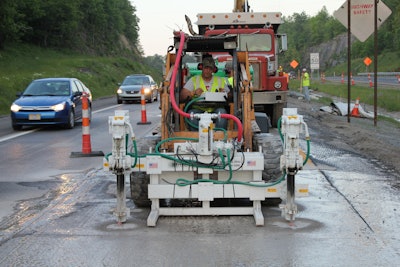
Also known as road and highway “patchwork,” full-depth repair involves cutting out and replacing damaged sections of concrete. When these “patches” are many and far apart, dowel pin drilling can be time-consuming and costly — unless you have the right solution.
Dowel-pin drill manufacturers offer machine-mounted options to help make the drilling component of full-depth repair as efficient as possible. Machine-mounted drills can be attached to tracked or wheeled excavators, backhoes, skid steers or other types of equipment to form self-contained and highly mobile drilling solutions.
What are the unique benefits of machine-mounted dowel pin drills? What factors should you consider when selecting them? Following is a guide to machine-mounted drills from Minnich Manufacturing, a manufacturer of dowel pin drills, concrete vibrators and vibrator monitoring solutions.
Benefits of Machine-Mounted Drills
Concrete dowel pin drilling is an integral part of road and highway construction projects. For these jobs to stay on time and under budget, the dowel-pin drilling component must move along efficiently and safely. Machine-mounted drills powered by an air compressor are ideal for full-depth repair jobs with relatively long distances between areas to be drilled.
Increased Efficiency
The highly maneuverable combination of a host vehicle and drill attachment increases productivity in horizontal drilling applications. For example, a drill may be mounted to the boom of an excavator or backhoe, while the air compressor is mounted to the counterweight or bucket. (This eliminates the need for a secondary vehicle to tow the compressor.) When the patch has been drilled, the operator can drive the host vehicle through traffic and move to the next patch.
The carrier already has the construction lights integrated, and everything is contained on the unit and can be moved quickly to the next patch — creating an efficient workflow on the job site. The boom of the carrier can allow the unit to be placed on all four sides of the patch without moving, which enables contractors to finish the drilling, pour the new slab and re-open roads to traffic in a shorter period of time.
Drill manufacturers also offer units that mount to a skid steer to drill vertical holes. Where there are several patches to be pulled, this pneumatically powered unit allows the operator to drive the skid steer down the road and drill two vertical holes where the slab pins need to be inserted to pull the bad slab. This is much quicker than hand-drilling these holes and does not damage the grade like total demolition and removal of the bad slab.
Improved Safety
Whether drilling is horizontal or vertical, using a machine-mounted dowel pin drills promotes safety. Many patchwork jobs require the work to be done in high-traffic areas, which make it of the utmost importance to utilize a very mobile carrier-and-drill combination. These machines also reduce operator fatigue by using the carrier to transport the drill, eliminating the need to manually move the machine.
How To Select a Machine-Mounted Drill
Contractors who use dowel pin drills have extremely difficult jobs. Combine tight timelines with the pressure of coming in under budget, and you have a lot to consider. Adding to the list of challenges is choosing the right concrete dowel pin drill for the job. There are several factors you should consider when selecting a machine-mounted dowel pin drill.
Know the Scope of Your Project
The first step in choosing the right machine-mounted dowel pin drill for your application is to understand the scope of your project. This includes:
- The number of holes you need to drill
- Your work space and cutout size
- Your timeline
- The distance you need to travel
These factors will help you determine whether to use a two-gang drill, a six-gang drill, or any drill in between. Another consideration is available side-shift functionality, which can enable operators to drill a second set of holes without having to reposition the carrier vehicle.
Consider Dust Collection
The Occupational Health and Safety Administration (OSHA) final silica rule for dust exposure is a hot topic throughout the construction industry. The construction industry’s silica rule compliance date is scheduled for June 23, 2017.
You should continue to plan ahead and, if choosing to pursue the Table 1 alternative for compliance, obtain a dust collection system for your machine-mounted drill that meets Table 1 requirements.
Table 1 states that, for tasks performed outdoors only, dowel pin drill operators can comply by using a shroud around the drill bit with a dust collection system. The dust collector must have a filter with 99 percent or greater efficiency and a filter-cleaning mechanism. According to the Table 1 section on dowel drilling, workers must also use a respirator with an assigned protection factor (APF) of at least 10.
The Minnich dust collection system, featuring Venturi-style suction and manual or automatic purge control, meets the requirements for dowel pin drills found in Table 1 when used with an appropriate filter. The filters supplied with the Minnich dust collection system comply with OSHA’s 99 percent filter efficiency requirement.
Where To Go for More Information
Dowel pin drill manufacturers and local drill dealers can help you better understand the benefits of machine-mounted drills, step you through the selection process and get you on your way to greater efficiency and safety in full-depth repair applications.
Ed. Note: Rob Minnich is vice president of marketing at Minnich Manufacturing, where he also serves as sales manager for the western region. Minnich manufactures concrete dowel pin drills, concrete paving vibrators and vibrator monitoring systems. For more information on Minnich, visit the Minnich website, www.minnich-mfg.com, or call (419) 903-0010.