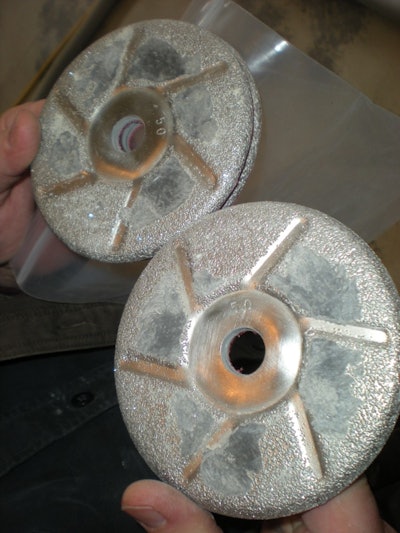
Some floor coatings are very durable and guaranteed to last for years and years of daily use. When the job is to pull up a perfectly good coating, I have heard many horrific stories of costly problems in performing this seemingly simple task. Like many experienced contractors, I too have learned from the school of hard knocks in coating removal, many times it is a very expensive school to attend.
There are lots of misunderstandings and myths regarding the generic all-encompassing term of “coating removal”. A contractor can be financially burned by underestimating a job, but can lose the bid if they pad the bid for too many unknowns. One of the myths is thinking you know everything you need to know about coating removal because I have personally heard way too many stories to the contrary from some really elite operators.
My suggestion is to slow down. Create a plan that includes some contingencies. Only the shipping companies reap benefit from next day air shipping charges of heavy metallic tooling, and the downtime for your job adds to your costs. When you are performing the work, make certain you fully work your plan and make timely changes when necessary.
Many new technologies in machinery and tooling are being developed all the time. It may be a powerful competitive advantage to keep pace with some of the new technologies. A word of caution from an old engineer like me, some tooling has a very specific purpose and its true value might not be evident on every job. No one tool does everything and if you only have a few different tools in your toolbox, you might be at a competitive disadvantage.
Myth #1, I did a job in the past with a similar looking coating and I have a tool that works every time. Many contractors can be (quite frankly) very lucky and do a series of jobs without any problems until they discover to the contrary, ignorance of what those potential problems are can be bliss. It is not uncommon for me to receive a telephone call from a colleague or a customer on a jobsite that ran into some coating removal problems they never anticipated, and unanticipated problems frequently end up driving up the labor costs.
Understanding coating removal can be simplified to the two basic areas of concern, the coating and the machine (aka the “tool”) to remove it. As we can address in other myths, the skill of the operator as well as many other variables can also have a major impact, but for Myth #1, I will address the coating and the tooling.
The coating can look very similar to other coatings, yet have very different properties like how hard, how tough, the tensile strength, the gumminess, how brittle (or flexible) and how abrasive (or non-abrasive) the coating is. Some high build up coatings may have different properties in each layer. More importantly might be how well the coating is bonded to the substrate. More frequently than not, parts of the floor will have a better bond to the substrate and can be much more difficult to pull up. Sometimes areas on the floor might have a damaged substrate that was filled and covered with a coating thus creating a very different bond.
There are four distinctly different types of coatings, including synergistic coatings (chemical/petroleum/organic stains, acid stains, dyes, densifiers, curing agents, admixtures), topical coatings (sealers, paint, epoxy, polyaspartics, urethanes, elastomeric/waterproof membranes, waxes), caps (polymer modified cements, overlays, trowel down epoxies) and coverings (tile thinset, carpet glue). There are different tools and techniques specific to each of these types of coating removal.
Because there are so many different coatings, there are various tools available for coating removal. This article is limited in scope to grinders (rotary and planetary) but other tools are available including chemicals, chisel scalers, scrapers, shot blasters, scarifiers, scabblers, and shavers.
Tooling from grinders range from metal segmented diamonds (different mesh size/grit, bond, contact area and shape/orientation), beads, spikes, vacuum brazed tools, bush hammers, scrapers, and polycrystalline diamonds (PCD’s). The selection of the tool should be based on both the properties of the coating and the machine it is used on.
