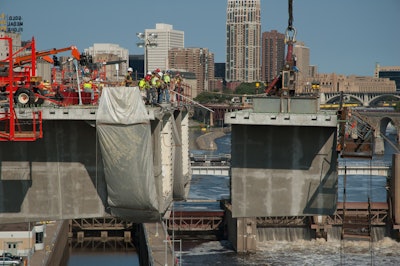
How long should a concrete structure last? Owners are asking that question and it’s natural to want them to last a very long time, especially structures which are very expensive to build. So they are beginning to specify and expect minimum life spans as much as 100 years without unusual maintenance requirements. This can be a daunting task, especially when parts of a structure are exposed to harsh elements such as bridges and decks exposed to large volumes of deicing salt and extraordinary freeze-thaw cycling each winter.
To achieve long life requires special effort on the part of owners, architects, engineers, contractors and material suppliers. Contractors are often awarded design-build contracts to do the work and therefore bear most of the responsibility to prove to the owner before the contract is awarded that the structure will perform as planned.
Specifying the long life of a structure usually involves focusing on the elements of a structure that have the highest level of risk associated with them. Rarely is money spent to maximize all parts of a structure because the cost would be prohibitive. For example, if the foundations for a structure are constantly submerged in brackish water, it’s reasonable to allocate more funds to include higher durability concrete in the foundations. Further, if they had to be repaired at some future time the cost would be very high, given their location.
As the life expectancy requirements for a project goes up so does the risk because solutions tend to fall outside the norms. Here are some thoughts about balancing structural concrete durability with cost and risk between owners and contractors.
What the owner wants
The movement to specify longer service life elements probably started with Departments of Transportation (DOT) evaluating or critical expensive bridge construction projects. Ed Lutgen, the State Bridge Construction and Maintenance Engineer for the Minnesota Department of Transportation (MnDOT) says they needed to increase the lifespans of some of their more expensive bridges and they recognized they could only do this by encouraging creativity on the parts of all the participants of a project and by trying new technology and ideas. One way to achieve this is by using design-build type contracts so that contractors have the freedom to suggest newer technology and different designs. “As an agency MnDOT works to improve quality, durability and least cost ownership. We know that experimental approaches works both ways, some ideas achieve the goals we have set but some don’t and MnDOT accepts that mistakes will sometimes happen but the risk of doing nothing is greater,” Lutgen adds.
MnDot specified 100 year service lives for the I-35W bridge over the Mississippi River in Minneapolis (the old bridge collapsed in 2007) and the new pre-cast segmental “extra dosed” bridge crossing the St. Croix River at Stillwater. Usual construction materials and methods specifications for bridges couldn’t achieve this lifespan so project participants; including design, engineering, and contractors were invited to submit ideas for consideration. Contractors were also focused on constructability. MnDot sees this process as the best way to accommodate innovation.
Lutgen says that in the ideal world owners would like others to warrant or guarantee their work for the specified lifespan of a project but they recognize this isn’t realistic—if it could happen projects would become too expensive to build because construction teams would want to pass on the costs for bonds needed to back up the warranties.
One way to avoid this conflict is to require a maintenance contract for the structure over the first several years of construction, or to enter into Public-Private Partnerships where the design builder is also owner and operator. This can involve tolls or a fixed fee from the DOT.
What Determines Structural Life
Some parts of a concrete structure are always more vulnerable to premature aging than other parts. Elements exposed to severe environments are where costly repairs occur. Traditional contracts between owners and contractors typically don’t encourage anyone to come up with better approaches.
Some environments that reduce concrete service life include the following:
- Concrete exposed to multiple freeze-thaw cycles each year
- Salt water environments—pavement and bridges exposure to deicing salts and ocean saltwater spray on bridge piers and other parts.
