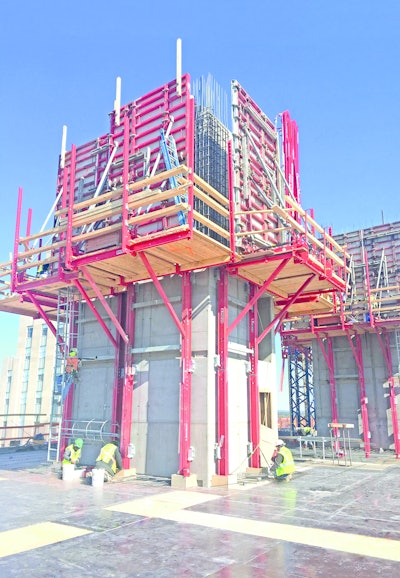
Ground broke on the new One City Center, also known as the “Durham City Center” in Durham, North Carolina in February 2016. Located in the heart of downtown, steps away from the theater district, this 350,000-plus square foot, 27 story building will feature 130,000 square feet of retail and office space, two levels of parking, and 21 residential levels complete with a rooftop pool. When completed, it will be the tallest building in Durham.
One City Center is built on the site of the old Woolworths building and is made entirely of cast-in-place concrete. Confined construction space is always a challenge in urban high-rise construction – and MEVA provided a complete solution for the contractor from the basement to the roof.
Single-sided pours in confined space
The first challenge that contractor Lithko faced was there were other buildings located very close to the construction site, limiting access for large equipment such as cranes to be on site or move – making one-sided concrete pours and a versatile wall formwork system a necessity to pour the basement/underground parking levels and the structural columns. The job required 75’ long and 25’ high single-sided wall pours on the lower levels, and MevaLite wall formwork in combination with STB 450 support frames provided the total solution.
MevaLite wall formwork for work without a crane
At only 7 to 10 lbs. per square foot (depending on hardware), the MevaLite hand-set clamp system was designed especially for concrete works where assembly and stripping are done without a crane. The two-chamber aluminum hollow profile allows for panels to be handled by hand with as little as one worker, while still achieving a sturdy pressure rating of up to 1,350 psf.
STB 450 support frames for single-sided pours
STB 450 frames can be used for pours up to 16’ and extensions are placed in 5’ increments from the top, allowing the base unit to stay intact for pours up to 38’. The frames are only 7-10.5’ wide at the base, making the STB 450 support frames the best choice for the confines of the One City Center jobsite.
According to Lithko Project Manager Andy Lindsey, “The selection and use of MEVA Formwork for the Durham City Center project was based on the flexibility of the single-sided wall formwork utilizing either MevaLite or Imperial to pour the 25’ tall single- sided walls around the entire lower level parking. Based on the confines of the jobsite, the MevaLite product line was the best option for structural columns up the entire building.”
MevaDec slab system: No fixed grid, no crane required
The building floor slabs were completed using a combination of the MevaDec slab formwork and MEP shoring. For the first six levels of construction MevaDec was used; chosen by the contractor both for its ease of use and for economy. With no fixed grid, MevaDec can switch direction to easily adapt to any slab layout and reduce filler areas. MevaDec does not require a crane and can be easily set by as little as two or three workers. This system combination includes a drop head that lowers the panel by 7.5” to allow for early stripping and cycling – saving Lithko time, labor, and material. In addition, MevaDec comes standard with the alkus all-plastic facing that delivers an even concrete surface and, unlike plywood, lasts as long as the panel frame, saving additional money and natural resources.
Transfer slab poured with the help of sturdy MEP shoring towers
At the seventh level of construction, a transfer slab to help support and evenly distribute the weight of the remaining 21 stories needed to be constructed. The slab contained 1,800 cubic yards and 450,000 lbs. of reinforcing steel over 20,000 square feet with 5’ drop beams. MEP shoring was used to carry the heavy weight of this undertaking.
On the safe side with the MEVA Guided Climbing system (MGC)
Safety is always of the utmost importance, especially when working at great heights. The MEVA Guided Climbing system MGC is the safe choice when climbing cores in high- rise construction. The entire MGC system is assembled flat on the ground, optimizing worker safety from the very beginning and saving time. Two guiding profiles are attached to each MGC unit (platform). As soon as the starter wall has been poured and the concrete has achieved the required strength, the MGC unit is erected so that its guiding profiles are in vertical position. The unit is then lifted by crane and the guiding profiles slide through the climbing shoes that have previously been attached to the wall. Claws that are integrated inside the guiding profiles engage with the climbing shoes and keep the MGC unit at the chosen height while the next higher section of the core wall is poured with the wall formwork placed on the platform. Once an MGC unit has been connected to the structure through its guiding profiles and the climbing shoes, it remains permanently connected to the structure throughout the building process, even when climbing. After a new core wall section has been poured, the climbing shoes are attached for the next lift and then the MGC is elevated one level by crane. The guiding profiles slide through the climbing shoes that are holding them and then through shoes one level higher. Since the MGC units are always attached to the structure, work is not hindered by bad weather and the units can be raised even with wind.
Andy Lindsey notes, “MEVA’s MGC along with Imperial formwork proved to not only be an efficient product when advancing the cores ahead of the decks in the tower levels, but also provided the safety factor that we consistently achieve on our job sites.”
Imperial wall formwork for the cores
Heavy-duty Imperial wall formwork was used in combination with the MGC system for the outside of the cores and the MEVA Flipper Beam inner shaft platforms. Heavy-duty Imperial with a pour rating of up to 2,025 psf aligns and securely connects panels with the MEVA clamp, and the multi-function profiles with welded-in DW nuts allow for easy attachment of all accessories with a standard flange screw, reducing consumables and easing logistics.
The new Imperial stripping corner inside the cores
The stripping corner allows panel gangs for elevator shafts to be set and stripped without disassembling the gangs. The stripping corner is designed with three pieces to allow inward movement. Minimal crane time is required because the stripping corners turn all sides of the panel gang into one movable unit that can be elevated.
Flipper Beams inside the cores
The MEVA Flipper Beam inner shaft platform is made with steel double C-channels that are custom-built and sized to job requirements. The platform is designed for a live load of 50 psf and to support the weight of formwork. The platform and inner shaft formwork including the stripping corners can be cycled together in a single pick; reducing work, saving time and enhancing safety.
Ultimately, Lithko was extremely satisfied with MEVA’s comprehensive answer to the requirements of One City Center’s construction, and they appreciated the “outside the box” thinking that MEVA presented to give them the best opportunity for success. They also greatly appreciated MEVA’s staff and their complete willingness to go above and beyond business as usual to ensure that they were successful in all matters on this job.
“Utilization of sales representative Matt Woodlief during the planning phase, as well as his dedicated weekly visits to the jobsite continues to ensure optimal use of our on-site MEVA products and he in turn helps identify materials that can be returned after their scheduled use to avoid unnecessary costs,” Lindsey says.