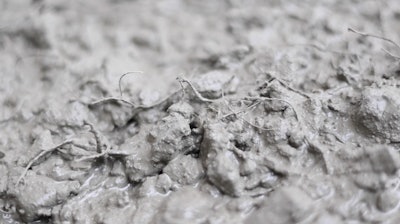
In the wake of a global pandemic, widespread supply chain issues and inflation on the horizon, the construction industry has had more than its share of speedbumps over the past few years. Fortunately, builders were considered essential in most places, allowing the pace and volume of construction projects to weather the storm relatively well. While all this has been occurring, many engineers, architects, owners, and contractors have increasingly realized that synthetic macrofibers can replace steel in a number of applications, speeding their construction schedules and reducing overall construction costs.
Decades ago, I served on the Strategic Development Committee at the American Concrete Institute (ACI). During this time, the committee produced a report stating that most innovations in the concrete industry take almost two decades to become a common practice. Innovations face particularly strong headwinds in the concrete construction industry. Engineers and architects must manage the risk of liability, so few want to be the first to try anything new. Contractors, on the other hand, prefer to do things the way they have been done in the past as this familiar routine generally makes it easier to estimate and construct. That said, synthetic macrofibers have been around for more than 20 years, increasingly gaining market share (versus steel) even before the last few years’ disruptions. However, when recent inflation impacted steel prices, the growth of macrofiber usage has only accelerated as a result. Techniques used to finish FRC will impact its final appearance.The Euclid Chemical Company
Why has the demand for synthetic macrofibers exploded? Cost is certainly one of the key drivers. When macrofibers are used in slabs-on-grade, elevated slabs, pavements and other applications, this eliminates the labor costs associated with #3 or #4 bar and welded wire fabric. In other words, no labor is needed to install steel, place it on chairs or move it to the upper floors. Add in the cost of steel you don’t have to buy, and the savings can be significant. On projects in the South Central U.S. alone, I have seen $0.50 to $1.10 savings—per square foot! That’s a $100,000 savings on a 100,000 ft2 project. It is easy to see why the market is shifting to macrofibers at a significant rate.
Who is using macrofibers in lieu of steel rebar? One such company is Tesla, which recently used 5,000,000 ft2 of macrofibers for the construction of their new gigafactory. Amazon has also used macrofibers on countless large distribution centers. Similarly, FedEx, Tractor Supply, Walmart and many other retailers are increasingly building with macrofiber as well.
The Euclid Chemical Company
Choosing a Synthetic Macrofiber
With the economic case so strong, the market is shifting rapidly. Speed of construction continues to drive the concrete construction industry, while macrofibers significantly cut time from the project schedule. So, the question becomes: how do I know which macrofiber to use?
To answer this question, there are significant intangible factors that must be considered. For instance, how does the concrete finish with the macrofiber in it? Is the macrofiber creating a “furry” slab? Does it pump well? Does the manufacturer support the contractor at the site when the placement begins? (This is a critical point, especially if the construction crew has not placed macrofiber concrete before.)
Some of the biggest factors to consider:
1. Macrofiber Pumpability. What can be done to improve the pumpability of a macrofiber mix? For most cases, a good pumpable mix can accommodate fibers with little to no adjustments made. Oftentimes in the field, because fiber-reinforced concrete functions differently, users will want to add water to make the concrete more workable. This can worsen the situation, as too much water will actually cause a mix to segregate and can ultimately block a pump hose.
When discharging a fiber-reinforced concrete (FRC) mix into a hopper assembly on a pump truck, raise the chute to 18 inches (300-450 mm) above the grate on the pump to allow for the fibers to ‘impact” the grate and help them pass through. A working vibrator on a grate will also improve the concrete’s ability to pass through the grate. Synthetic macrofiber reinforcementThe Euclid Chemical Company
2. Finishing Macrofiber-Reinforced Concrete. If reducing the visibility of macrofibers on the finished concrete surface is desired, it’s important to start with a properly proportioned concrete mix to accommodate fibers, as well as ensure that a mix is not over-watered to improve flow. The use of water-reducing admixtures to maintain strength while improving workability is always recommended. Timing of the finishing operation can sometimes be tricky because the FRC may look like the concrete is setting up more quickly due to the cohesive nature of the material.
How the finishing of this concrete is actually completed will make a huge impact on its appearance. First, it is critical to hit the surface with a vibratory screed. If not done, this will likely result in “furry” concrete, no matter what fiber you choose. After this step, you can finish the surface with pans or trowels, just like you would do with regular concrete.