- Footings and foundations submerged in brackish water
- High wind loads on super-tall buildings and other structures
- Lack of protection for steel reinforcement
- Fires and blasts
- Excessive loads
Breakthroughs
When you are challenged to extend the life of a structure beyond the normal life expectations you must focus on what is presently known and future predictions. Building a super-tall building is a good example. High-rise structural concrete buildings are typically designed to withstand a minimum fifty year wind event but super-tall buildings (most all are structural concrete constructions now) are so expensive and pose so many additional challenges that owners and engineers plan on a minimum one hundred year wind event and models are subjected to wind-tunnel testing during the design process.
Newer technology helps to increase lifespan. Here are some examples:
Software. It helps design and construction at every level. Engineers use several software programs to analyze the behavior of structures under every condition available and plan for reinforcement. Contractors use programs such as building information modeling (BIM) to model and understand their work better: analyze, schedule, detect conflicts, do layout work, order materials, and cost account.
Reinforcement. Often the “Achilles Heel” for concrete, when reinforcement corrodes and expands concrete, deterioration follows. Fiber-reinforcement polymer (FRP) rebar, stainless steel rebar, pre-stress and post tension reinforcement, and fiber reinforcement are ways to limit corrosion.
Electronic monitoring. Knowing how a structure behaves over time builds on our body of knowledge and provides early warning to maintenance issues. Electronic sensors can measure stress, chloride penetration, moisture content, temperature, and vibration.
Modelling. The industry has developed a number of models to simulate the performance of structural elements on the basis of exposure and transport properties of the concrete. This is essentially the same process used for structural design. The Engineer constructs a mathematical model based on the environmental loads, dimensions and material properties.
The lack of a North-American based code complicates this modelling, as the fib 34 model relies on the NT Build 492 testing that does not have an ASTM equivalent.
Contracts. Integrated project delivery (IPD), design-build, and performance contracts are ways encourage more innovative approaches. But when contractors suggest creative or new owners may require assurance in the form of warranties for limited periods of time.
How to achieve a 100 year service life
There are a number of ways to increase the durability of concrete and therefore its service life. When designing concrete mixes consider the following:
- Use non-reactive aggregate
- Limit concrete shrinkage
- Use well-graded mixes with the largest top-size aggregate possible
- Design high density mixes
- Design mixes so that large aggregates are in contact with each other
- Include pozzolans and keep total cementitious weight as low as practical. Cement paste should be kept to the minimum amount required to fill the voids in the aggregate and a small fraction to allow flow.
- Keep water-cement ratios low to provide an acceptable diffusion value. .
Steel reinforcement in concrete must be kept dry and chloride free. Once the chloride ion content is high enough, steel corrodes and expands, breaking up the concrete surrounding it. The best way to prevent moisture from penetrating concrete and wetting reinforcement is to use high density concrete mixes, provide adequate concrete cover, and keep cracks small enough to prevent water penetration. Lutgen says MnDOT decided to replace steel rebar with stainless steel in bridge decks to avoid the corrosion problem. “Reinforcement costs up to four times as much but that is justified by low maintenance costs in the future.” Post tension reinforcement is another way of preventing crack development in decks. Also, adding fibers to concrete is a way to prevent cracks from becoming wide enough for water to penetrate.
Monitoring structural concrete in buildings isn’t as important as it is for bridges because it is sheltered from the elements by the buildings curtainwall. Monitoring long lifespan structures that are exposed to the elements is more important and should start at about ten years. Information learned when a structure is at ten percent of its rated life should provide information about how it will behave for the rest of its life. Testing should include removing cores, electronic testing, and lab tests related to environmental exposure.
Contracts and Warranties
Lutgen says MnDot is one of the more progressive DOTs in the US in terms of its commitment to increasing the lifespan of its bridges and pavements. So they like design-build contracts because contractors have the opportunity to be more innovative in their approach to building high-traffic and more expensive bridges that will last longer. Typically contractors provide a plan along with their price that explains how they will meet life expectation requirements. Ideas are discussed and agreed upon by both sides before a contract is issued. Testing is part of this process too. But MnDOT understands that the level of risk goes up too for some innovative approaches so they want the contractor to warrant their ideas for a period of time—usually three to seven years.