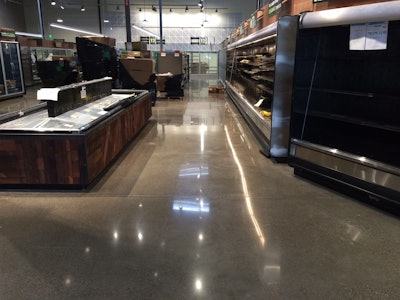
In part one, we discussed why proper maintenance is important to long term customer satisfaction, basic housekeeping guidelines and one of the three main concerns of maintenance: the abradability of concrete and how to address it. In this article, we will cover the remaining two main concerns: porosity and reactivity, as well as the importance of matching a floor to its owner expectations. This includes maintenance capabilities before work begins – the floor's risk profile and the floor owner's aesthetic requirements.
Concrete is Porous
Concrete looks like a sponge under magnification. The surface is riddled with pores - capillaries and micro-fissures that are access channels for oil- and water-based liquids to infiltrate into the interior of the slab, causing discoloration and staining. Although the process of polishing does mechanically “tighten” the floor and the application of a densifier helps to seal off theses access channels, further effort is required to address this issue.
How to Address Porosity
During Installation: The application of a stain protector as a final step in the application process will help to prevent oils and water from infiltrating into the concrete slab, keeping the discoloring substance on the surface until cleanup and removal of the liquid is possible. There are two main categories of stain protectors: guards, which fill in tops of the access channels and form a thin membrane with acrylic polymers, and penetrating stain protectors, which seal off the interior of the access channels with a build-up of silicone.
During On-Going Maintenance: Timely cleanup of any staining substance is critical, even when a stain protector that has its integrity intact is present. The exact window for acceptable surface dwell time prior to cleanup will vary, based on the floor itself as well as the characteristics of the liquid spilled including viscosity and surface tension. However, a good rule of thumb is to cleanup any spill as soon as possible. Reapplying the stain protector is also an important factor in stain prevention. Both guard and penetrating type stain protectors will lose integrity and efficacy with time, and manufacturer's recommended reapplication schedules should be followed.
Remediating Existing Issues: Once a discoloring or staining substance has penetrated into the concrete, it can be difficult to remove. The two most common methods of treatment, which can be used in conjunction with each other, are to draw out or remove the staining substance with a poultice, or to treat the stain in place with a chemical reaction. A poultice is a compact of absorbent solids moistened with a solvent that will wick or draw a staining liquid up and out of the interior of the concrete. There are commercially available poultices on the market or it can be made, typically using diatomaceous earth or trisodium phospate (TSP) as the absorbent base. Stains can also be treated in situations by introducing a treatment that will chemically break the substance down. Depending on the composition of the staining substance, an oxidizer or enzymatic treatment can be appropriate.
Concrete is Reactive
The cement paste component of concrete has a large amount of calcium in it, making it susceptible to reactions with any substance that is acidic (less than 7pH) or alkiline (greater than 7pH) on the pH scale. This is of particular concern with highly mechanically refined or polished concrete, as these reactions can chemically profile the area where they interact with the concrete, leaving a less reflective surface or an etch as a result. Further complicating this aspect of maintaining polished concrete, is that reactive substances can not only chemically profile the concrete, they can also create byproducts from the reaction that can discolor the floor. An example being acetic acid, found in vinegar, reacting with the calcium component of concrete and leaving deposits of calcium acetate, which is a white crystal embedded in the matrix of the concrete.
How to Address Reactivity
During Installation: The application of a stain protector as the final step in the polishing process can help to prevent or minimize chemical etching after the floor is put into use. A guard will create a protective membrane between the surface of the concrete and reactive substances that the floor might encounter. However, to be effective the guard must be maintained through reapplication, to ensure its integrity. The acrylic polymers used in most guards are also not terribly chemically resistant and if an etching substance contacts the floor in enough quantity for enough time, the etching substance can eat through the protective membrane of the guard and get to the underlying concrete, where it can deleteriously interact with the floor. A penetrating stain protector will not typically create a similar protective membrane, as they are by nature subsurface. However, by sealing off the access channels into the interior of the concrete, a penetrator can suspend the etching substance on the surface i.e. limiting the damage to that of a superficial stain, making remediation much easier.
