tests won't tell you everything and more advanced testing may be needed, they will give a clue that there may be trouble on the horizon. At a minimum, if the PH test indicates there are problems, a manufacturer's technical representative should be involved.
Put another way, a contractor who performs these simple tests is proactive. On the other hand, the contractor that does not will end up being reactive. The reactive contractor's concrete dye doesn't take and the contractor blames it on the manufacturer. The reactive contractor's diamond tooling wears out prematurely and the contractor blames it on the tooling manufacturer. The reactive contractor ends up guessing and hurts the industry, not to mention incurs extra costs. It is easy to get caught up in an easy sale and side-step testing. Russian Roulette anyone?
When I do the simple tests in front of the customer, I am qualifying myself as a careful expert. Taking it one step further, I perform a Mohs' scale of hardness test. This aids in diamond matrix choice and proper engineering of hardening and densifying of the slab. Qualifying yourself as an expert is a very important part of a sale and will also put a customer at ease, giving them confidence that you know what you are doing. After being involved in hundreds of projects, I have yet to be involved on a project that did not include some degree of customer education.
Testing and polishing early
In new construction, polishing when the slab is relatively young helps push the schedule. We installed one 10 day polish with zero problems during winter months. The densifier reacted properly and the polish was even and attractive. We did wait past 28 days to install the stain protector and 45 days to install the joint sealant. At the same time, we performed a polishing job at a similar structure down the road to much different results – the slab appears to have carbonized and more extensive testing was required.
The twist is, of course, the concrete is softer and easier to polish at the 10 day mark, but any PH testing is not entirely accurate. A full 28 day cure is required to get a more accurate indication of the condition of the slab. A PH test on a relatively new slab may not be a trustworthy indicator of potential success unless performed after a significant amount of cure time.
In our case, there were no indicators that carbonization occurred, including PH test results. We did subsequently learn that propane heaters were used to heat the building during construction. Ultimately, it is up to a proactive contractor to educate the customer and draw on past experience to make the informed decisions.
Get a test kit
The total investment for a test kit can be less than the cost of two gallons of concrete dye. This industry relies on chemical reactions in concrete, concrete that most contractors have little to do with designing, much less placing or finishing. Pre-testing is not a panacea, but it provides a proactive contractor with information that helps to ensure a successful project.