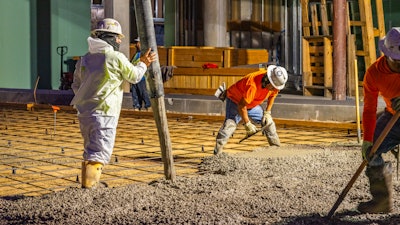
Fly ash has been one of the most common supplementary cementitious materials (SCMs) for decades. While lowering the cost per unit of concrete by replacing cementitious material in the mix, contractors have also found the SCM provided benefits like an improved strength, durability, workability, finishing (among others). Not to mention the opportunity to reduce CO2 emissions along the cement-to-concrete supply chain.
Fly ash from coal fired furnaces have slowly become less available. To put this in perspective, during a presentation within the Portland Cement Association’s 2023 Sustainability Summit, Ross Gorman, manager of technical services with the SEFA Group, stated that the production of coal ash has fallen from 140 million tons (2007-2009) to about 69 million tons in 2020.
Bill Yearsley, CEO of Terra CO2 Technology sees SCMs as a powerful way to not only have some control over the cost of concrete but providing one more level for the concrete industry to pull to minimize CO2. While the industry won’t likely run out like toilet paper from shelves, he understands that research on new solutions will be vital for the industry.
Representatives from Terra state that “OPUS SCM is intended to fill the void that fly ash and blast furnace slag are leaving because both are going away. Fly ash with the closure and conversion of coal-fired power plants and blast furnace slag is changing because steelmaking is changing. So you know, it's important for the industry to have a new product that can be scaled and reliable and cost competitive."
“SCMs are cheaper than the portland cement they displace and add performance qualities, where you’re trying to mitigate reactivity – if there aren’t new SCMs and the old ones [like fly ash] go away, the only alternative is to use more portland cement or 100% portland cement mixes, which is going to result in more CO2 emissions,” Yearsley says.
With the decrease, people have started work on developing alternative options – some to recycled products like that from SEFA Group which utilizes the fly ash stored in impoundments; others to engineered SCMs like OPUS from Terra.
Terra is a manufacturer of the scalable low-carbon alternative for cement production called OPUS. They have a pilot facility in Colorado, but it’s not available at a commercial scale yet. They are currently working with general contractors for a handful of demonstration projects around the country to put the material to test and further proof of concept.
Terra’s OPUS SCM has been used in Colorado as well as with the Minnesota Road Research (MnROAD) Facility on Interstate 94. Where 20 tons of the SCM were used without the need for adaptions for new investments. Larry Sutter, from Sutter Engineering LLC who managed the technical aspects of the project such as testing constructability and performance evaluation, explained in the September 2022 release that the project’s specifications were based on performance instead of a specific concrete mixture. “[This allowed] the additive suppliers to push the boundaries of cement substitution,” he says. According to the announcement, the concrete featuring Terra’s OPUS met the target flexural strength and compressive strength in “half the usual time” even though it was utilized at the highest substitution level of all the SCMs tested (35%).
Terra’s team of industry veterans is led by Yearsley, with over 40 years of experience in the construction industry, and by Founder and Chief Science Officer DJ Lake, an expert in alternative cementitious materials. Their team recently expanded with the addition of several industry veterans from the building materials sector. The company was founded in 2015 and has raised $61 million in venture capital.
G. LYON PHOTOGRAPHY Inc.
Green concrete for Porsche
Based out of Houston, Christensen Building Group (CBG) is a traditional general contractor and construction management firm. With a work portfolio of roughly 50% commercial to 50% industrial projects, they reach a lot of different market sectors from municipal projects to office space. Founded in March 2014, a large portion of their work is also in the oil and gas support side. They target the challenging projects that need a solution – and need a partner to help them resolve it.
“Texas has a big footprint in that [oil and gas] world, especially Houston,” says Mark Christensen, president of Christensen Building Group. “It’s exciting to be a part of a technology that’s moving in the direction of improving our environmental footprint of what we do as an industry.”
Christensen and CBC are familiar with Terra’s OPUS product; the team were brought on roughly a year ago for pre-construction and are moving towards the design completion of their first commercial plant. With a background in general contracting and construction materials production, Yearsley understands the value of bringing in the GC during the design phase. “They can help with value engineering, they can help with budgeting,” he says. The commercial plant is expected to be able to produce 250,000 tons of product annually.
The OPUS SCM concrete placement completed late July 2023, with the OPUS SCM pour reaching the 28-day mark on August 24. IndiGO Auto Group, the owners of the dealership, and Porsche have a strong focus on sustainability with the manufacturer’s move towards electric vehicles and the electrification of their infrastructure. Understanding that focus, Christensen brought suggested to the owners that the project might make for a good demo with the SCM. “They welcomed that immediately and recognized the benefit of decarbonizing their structures,” says Christensen.
“We are thrilled to be the first pour in Texas, and we look forward to using Cement for Humanity in our future projects. Reducing our carbon footprint is at the top of mind for indiGO Auto Group and finding innovative ways to do it is part of our culture,” says Kelly Wolf, CEO of indiGO Auto Group.
For the OPUS placement, CBG felt the facility’s entrance feature would be a place for something meaningful and placed 240 cubic yards of concrete. Terra provided about 5 tons of OPUS material to use in the mix design. They partnered with Houston-based A.G.E. Construction as the concrete subcontractor, Odi & Son Concrete Company for the concrete ready-mix supplier as well as Dally + Associates for structural engineering.
