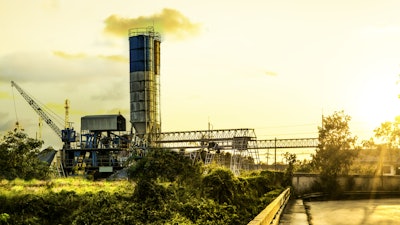
Concrete admixtures can be used to reduce cement content, permit greater use of supplementary cementitious materials (SCMs), and even increase resistance to the environment to extend the lifespan of structures. Admixtures also have the potential to affect a reduction in the CO2 emissions associated with concrete production. However, the impact of admixtures on sustainability can be complex and involve many variables. The following examples illustrate several ways that admixtures can be used to reduce the CO2 footprint of concrete.
Example #1: Superplasticizers
GCP Applied Technologies
The use of the superplasticizer allowed us to remove 34 kg/m3 (57 lb/yd3) of cement and 20 kg/m3 (34 lb/yd3) of water. Some sand can be added to the mix to maintain an equivalent yield.
The sum of these changes results in concrete with about a 9% reduction in CO2 emissions. It is clear that higher sustainability can be achieved with higher water reduction, and that there is room for improvement in this direction.
Example #2: Superplasticizers & Accelerators in SCM Mixes
GCP Applied Technologies
Starting with a mix that has 356 kg/m3 (600 lb/yd3) of cement and 180 kg/m3 (303 lb/yd3) of water, (0.51 w/c ratio), proportioned to produce a 150 mm (6”) slump.
Using a similar dose of superplasticizer to example 1, we reduce the water content of the mix to 160 kg/m3 (270 lb/yd3) and the cement content to 178 kg/m3 (300 lb/yd3). The cement removed is replaced with 178 kg/m3 (300 lb/yd3) of fly ash, resulting in a water-to-cementitious ratio of 0.45.
We are going to use the lower w/c and a set accelerator to overcome the extended set times and the lower early strengths associated with this high cement replacement level. The dosage of the set accelerator will depend on the ambient conditions at the time of placement. Later-age strength is typically not an issue for fly ash mixes. The sum of these changes results in concrete with a very significant 43% reduction in CO2 emissions. If allowance for slower strength development were possible, thus allowing less accelerator use, the CO2 emissions would be further reduced.
GCP Applied Technologies
Creative use of concrete admixtures, alone or in combinations, can be used to make significant reductions in CO2 emissions associated with concrete production.
Environmental assessment comparisons of the concrete were used to determine the CO2 emission reduction.
Diego Granell is a Director of Product Management and Marketing at GCP Applied Technologies in Cambridge, MA. He is globally responsible for development and introduction of new cement additive and concrete admixture products and systems with a strategic research focus on technologies reducing embodied carbon in concrete mix designs. Diego received an M.S and B.S. in Civil Engineering from the Technical University of Valencia, and an MBA from Dartmouth College’s Tuck School of Business.