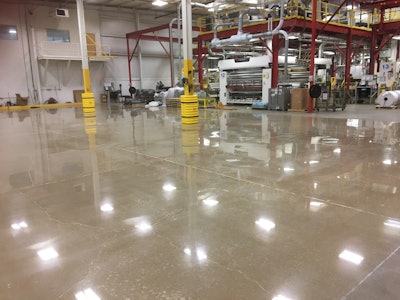
Next Generation Films, Inc. manufactures food grade plastics and is the largest custom blown film company in North America. Increasing sales has fueled expansion at its Lexington, Ohio facilities. Producing products for the food industry required floors in the manufacturing area to be dust-free with superior wear characteristics. Additionally, the surfaces had to deliver superior reflectivity and be easily cleaned to minimize long-term maintenance costs.
John Leedy, Corporate Development Director for Next wanted to improve upon the wear and maintenance characteristics he previously experienced with conventionally polished floors. He found the gloss and sustainability of newly polished floors quickly degraded, resulting in frequent maintenance and re-polishing. Additionally, demands to increase manufacturing output had him interested in finding ways to accelerate the project’s completion date.
Leedy consulted with Mark Fanello, owner of Fanello Concrete, contracted on a separate project for Next. They evaluated the benefits offered by the MQ SlabArmor system and decided to try the products in a new construction project to see if they delivered the required results.
The concrete was placed and finished by Sloan Concrete of Ashland, Ohio utilizing SlabArmor Starter and Closer. The SlabArmor Curing System increased the durability and hardness of the floors by consolidating the surface cap and producing a highly refined, less permeable, and abrasion resistant surface.
According to Ben Wiese, Product Manager at Multiquip, the SlabArmor product is a two-step process. The process was developed for application on slabs where maximum hardness and durability is required. An added benefit is the surface resistance to spills and staining when compared to conventional industrial slabs.
“The wear characteristics are comparable to dry shake hardeners and trap-rock while providing a more economical construction cost,” Wiese notes.
The chemical properties of SlabArmor allow the contractor to integrally apply the material into the concrete during placement with an additional topical application during final finishing. Both applications require minimal equipment and labor, essentially a sprayer, as opposed to other options such as trap-rock or dry shake pigments.
Five days after the pour, Fanello Concrete cleaned the surface with SlabArmor Plus Condition & Restore and prepared and sealed the joints. The floor was fully refined by diamond polishing and protected with SlabArmor Plus Seal & Shine seven days after the pour. Only ten days after placing concrete, over 1,500,000 pounds of manufacturing equipment was moved into the building – including a 55,000 pound crane. The new 80,000 square foot manufacturing facility was delivered eighteen days ahead of schedule!
“Having our manufacturing equipment in place a full two weeks ahead of schedule is an enormous benefit for us,” says Leedy. “We were able to ramp up production sooner and meet our customer’s delivery requirements.”
“Additionally, the polished surface we required is sustainable and doesn’t degrade even after several months of heavy use providing huge savings over the long run. This is the only system I’ve seen to deliver a high performance surface for our manufacturing environment.”