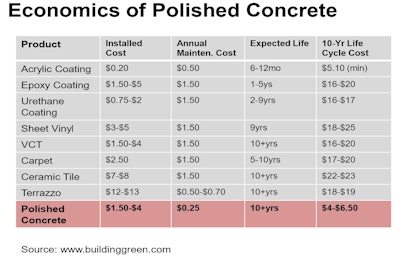
Everything looks great when it’s new. Everything. Flooring is no exception, and polished concrete floor systems glow as owners take over their buildings. However, time passes, and that initial glow begins to fade leaving building owners everywhere scratching their collective heads and questioning what happened to that glowing floor. Usually those questions lead down dozens of rabbit holes, but the reality is that the most likely suspect is simply a dis-organized or non-existent ongoing maintenance program.
While the maintenance program may be the guilty suspect, the polished concrete industry could be prosecuted as accessories to the crime. As polished concrete floor systems gained a foothold in the realm of commercial flooring, all too often “no maintenance” or “worry free” were terms used in the sales process by manufacturers and polished contractors alike. The term no maintenance was never intended to be truly no maintenance. After all, is you have a commercial carpeted floor certainly you need to vacuum or a commercial tiled floor certainly you need to mop and wax. However, many owners took the term at face value and bought into an ideology that while not completely un-true was misleading. At some point, the polished concrete industry changed the vocabulary. Today’s reputable polished contractors and manufacturers speak in terms of “low maintenance” flooring, and polished concrete floors are truly a low maintenance alternative in commercial flooring.
What does “Low Maintenance” mean?
“Low” anything can be misleading as well, though. In considering floor systems it’s important to analyze the annual maintenance costs of multiple types of commercial flooring to determine polished concrete as the “low maintenance” alternative. According to www.buildinggreen.com polished concrete has the least expensive annual maintenance cost of any commercial flooring system. Per their chart, polished concrete’s annual cost is $0.25/sq. ft. in contrast to several other systems which have higher annual costs solidifying polished concrete as the “low maintenance” alternative.
Where polished concrete really shines is the life cycle cost category of a given floor. A floor system’s life cycle is based on the installed cost plus the annualized maintenance at the expected life of the floor. Traditionally designers, architects, and engineers consider the floor in 5, 10 or 20 year blocks to establish the actual expense related to a given floor system. As a function of having the lowest annual maintenance cost, polished concrete also has the lowest 10-year life cycle cost of any commercial flooring.
The realities behind low maintenance polished concrete floors
While the number crunchers of the world can shout these and other cost advantages from the rooftops, the reality lies in means and methods of maintaining the floor itself. The devil, as they say, is in the details.
As a large-scale commercial polishing contractor, Industrial Caulk and Seal has polished and helped owners to maintain polished systems over millions of square feet of concrete for nearly two decades. In 2017 by popular demand from their customer base, Industrial Caulk and Seal released their Polished Concrete Best Practices and Polished Concrete Assurance Program. These initiatives have become the benchmark in ongoing polished concrete floor maintenance allowing builders and building owners to truly recognize the long-term benefits of polished concrete and develop a step by step road-map to that end.
Polished concrete floor maintenance starts with immediately addressing spills and stains. The traditional sealers associated with polished concrete are not topical in nature; they are penetrating sealers designed to fill the pores in the concrete surface. The great thing about these sealers or concrete densifiers is that they cannot be walked off a floor surface allowing the concrete to be sealed in perpetuity, however the fact that these sealers do not form a membrane on the floor surface makes the concrete susceptible to stains and spills. Those stains and spills need to be cleaned up immediately using a neutral cleaning agent. Simple soap and water may not be adequate particularly if there are heavy oils present in the spill or stain. Industrial Caulk and Seal recommends Oil and Grease Stain Remover by Prosoco. This is a poultice style cleaning agent that pours on wet but forms an instant poultice on the surface and draws the oils out of floor surface.
To minimize the effects of spills and stains to the polished concrete floor, guard products from a variety of manufacturers have become the industry standard. Though different manufacturer’s have a variety of guard products available and each has its own specific chemistry the common bond lies in the guard product being a topical solution and subsequently forming a membrane over the polished concrete floor. These products are traditionally applied during the final stage of the polishing process. Several manufacturers have created innovative products designed specifically to address spills and stains regardless of the makeup of those spills and stains. The two products most recommended by Industrial Caulk and Seal are ProtectSelect or ProtectPlus by the SASE Company. Though guards will help protect the polished concrete floor surface, these products are topical, can be walked off the surface over time, and should be re-applied at regular intervals depending on the traffic on a given floor.
Some manufacturers have taken stain prevention to the next level and offer sealers/densifiers that have stain preventative characteristics as an integral component without the use of a traditional guard product. SR2 by Ameripolish and SPR3 by the SASE Company are both relatively new products that fall into this category and that minimize the need for repeated re-application.
The next step in a polished concrete maintenance program lies in mapping out a specific daily cleaning program. That daily maintenance should include daily dust mopping and weekly, if not daily, wet cleaning. The goal behind frequent dust mopping is to remove dust and dirt particles before those particles are ground into the surface as a function of foot or wheel traffic. Soil is abrasive in nature and will eventually erode the concrete surface if not removed. Wet cleaning can include either wet mopping or the use of an auto-scrubber depending on the size and scope of the facility. It is imperative that wet cleaning only uses non-abrasive PH neutral cleaning agents. The key being in the non-abrasive PH neutral part of the equation. Abrasive cleaners of cleaners that are acidic or too alkaline in nature could deteriorate the concrete surface and most definitely will dull the surface with repeated use.
From the daily cleaning forward, Industrial Caulk and Seal recommends two additional steps in maintaining concrete floors. The first of these steps is to refresh the polish. The refreshing process entails burnishing the floor surface twice annually with high speed concrete burnishers equipped with diamond impregnated burnishing pads. These pads will remove light scratches and slight imperfections to the concrete surface that are bound to occur with daily use. The second process that is recommended is to rejuvenate the concrete floor system. The rejuvenating process includes a re-application of the manufacturer’s specific protective treatment to the floor and a high-speed burnish of that protective treatment to weld the protection to the floor surface.
Industrial Caulk and Seal is confident that the use of this system will produce a polished concrete floor that will last a lifetime. As part of the Best Practices and Assurance Program which they released last year Industrial Caulk mand Seal began to issue a Lifetime Warranty on their polished concrete floor systems provided that the polished concrete has been maintained as required. Industrial Caulk and Seal’s Assurance Program is available to builders and building owners. It includes regular visits for both the Refresh and the Rejuvenate parts of the maintenance process.
Regular maintenance is critical to a long lasting polished concrete floor and cannot be overlooked or underestimated. Though polished concrete is not a “no maintenance” commercial flooring alternative, it is definitely a low maintenance solution in commercial and industrial flooring. Polished concrete has become the floor of the future over the past decade, and with regular maintenance should become, not only the floor of the future, but the floor that will last thru the future.
Ed. Note: C.T. “Chip” Marshall is the executive vice president of Industrial Caulk and Seal Inc.. An award winning, large scale decorative concrete and concrete repair contractor, Industrial Caulk and Seal operates throughout the Mid-Atlantic and Northeast. Both Chip and Industrial Caulk and Seal can be reached through their website www.industrialcaulkandseal.com.