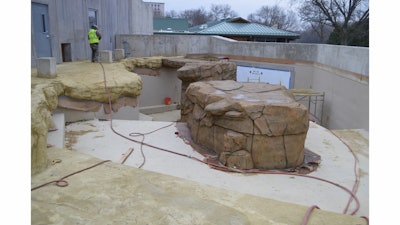
There’s something big happening at Henry Vilas Zoo in Madison, Wisconsin. The Arctic Passage, an exhibit featuring polar and grizzly bears, harbor seals and an underwater viewing area will be open for zoo visitors in 2015. Not only will the zoo welcome new animals to the zoo, but concrete plays an important role in the development of realistic habitats.
Construction firm, J.P. Cullen & Sons Inc., Janesville, Wisconsin is leading the construction of the near $10 million project. One of the largest and most noticeable aspects of the project is the number of walls constructed to create boundaries for the new exhibit.
“Every wall pour was different,” says Matt Iserloth, Project Superintendent with J.P. Cullen. “There was no gang forming on the walls. Every wall has a reveal and in some cases, there were 18-30 different reveals on each wall.”
The key to tackling the walls on this project was to have a vision drawn out on plans and designed by the architect on the job, WDM Architects. The walls were mainly constructed using Logo concrete forms. However, each wall pour required job-built wood forms in order to meet the architects requirements for the aesthetics of the walls. In other aspects of the project, the contractor used Peri Fun Flex Forms and Symons Logo forming systems.
One of the most difficult aspects of the construction of the walls was lining up all the form lines. A feat that Iserloth says required an extraordinary amount of onsite coordination.
Pouring the walls
According to Iserloth, the remodel project at the Henry Villas Zoo has been in the planning for 10 years and much of what has been torn out was built around 1970. In order to create the various elevations required in the seal pools and the bear dens, the contractor relied heavily on Revit BIM technology to map out the architect’s vision.
The tallest wall measures 34 feet tall and was monolithically poured and the average wall pour was four to five hours long. In addition to the varying degree of height and length, the typical wall in this pour was 20 to 40 feet long.
“Each wall is a different color,” Iserloth says. “Keeping them clean and crisp to keep them neat was a challenge.”
Contractors used a ¾ in. mix at 4,000 psi for all the exterior footings and walls. “When we were pouring, a lot of times, we’d pour three to four components a day,” says Iserloth. “We had to keep track with all the trucks coming in and what we had coming. Since the mix was the same throughout the project, the only difference was which color was coming in a particular truck.”
Iserloth adds the mix included a high range water reducer which helped increase the mix to a 7-in. slump. “We had no issues with the concrete, but as we were pouring and we reached the top of the wall, we had to deal with the pitch on top of the walls. In this case, for example, our first five trucks would have the high range water reducer and the sixth truck would not. We would simply pour from the last truck, groom it and walk away.”
On site, visitors will notice the different colored walls which featured Davis Colors – Mesquite, Silver Smoke and Flagstone Brown.
Building the seal pool and bear dens
A 175,000 gallon tank for the seals is part of the new exhibit. Contractors used No. 3 rebar and wire mesh to create the structure which will ultimately become the habitat for the seals. The Nassal Company has been subcontracted to perform the theming work. After the creation of the structures, contractors used Type S Mortar with an air-entraining unit from Mortar Technologies to shotcrete the structures. For the finishing touches, a water-based acrylic stain from Smith’s Decorative Concrete Products was used to stain the themed elements by hand.
“We wanted true radius walls to be visible in the seal pool,” Iserloth says. “We used the Peri Run Flex Forms, Symons steel ply forms, Logo forms and wood job built forms to create the various components. At times we had three of these form systems in use in order to achieve the correct pour and the right elevations. This was the main challenge when we constructed the seal pool.”
The new polar bear exhibit will feature a 225,000 gallon tank plus all new theme work. The area will feature various points of viewing from the concessions as well as an underwater bear viewing area. As a whole, the “bear building” is composed of exterior pre-cast walls and lid, interior poured concrete walls and retaining walls. The bear pool features a variety of steps and stairs at different elevations. It took coordination between Cullen and Nassal to make this portion of the project work, but perhaps that’s the key take away from this job – execution and coordination.
An exercise in execution
As a contractor, the journey from building plan to construction can be a challenging and daunting task. There are several aspects the concrete contractor is trying to estimate. The architect is trying to draw the vision. The engineer is trying to make sure it carries the load. Once onsite, the contractor needs to create the build out. But for Iserloth, the biggest challenge has been the logistics of bringing the vision to reality.
“Bringing the vision of the project requires manpower,” Iserloth says. “I didn’t have the manpower to do what I wanted to do, when I wanted to do it. It was difficult.”
Despite having enough crew members to get the job done, Iserloth says it’s one reason he tries to learn every sub-contractors work. “I take the effort to learn my subs work. It helps in pre-planning and when I start to look at the systems, I know more and I can conceive a better plan to the things I need to do before a subcontractor starts their work.”
He notes the key to success on this particular job was communication. Managing the logistics between subcontractors and the underground utilities required for the operation of the exhibits was a daunting challenge.
“I learned something new every day,” he says. “The coordination for underground utilities was probably one of the biggest aspects of this job. We had a lot to do in terms of coordination, but, I understand the work now, and I would like to learn more.”
“We’re going to finish something that we’ll be able to bring our kids to for years to come. There is a quality in the workmanship in a project of this magnitude and all of the components it takes to get to the finished product.”