If you are looking to achieve a broom or tine finish, it is very important that you do it in one pass and in one direction. Ensure that the equipment used to apply the broom finish is maintained in a clean state and that the angle of the broom is low. Broom finishes will usually pull fibers of any type to the surface of concrete, but experience has shown that “practice makes perfect.” Self-fibrillating macrofiber does not have as much of a tendency to be pulled to the surface during finishing operations, making this type of fiber an ideal candidate over steel fibers, which tend to be more rigid and can cause problems along joints when saw-cutting operations are underway.
It is always good to have the fiber manufacturer on site for the first day of placement and, if necessary, perform a trial or mock-up prior to concrete placement to assist the contractor in obtaining the desired surface appearance. Synthetic macrofiber reinforcementThe Euclid Chemical Company
3. Flexural Strength. Another important differentiator between macrofiber types is flexural strength. The same dosage rate does not provide the same flexural strength when comparing most fibers. ACI and the American Society of Testing & Materials (ASTM) have standards that make this part easy to understand.
Macrofibers should be tested in accordance with ASTM C 1609, Standard Test Method for Flexural Performance of Fiber-Reinforced Concrete, which will provide a residual strength based on the dosage. The results of this test method are used for comparing the performance of various fiber-reinforced concrete mixtures, monitoring concrete quality, verifying compliance with construction specifications or evaluating the quality of concrete in service. It is especially important to have ASTM C 1609 results if you are considering more than one supplier of macrofiber.
Over the past several years, we have seen an increased interest in the use of macrofiber-reinforced concrete in concrete pavement applications, such as parking lots, bridge decks and roadways. ACI, the American Concrete Pavement Association (ACPA) and the National Concrete Pavement Technology Center (NCPTC) have each developed guidelines and recommendations on how to properly select and use fiber-reinforced concrete: Broom finishing macrofiber-reinforced concrete.The Euclid Chemical Company
- ACI PRC-544.4-18: Guide to Design with Fiber-Reinforced Concrete
- NCPTC Fiber-Reinforced Concrete for Pavement Overlays
- NCPTC Overview of Fiber-Reinforced Concrete Bridge Decks
Recent Projects Utilizing Macrofiber-Reinforced Concrete
SoFi Stadium—Home to the Los Angeles Rams and Los Angeles Chargers
The SoFi stadium, located in Inglewood, California, was constructed by a joint venture between two general contractors. The stadium seats 70,240 spectators for most events, with the ability to expand it with 30,000 additional seats for larger events. It is located at the former site of the Hollywood Park Racetrack, three miles (4.8 km) from the Los Angeles International Airport.
As opposed to conventionally reinforced slabs, these fiber-reinforced concrete slabs:
- Prevents corrosion over the lifetime of this facility;
- Provides improved crack control for this topping slab;
- Allowed construction time to be reduced, as the use of macrofiber eliminated the time to crane lift and install welded wire fabric or reinforcing steel; and
- Improved job-site safety by eliminating tripping hazards for the concrete placement crew.
Macrofiber reinforcement provides cost savings over rebar and welded wire.The Euclid Chemical Company
Highway Rehabilitation in Fowler, Indiana
The Indiana Department of Transportation (INDOT) is also utilizing macrofiber reinforcement with thin concrete overlays for highway rehabilitation. Constructed in 2018, the section of US 52 outside of Fowler, Indiana, was rehabilitated with a 4 to 4.5-in. concrete overlay using a 4 lb./yd3 (2.4 kg/m3) dosage of macrofiber. This four lane highway was previously surfaced in asphalt and had reached a deteriorated state that required a long-term solution and improved ride quality.
The project utilized a twin-shaft portable mixer placed at its local dry batch plant location. This combination of mixers allowed for the production of up to 100 yd3 per hour, with the placement of between 500-900 yd3 per day. In total, over 18,500 yd3 of macrofiber-reinforced pavement was placed without the use of any dowels or reinforcing steel. This showcases a major market potential for future FRC and pavement projects in the industry.
Synthetic macrofibers have passed the test of time and are being used on hundreds of projects of every size. With cost savings of as much as $1.10 per ft2, the use of macrofiber is booming in the concrete construction industry—meaning we will likely continue to see its rise in 2023 and beyond.
About the author
Vance Pool is manager of the National Business Development Group at Euclid Chemical, a leading manufacturer of specialty concrete and masonry construction solutions. He has been actively involved in the concrete construction industry for four decades. To learn more, visit www.euclidchemical.com.