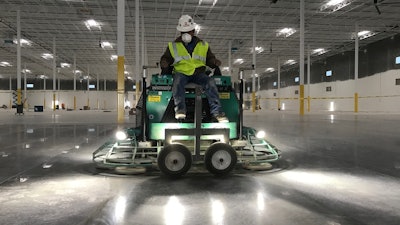
With enough people walking through retail stores, especially in a grocery setting, the polished concrete floor will eventually need attention – more than the standard maintenance it had been receiving (hopefully). Whether a new construction or not, sooner or later the owner or designer will decide between installing old traditional tile, epoxy, or a durable and economical concrete floor. In my experience, generally speaking, the overall cost of a polished concrete floor is a fraction of the cost of tile or epoxy over the life of the building.
Should you win the bid and the project swings your way, here are a few key matters to address.
Exposed Design Group
A retail project, before.Exposed Design Group
- Avoid air-entrained concrete if possible.
- Minimize fly ash and other fillers (ideally less than 20%).
- Concrete with PSI strength between 3,500 and 5,000 is optimal.
- When finishing, the flatter the better and preferably not burned in.
Often, the concrete floor has already been placed or you’re working with a 2nd generation concrete floor, and you’re left to deal with the concrete as-is. In that case, observation and preparation become the key.
Once you have determined the age and condition of the concrete floor that you’ll be working with, it’s important to know what the customer or client’s expectations are. If there’s a specification, you generally have a good understanding of what is desired. If there is no specification, it’s a good idea to ask a few key questions:
- What kind of traffic or activity is the floor going to be subjected to?
- What is the budget?
- What type of appearance is desired?
- Does the customer want a ground concrete floor and if so, what kind of aggregate exposure is required?
- Does the customer desire a glossy appearance or is a matte finish preferable?
Determining the answers to these questions will allow you to identify the processes required to help you succeed and give your client the best floor for their project.
The same retail project, after.Exposed Design Group
The Fun Begins: Preparing the Floor
If the client has decided that a simple cleaned and sealed floor is the desired finish, the process is simple. Our standard cleaning would include abrasive pads, application of a concrete cleaner and an auto scrubber. If the floor has excessive residual curing compound or bond breakers, a mechanical cleaning may be required using sanding screens or diamond tooling. Once the preparation is complete and the floor is determined to be ready to accept a densifier treatment, you have several options to choose from including lithium, sodium, and blended products. All products vary in application methods and it’s important to understand the differences, but they all provide a dustproofed, densified, and durable surface. After all contaminants have been removed from the surface, your concrete densifier can be applied. Typically, densifiers are installed after the floor has been honed. Based on the porosity of the concrete, multiple applications of densifier may be required to get a properly densified floor.
Exposed Design Group
After determining the client’s expected finished appearance, the process starts. Diamond tooling is determined by the level of aggregate exposure. Depending on the level of grind, the hardness of the concrete, and the performance of the tooling, this process may take several passes using several different diamond grits. Edgework may be required if walls are in-place and edgework should be produced ahead of field grinding. The floor should be cleaned between grinding passes to determine the progress and ensure that diamond scratch patterns are progressing as expected. “Roughness Meters” can help you determine when the floor is ready to move on to the next diamond step.
The edges will most likely be the most scrutinized aspects of the floor. This is usually much more detailed work and often performed by hand with small grinders. There are no shortcuts in edging. If possible, perform your initial grinding steps prior to the interior wall construction, you can eliminate a lot of time by minimizing your required edgework.
Exposed Design Group
Polishing
Once the desired aggregate exposure is reached, the process of polishing the surface begins. As the polishing progresses, lithium, sodium, or blended densifier treatments are applied to strengthen and harden the concrete surface. Color may also be introduced to the floor using concrete dyes. Concrete dyes come in an array of colors and can may be added during the polishing process as well. Additionally, cementitious grout products may be utilized to fill small pinholes and pitting in the surface. Once you’ve reached the desired appearance you may want to add a repellent product or a stain guard treatment for additional protection. In the end, you should be left with a truly beautiful concrete floor.
The key to ensuring your floor continues to look beautiful and performs as intended is making sure that it’s maintained properly. It’s always a good idea to spend some time with the end-user/owner to ensure that they understand what equipment to use and what chemicals or cleaning agents to NOT use when cleaning their floor. Polished concrete floors are extremely low maintenance but they’re not “no maintenance,” going the extra mile to show the client how to maintain their investment is always good practice.
Advances in the cost effectiveness of polished concrete, in addition to the low environmental impact, aesthetically beautiful appearance, and ease of maintenance have contributed to the exponential growth of the exposed concrete floor surfaces in the commercial construction industry.
About the author
Jayson Barnhart is a partner of Exposed Design Group. Exposed Design Group strives to partner with clients to help them identify the floor that will work best for their needs and assist the client with any training or expertise required to maintain that floor for years to come. Every floor that we produce is a reflection of our commitment to excellence, we take pride in being able to say “Exposed did that!”.