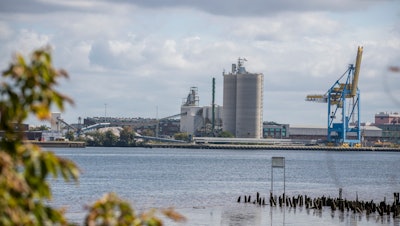
In Times Square, buildings must be larger than life. Twenty-two percent of every New York tourist dollar is spent in Times Square, and it receives 400,000 visitors per day, according to the TSX Broadway website. The TSX property—a 550,000-sq.-ft. “entertainment ecosystem” containing a mix of retail, concert space, and 661-room hotel—was completed in early 2024.
The project redeveloped an existing 1980s tower built over the circa-1910 Palace Theater. The theater interior was landmarked, but since this meant only the inside of the building needed to be preserved, the design team decided to raise the structure and incorporate it into a portion of the new building that is 30 ft. above street level. Doing so freed up ground-level real estate in Times Square’s highly-sought-after retail environment. Another challenge for the building team was that 25% of the 1980s tower needed to be retained in order to maintain a zoning exemption. To meet this goal, the structural elements of the lower-story floor slabs were retained, complicating demolition and excavation activities. Cutting-edge concrete construction techniques provided the strength and stiffness necessary for the structural systems and helped accomplish the site’s transformation from a dated, limited-use theater space into a dynamic retail and entertainment hub.
TSX Redevelopment Project Cost: $2.6 billion
Structural Features
A post-tensioned system was used to transfer loads from the old structural system to the new one and a concrete ring-beam was used to lift the Palace Theater. For below-grade construction, a new concrete system was created to support the existing structure while the foundation was lowered by 30 ft. to accommodate a new subcellar. This system redirected loads to concrete columns supported on newly installed caissons. The TSX building, Times Square, New YorkTSX Broadway
Sequencing for the project was critical. The existing hotel tower had been built around and above the Palace Theater, which occupied the corner of the block. To support the tower, super-columns had been placed at the theater’s corners and a deep truss system positioned on top of it. The first phase of construction for TSX Broadway, which began in 2018, involved upward extension of the super-columns, demolition of the existing tower from the top down to the existing level 16 slab, and foundation work.
A post-tensioned girder system was created to de-load the existing truss and provide support for the future tower. A total of three post-tensioned concrete girders, each 41 ft. deep, 4.5 ft. wide, and 140 ft. long, were installed in four separate vertical pours. Formwork was supported on the existing trusses for the first lift, which was post-tensioned using 1,700-ton stressing jacks. The girders were then constructed in 10-ft.-deep increments and were post-tensioned with each increment. Further post-tensioning occurred when construction progressed to the upper tower floors. At that point, tendon-stressing was calibrated following the construction of each 10-floor tower segment. This gave the girders a slight upward camber, controlling stresses and limiting deflection. Movements were closely monitored as construction progressed, and at completion, the girders exhibited deflection of only a quarter inch. Thirty-six high-strength tendons, measuring a total of 210,000 ft., were tensioned to 2,000 kips each.
The three girders are braced by 16-in.-thick cast-in-place concrete slabs at the 12th and 16th floors. Existing hotel tower slabs that had not been demolished were hung from the new post-tensioned super-truss, and the new truss also supports the raised theater building. It is the longest post-tensioned concrete transfer truss for a vertical building in the world.
Once the new support podium was in place, the old truss system above the Palace Theater was demolished. At that point, another of the project’s most challenging tasks commenced: a 6-ft.-thick concrete ring beam was poured to act as a base for the 14-million-lb. masonry theater. The ring beam was installed in segments at the underside of the ground floor framing by first pocketing steel posts into the walls and then replacing the brick with concrete in lengths of 30-40 ft. Shoring posts and jacks were used to raise the theater. Using the ring beam minimized the risk of cracking the theater’s masonry walls.
Concrete also helped the team achieve the 25% structure retainage requirement. The structural capacities of some existing slabs were increased by bonding them to structural topping slabs. In another location, a reinforced concrete slab was epoxy-pinned to an existing concrete plate. The resulting higher load capacity allowed for the removal of interior columns. New concrete was also used to augment the existing steel super-columns’ structures since the increase in the building’s live and dead loads meant that each super-column now must support 25 million lbs. From the cellar to the 8th floor, existing columns were encased in 14,000 psi concrete reinforced with Grade 80 rebar. Above the 8th floor, columns were entirely constructed of high-strength reinforced concrete.
Early decisions on the part of the construction team to use concrete instead of steel for the structural system were based on cost as well as the flexibility of concrete to be placed on the tight urban site.
Innovations in the Concrete Mix
High-performance concrete was a requirement for the project. Slag cement, incorporated at 40%, not only helped achieve high performance but made the mixes low-carbon. Heidelberg Materials North America supplied slag cement, as well as portland cement, to Tec-Crete Transit Mix, who supplied the concrete used in the building’s construction. Stan Trella, sales manager at Metro New York/Long Island for Heidelberg Materials North America noted that the use of slag cement was beneficial to not only 1) optimize the concrete's strength but 2) reduce the venue's environmental impact by lowering the percentage of ordinary portland cement (OPC) in the mix.
Assuming industry averages for the global warming potential (GWP) associated with portland cement and slag cement, the TSX Broadway project saved more than 6.8 million lbs. (3,000 metric tons) of CO2. (Industry averages for portland cement are published by the Portland Cement Association and, for slag cement, by the Slag Cement Association.)
A 14,000 psi (96.5 MPa) design strength mix accounted for 38% of the concrete placed on the project. More than half (58%) of the concrete placed had a design strength of at least 10,000 psi; each had a minimum of 40% slag replacement.
The 580-ft. Tall Tower
The 580-ft.-tall TSX Broadway tower represents an increase in building height of 100 ft., allowing for higher floor-to-floor heights in the new hotel. The wider column spacing on the tower’s lower levels (enabled by the increase in slabs’ structural capacities) permits flexibility in entertainment spaces. One hospitality lounge features the largest terrace in Times Square.
A highlight of the building is a cantilevered entertainment stage that is 30 ft. above 7th Avenue. A hinged LED door—part of the 18,000-square-foot LED screen that wraps around nine of the building’s lower stories—opens to reveal the stage; when closed the door is part of the high-resolution display. Other digital signage is placed along the height of the tower and at its crown, offering a total of 51,000 sq. ft. of advertising space.
Project cost for the TSX Broadway redevelopment was $2.6 billion.