During On-Going Maintenance: The most effective way to deal with etching is prevention – keeping etching substances from interacting with the floor at all and timely cleanup to limit the concrete's exposure to them. For floors protected with a guard, maintaining the integrity of that guard via reapplication of it “as needed” will keep the protection offered at its most effective. For floors protected with a penetrating stain protector, consider using specialty abrasive cleaning pads on the cleaning equipment. This will re-refine areas where superficial etching has taken place, remediating the etching as part of the regular maintenance schedule.
Remediating Existing Issues: Once etching has occurred, excepting the ones that can be remediated during the routine maintenance procedures as described above, it will be necessary to periodically address them. For floors that are protected with a guard product, it is often best to strip guard from the area surrounding the etch being fixed, as many guards will leave a visible cut line where a new application meets existing product. Consequently, stripping the guard from control joint to control joint will allow you to reapply in a seamless fashion once the etch has been repaired. Once the guard has been removed, or as a first step on an impregnated floor, abrasives will need to be used to re-refine the area that has been etched. To do this, begin with the least aggressive abrasive that will eliminate the etch and work progressively finer, with each step being used in a slightly larger area than the previous to feather in and blend the repair into the surrounding floor. To remove discoloring byproducts that may have been introduced during the reaction, such as the calcium acetate example above, the application of an oxidizer maybe required. Once the area effected by the etch is brought up to and blended into the level of refinement of the surrounding floor, the stain protector should be reapplied.
Matching a Floor Owner With the Correct System
Pairing the floor owner with a polished concrete system that meets their aesthetic requirements and fits with their maintenance capabilities, while fully informing the owner of what the maintenance requirements of that system will be, is critical to the floor owner's long-term satisfaction, but is rarely done. Due to each floor owner's capability and tolerance for maintenance, their aesthetic requirements, and their floor's unique traffic pattern, it is important to be able to tailor the floor as installed to meet these factors and avoid the temptation to provide a cookie cutter “one size fits all” approach. To illustrate the concept, we will consider two different floors: A. a clothing retailer with very high aesthetic requirements, light foot traffic, medium tolerance for maintenance cost, and limited capability to provide their own maintenance and B. an industrial facility with low aesthetic requirements, frequent heavy wheeled traffic, low tolerance for maintenance cost, and janitorial equipment and staff on site. For situation A., a highly refined polish level (3000 grit+) with a guard stain protector will fulfill the high aesthetic requirements and a maintenance system incorporating minimum input from in-house staff (daily dust mopping, weekly spot mopping) and quarterly periodic maintenance from an outside vendor who would remediate stains, UHS burnish with a high grit diamond impregnated pad and reapply guard during the service would be appropriate. For situation B., a floor refined to 400 grit and protected with a penetrating stain protector and a maintenance system that has in-house personnel auto scrubbing the floor with appropriate cleaner and pads weekly and bi-annual reapplication of the impregnating stain protector would fit the bill.
It can take some creativity and forethought to make the correct match of floor system with owner requirements and capabilities, and it can be difficult to ensure that the floor owner understands what the appropriate maintenance system for the floor provided requires. However, the payoff is customers that are satisfied long-term and the reputation and recurring business that stems from that.
Proper maintenance of polished concrete does not have to be expensive or difficult but it does need to be addressed and implemented, and the sooner in the process that it is addressed the better, as a neglected floor will eventually turn into a failed floor and lead to unhappy floor owners.
Ed.Note: Part 1 of this series appeared in the December 2017 issue of Concrete Contractor, pg. 74. The article can also be found online at https://www.forconstructionpros.com/concrete/decorative/polishing-materials-equipment/article/20982147/polished-concrete-maintenance.
Jon Hughel has been in the polished concrete industry for 11+ years, working for a major equipment and tooling manufacturer, a chemical producer and a national distributor. He has focused on the installation process from the contractor side as well as specializing on the maintenance of polished concrete and other hard surfaces, working with floor owners and building service contractors.