G. LYON PHOTOGRAPHY Inc.
“Of course, we couldn’t have don’t it without all the boots on the ground – the guys that batched it, that placed it, that got up early in the morning and go be in the Texas heat to make it happen,” reminds Christensen. “Those are the real heroes that make the rest of us look good.”
Before placement, CBG tested the mix design ahead of time with independent lab tests on four different occasions to satisfy the engineers.
Christensen explains that no changes to the design or work were needed. “We use utilized the same mix design and substituted the fly ash mix one for one,” he says. “It was a seamless utilization into the project. The crafts people that were placing the concrete couldn’t tell a difference. It went down and finished just like the other concrete that had been placed on the project.”
CBG used one of the most common mix designs for the region: a 3,500 psi with a 20% fly ash substitution. Subcontractors reported back to CBG with praises on the workability and Christensen says he was told by the subs that it went down like the previous hundreds of cubic yards of concrete prior.
Cylinder break tests exceeded performance. The mix met 75% to 80% strength at seven days – and reportedly 10% better than their fly ash mix – with a successful 28-day break test. (Editor’s Note: While the 28-day mark was August 24, they broke some cylinders one day early for an Augst 23 interview.)
Despite the project’s overall success, batching was the largest challenge. A problem they were able to overcome with good old-fashioned hard work.
Unfortunately, Christensen explains that the amount of OPUS SCM used for the project wasn’t enough for a ready-mix facility to displace its fly ash silo, yet too large of a pour for a small mobile mixer. The material was delivered in 1,000-lb. super sacks to the jobsite and teams (with the appropriate PPE) used five-gallon bucks to add the material into the trucks.
The dealership entrance featured a broom finish and will include a bronze plaque to identify Porsche Sugar Land, IndiGO, the date of placement, Cement for Humanity (Terra’s trademarked organization face of the OPUS demonstration projects), Terra CO2 Technology, and partners of the project.
G. LYON PHOTOGRAPHY Inc.
"Pioneering the use of a supplementary cement in Texas, like Terra's OPUS SCM, is monumental because it not only matches the performance of traditional SCMs, like fly ash, but also significantly reduces environmental impact without any changes to the conventional workflows of concrete batching and placement," says Christensen. "Decarbonizing construction is a climate imperative, and we’re excited to have partners like Terra and indiGO that are committed to making a real impact in Texas and across the industry.”
With the client pleased about the placement, they’ve requested CBG to utilize the SCM on future work.
“Now I get to ask Bill to get me more of that stuff so we can keep our folks down here satisfied,” Christensen says.
“Every project has a different mix design,” explains Yearsley. “But much like Mark did in Texas, we want to work with existing common mix designs for the type of project and location. We want to show that our material works within the existing infrastructure both in terms of engineering mix design as well as concrete trucks pumping this material. It’s proof of the workability and reliability of the material.” Terra hopes to add another demonstration project, a different geography and different type of project every two to three months.
A solid composition - About OPUS SCM
Terra’s proprietary process uses widely available silicate-based raw materials, which are among the most abundant materials on Earth. By locating plants on or near existing aggregate mines broadly found across large urban centers, Terra is reducing transportation costs and leveraging existing infrastructure, eliminating the need to permit new mines to source raw materials and the expense of transporting raw materials across long distances.
FastCompany.com’s Adele Peters wrote about Terra’s OPUS back in July 2022 when they announced $46 million in a series A round of funding led by Gates Foundation’s Breakthrough Energy – the organization’s fund focused on carbon reduction – and LENX, the investment arm of Lennar, one of the largest construction companies in the U.S.
In the article, Yearsley explains that Terra works with silicate rock types, one of the more abundant types of rock on earth’s crust.
Material testing conducted by Alpha Testing confirms that Terra's product performs on par with traditional SCMs in terms of durability, strength, and functionality. The successful incorporation of Terra's OPUS SCM, tested by third parties, is just the latest confirmation that underscores the industry's confidence in the product and its potential to revolutionize sustainable construction.
To reach scale, Terra CO2 has developed an advanced processing facility that produces precisely engineered SCMs. For every ton of cement replaced by Terra’s OPUS SCM, it results in 70% lower CO2 emissions and 90% lower NOx emissions than original portland cement without impacting mix designs, batching, delivery, and placement of concrete.
"Our work at Terra CO2 is about forging a viable path for sustainable construction. We're set on creating a blueprint for the future where performance, cost-effectiveness, and sustainability coexist seamlessly across projects," says Yearsley. “We’re moving beyond the lab, beyond the processes that have held us back as an industry, and introducing a sustainable solution to real-world applications.”
The company manufactures three different types of OPUS:
- OPUS – the standard fly ash replacement, Terra reports it can offset the use of up to 25% of portland cement in most common concrete mix designs
- OPUS SCM+ - which features an ingredient that allows it to be substituted for up to 40% of portland cement for use in concrete and directly replace fly ash
- OPUS ACM is an alternative cement still in development, designed to be a full replacement for portland cement (expected to be available late 2024)
According to a technical bulletin published by Terra, OPUS SCM can provide similar results for time of set, workability, and bleeding in concrete compared to Class F fly ash. It followed ASTM C1709 and meets the specifications under ASTM C618.
The comparison doesn't end there. Compared with traditional Class F fly ash, "the impact of OPUS SCM on concrete water demand is generally no different," says Yearsley. Both SCMs are made up microspheres which typically improves the workability of concrete. When the mix is proportioned correctly, OPUS should provide sufficient bleed water to enable a proper concrete finish without crusting issues.
No projects have introduced color or staining concrete after curing at this time. Yearsley expects performance to be similar to concrete made with fly ash.