Rotary and planetary grinders are very different in the mechanical grinding action and the effectiveness on coating removal. Rotary grinders are much better at cutting into the coating, especially with the orientation of the tooling, whereby the planetary machines are designed more for polishing with a cutting pattern more like a Spirograph. The effectiveness of a planetary machine can be optimized for coating removal with the right tooling but it is still primarily a polishing machine.
The speeds and contact pressure on the tooling can also have a huge impact on the effectiveness. It is also important to note that many slabs have a natural undulation of about 12” whereby a small rotary grinder with a head diameter of 12” or less can follow the contour of the slab surface and machines that are larger will need to knock down the high spots in the floor undulations to fully remove the coatings in the valleys between the high spots.
Many machines use a system to change tooling quickly. One of the advantages of this type of tooling is that it allows the operator to work the floor with the best value tooling (considering both labor and tooling cost) and work the floor at a normal pace leaving behind islands of areas that need more attention or a different tool, then go back and work those areas with a more effective tool. On many jobs, several different tooling changes are not uncommon to keep labor costs down.
Myth #2, when you are removing an old coating, it doesn’t really matter what they plan to do with the floor when the coating is gone. In my early days in this industry I was constantly reminded that I was either removing a coating or prepping for a new one. Look at the big picture and know that if you save time on the coating removal but damage the substrate in doing so, thus creating more work on the surface prep for the new coating, you gain nothing.
Myth #3, wet or dry, it is just for dust control and doesn’t matter for the tooling. Dust control is a very important part of the job and many contractors set up trucks with dry HEPA vacuums and are not prepared for wet grinding steps. In coating removal, this can be a costly mistake. On thick gummy coatings using carbide scrapers, it is ok to run the machine dry to minimize the mess to clean up. Side note, on some coatings you might even lift the dust skirt to keep the gummy material from packing under the machine head. If it is really gummy, you can use a fine sand for the gummy coating to bond to and ball up instead of smearing. For diamond grinding steps, the grinding speeds can be increased with changing the disk speed (usually slowing it down to allow the bond to act softer and expose new sharp diamond crystals on the tooling face) or adding water, just enough water to create a slurry paste to help keep the diamonds cool and increase the abrasiveness on the tool to open up and expose new sharp diamond crystals.
Some acrylic sealers burn at temperatures below that which a dry grinding will reach. It can glaze over the tool face and create black splotches on the floor surface. Adding a little water to keep the acrylic cool will greatly increase the effectiveness of the tool.
Myth #4, a good test patch on the floor will tell the whole story, no surprises. It continues to surprise me on how many times contractors do a test patch to bid the job on a cold day and perform the work on a really hot day, with the properties of the coating drastically changing based on the temperature. I also see jobsites with different similar looking coatings on different parts of the slab. The coating they use to designate forklift traffic might be totally different than the pedestrian paths.
Another consideration might be the machine, tool and operator that performed the test patch might not be the same when the job is performed. The planning process should include some contingency plans.
Myth #5, the machine doesn’t communicate. Coming from an engineer, the machine speaks volumes. If the substrate has many cracks and the weight of the machine is bearing down on the tips of PCD’s, the pounding on the machine can be heard and felt by the operator. This is one downside to remote controlled machinery, the vibration felt in the handle of a standard machine can let the operator know they have a problem. Sometimes the labor savings of the tooling can be offset by the damage to the machine from the pounding vibration (damage can include the PCD tooling, the mounting plates, flex couplers, belts/gears, and even the welded frame of the machine).
Most of the time it is the PCD tooling that causes machine damage because of the load concentration on the tips of the PCDs. You can also get PCDs with a wearbar to minimize the amount of drop of the PCD point into a crack in the slab. The idea is to prevent excessive pounding. Many PCD tooling also have shapes to spread out the working load from the machine to also minimize the pounding.
There are many other myths that we frequently hear. Don’t be afraid to ask questions from the technical support folks at your diamond tooling source so you can fully understand the tooling you selected for the machine you are using. Consider evaluating different tooling options on a job to see if your original approach as bid in the job is really the best option for the job at hand. Never assume any two jobs are the same.
Like I stated previously, my suggestion is to slow down. Create a plan that includes some contingencies. When you are performing the work, make certain you fully work your plan and make timely changes when necessary. Do not let the myths in coating removal cost you time and money.